Robots fill gaps as processors struggle to find workers
As labor shortages, strained supply chains and other fallout from the pandemic continue to bedevil plastics manufacturers, a veritable army of robots is marching to the rescue.
U.S. plastics manufacturing employment, while growing, still lags behind pre-pandemic levels, according to the Plastics Industry Association (PLASTICS). Citing numbers from the Bureau of Labor Statistics, the Washington, D.C.-based association reported that as of May, plastics manufacturers are still 2,900 workers shy of March 2020 employment levels and factory capacity utilization rates are stagnant.
“Since January this year, capacity utilization has averaged 81.8 percent,” said Perc Pineda, PLASTICS' chief economist. “While that is an improvement from the 64 percent in April last year, the capacity utilization rate has stayed stubbornly at 81 percent. This could mean that efforts to increase output through higher labor utilization have been met with a low labor supply.”
Processors are seeing the labor shortage firsthand.
Back in January, when PMM published its annual survey of processors’ machinery buying plans, 48 percent of respondents were planning to invest in automation in 2021. One respondent commented that “it’s getting very difficult to find workers.”
In addition to adding robots to fill plant floor labor gaps, there continues to be interest in robots to replace humans in dangerous or stressful jobs, as well as for improving quality.
The labor shortage is especially acute for processors performing a lot of secondary operations, including packaging products.
This confluence of factors is the backdrop for the launch of several innovative robots and, in the case of at least one automation supplier, record sales.
Muller debuts cobot case packer
Muller Technology, a supplier of molds and automation for thin-wall packaging, is offering what it calls the industry’s first self-contained collaborative robot case packer for packaging lids and containers. The system is centered around an Omron six-axis cobot.
“The biggest thing that we’ve seen is the labor issues that were caused initially by COVID and now continue as the economy opens up, but people are not necessarily going back to work,” Taras Konowal, director of sales and marketing for North America, said. “A lot of our customers are having issues of not having enough labor, and the majority of what we’re seeing is in packing … Our customers have the molding machine. They have the mold. They have the resin, but they don’t have a person to pack the parts. So, they shut down complete cells due to the lack of labor.”
That is the single largest factor driving processors to purchase automated packing systems, Konowal said.
Muller’s new cobot packer can work side-by-side with employees doing many basic tasks. When a person nears the cobot, it slows down but continues to work. The cobot does not require external guarding and all safety features are built-in.
The cobot packer includes a Muller HMI that stores multiple recipes for a wide range of stack and box sizes. It can be purchased separately or integrated into an automation line, including Muller’s new M-Line system for removing injection molded containers from their molds.
The new M-Line take-out robot removes packages from their molds and places them on a conveyor belt for labeling or packaging.
The M-Line offers significantly greater versatility than most take-out robots for injection molded packaging, the company said.
The robot accommodates multiple mold types and from one to 48 mold cavities. The M-Line’s low-cost end-of-arm tooling can be changed out quickly, allowing for changes in the number of mold cavities and types of packaging.
“It’s a unique design where it’s highly flexible,” Konowal said. “You can run any cavitation with that same take-out robot. It takes the parts out of the mold and it stacks them all with one arm, or two arms for a stack mold, or four arms for a four-face mold.”
The system is built on one frame and has a small footprint with no assembly required. The M-Line is motorized, with no pneumatics, which dramatically reduces energy consumption and eliminates the need for shop air.
The M-Line consists of three models for various sizes of injection molding machines. Seven units already have been sold in North America.
Stäubli expands six-axis line
Stäubli recently introduced three TX2 six-axis robot models, expanding the line to nine models.
TX2 robots are suitable for mold tending, part trimming, part assembly, ultrasonic welding and packaging tasks.
The models include the TX2-140, with a reach of 5 feet, and the TX2-160, with a reach of 5.6 feet. Each has a load capacity of 88 pounds. The new TX2-160L, a long-arm version of the TX2-160, has a reach of 7 feet with a load capacity of 55 pounds.
Stäubli said all three feature repeatability of plus or minus 0.05mm, putting the robots on a par with the most accurate in the market. The accuracy is due, in part, to Stäubli developing and manufacturing its own gearbox.
“We’re the only manufacturer in the world that does its own gearbox,” said Sebastien Schmitt, robotics director, North America. “It’s allowing us to have that rigidity, precision and accuracy that we have, and speed.”
The TX2-140 and TX2-160 are replacing the predecessor model RX160, which has resulted in an additional advantage — now all of Stäubli’s six-axis robots use the same CS9 controller, which makes it easier to deploy multiple robots in a digitally networked production environment.
The robots function as traditional industrial robots at high speed, or they can be coupled with safety equipment for what Stäubli refers to as MRC (man-robot collaboration) concepts. The new TX2 models have a digital safety encoder on each axis that communicates the position and movement of a robot’s arm and ensures that safety features like SafeSpeed and SafeStop (which control a robot’s actions when interacting with humans) are operating properly.
The new models can perform collaborative functions when combined with a third-party laser scanner that can sense when a worker is approaching the robot and slow its motion. The robot can also be programmed to come to a complete stop when a worker gets too close.
In addition, the new models are available with an optional “safe touch skin.” The skin senses human touch, so it stops the robot if it contacts a person.
“Our argument is that you don’t have to compromise between productivity and safety,” Schmitt said. “If you go with what is known as a standard lightweight cobot, they can’t go fast. They are compromised into having to go into a lower productivity — a lower speed. This is a different approach we are taking. We are saying you can go to the full speed if it is safe to do so. If nobody is around, then you run your production full speed. As people come to interact with the machine, the system will slow down or come to a full stop, if needed.”
Yaskawa goes big — and small
Yaskawa has launched several new robots and upgraded existing systems that are applicable to plastics processing.
Yaskawa’s six-axis GP4 robot, introduced in March, has an 8.8-pound payload for high-volume, small component processing. It has a 3.3-foot vertical reach, a 1.8-foot horizontal reach and repeatability of plus or minus 0.01mm.
“The GP4 is a very small new robot,” said Dean Elkins, segment leader for materials handling at Yaskawa Motoman. “It’s going to be applicable in the staging of inserts or perhaps in some post-process or pre-process applications.”
For example, it could be used for bin picking, sorting parts and loading inserts into another robot’s gripper for placement into a mold. It also could be used for assembling and trimming parts and small case packing, he said.
In February the company launched the extended reach six-axis GP280L robot, which offers fast and powerful performance for machine tending.
“It’s going to be used for injection molding extraction more than anything else,” Elkins said. “It’s going to be used on larger parts, perhaps parts that are being molded for the automotive industry or things that are very deep, like garbage cans, that require a longer reach to get to the center line of the mold inside the injection molding machine.”
The GP280L has a 617-pound payload capacity, a 10.2-foot horizontal reach, an 11.7-foot vertical reach and repeatability of plus or minus 0.1mm.
“When we look at a robot that has 3,100mm of reach, that allows us to set the robot back from larger injection molding machines at a distance where we can easily articulate in and out of the machine,” Elkins said.
The streamlined upper arm allows it to easily access parts in tight spots and a wide range of motion for the wrist eliminates potential interference with fixtures, the company said.
Yaskawa’s PL190 and PL320 palletizing robots, also launched in March, are suitable for moving boxes and filling pallets.
The PL190 has a 418.8-pound payload capacity and the PL320 has a 705.4-pound capacity. Each features a 10.4-foot horizontal reach, a 9.9-foot vertical reach and plus or minus 0.05mm repeatability.
A one-piece upper arm reduces mass and increases durability, while parallel-link construction for strength and heavy-duty bearings for smooth arm rotation support the handling of large, heavy payloads, the company said. The robots also can handle unbalanced loads, can be floor-mounted and include brakes on all axes.
The PL190 and PL320 are particularly suited to palletizing large quantities of blow molded bottles or containers, Elkins said.
“The palletizing arms allow you to pick up an entire row of product or actually an entire unitized layer at a time and place it onto a pallet,” he said.
Yaskawa also announced enhancements to its MotoSight 2D vision hardware and software system for robot guidance and inspection.
The system now uses new Cognex cameras — the MS8101, MS8401 or MS8402 — with high-speed PatMax technology for part and feature location, providing high accuracy and repeatability, according to the company.
“It’s a new evolution in the sense that we have moved to a new series of cameras for it, which is the 8000 series of Cognex cameras, which give you pattern matching, better resolution, and more flexibility in the machine vision process,” Elkins said.
The MotoSight 2D system is suited for general robot guidance, part identification, part inspection and high-speed picking.
Wittmann Battenfeld’s sales climb
Wittmann Battenfeld is setting sales records and enhancing its product line.
“Our robot and automation business in 2021 has just taken off,” said National Sales Manager Jason Long. “We are hearing more and more from our customers that they need to automate.”
The company set a monthly sales record in June, with more than 80 robots sold.
It also recently launched U.S. sales of its latest Primus robot and upgraded a couple of existing robot models.
The new Primus 48T is the largest in the line, which is designed for pick-and-place tasks. It has a telescoping arm, a payload capacity of 44 pounds and is designed to work with injection molding machines with clamping forces from 20 tons to 900 tons. The 48T has a Z stroke of 8.2 feet to 19.7 feet, an X stroke of 2.6 feet to 3.9 feet, and a Y stroke of 5.2 feet to 6.6 feet.
In addition, Wittmann Battenfeld updated its Sonic Ultra high-speed robots to be more streamlined and efficient. The company said the new design will help the molded part-removal robots “last longer and maintain themselves through the wear and tear created by their impressive speeds.”
“The Sonic robots are designed for applications down to 4-second cycles,” Long said. “The new design takes the great features from our Pro robots, such as wider bearing stance and axis profiles, to ensure even at faster speeds, the drives stay cool for less wear. These robots also now come standard with a complete auto lubrication system for all bearings and rack and pinion to make them a very low maintenance robot even at ultra-high speeds.”
The company also added features to its R9 robot control system, which is used on most of its robots, including an updated Quick New Wizard programming function and new ergonomic vertical touch screen pendants.
“The new Quick New Wizard requires very little training for the operator and can have a robot up and running in just a few short minutes,” Long said. “The flexibility now allows for more than just a simple pick-and-place program. The end user can set up more complex programs for things like degating parts or stacking parts by just answering a few simple questions.”
Other additions to the R9 robot control system include a digital twin to help users better simulate complex processes to more accurately predict their outcomes, the company said.
“The R9 new digital twin feature allows for a virtual display of real robot processes,” Long said. “The digital twin has the same attributes and characteristics as the real equipment, which enables simulation of the robot cycle. The digital twin can run on the R9 TeachBox and a PC. The programmer can run the cycle simulation before it is entered into the robot, allowing the user to catch possible errors at an early virtual stage.”
Other new features on the R9 controller include a “replay” troubleshooting feature, and the incorporation of new anti-collision features.
Hekuma responds to pandemic needs
The pandemic has spurred demand for pipette tips used in lab testing, and that has boosted the need for automated equipment to produce them, according to Hekuma.
“If you look at the demand and growth rates that happened in pipette tips, it’s astounding,” said Rick Shaffer, USA regional sales manager for Germany-based Hekuma. “In 2019, the total demand would have been something around 8 billion pipette tips. From ’19 to ’20, that increased to 11 billion, about a 40 percent increase due to an increase in testing. A lot of people were thinking, it’s a COVID blip, but the common wisdom is, it’s not a blip. It’s a step change. In 2021, it’s going to increase again to about 17 billion and then go up to about 22 billion [in 2022].”
In addition, there is a trend towards higher quality tips. Regulatory requirements are making filtered tips the majority of those produced almost overnight, Shaffer said.
Manufacturers of the injection molded tips also are dealing with a massive number of SKUs resulting from greater need for various tip sizes, material types and barriers, as well as different systems of packaging.
Many pipette tip manufacturers can easily justify systems with high-cavitation molds, but there are others who simply have too many different products and need a low-volume, high-mix solution.
To meet the changing demand, Hekuma now offers its HekuTip modular automation systems for pipette tips in three pre-configured models for different size production runs — the HekuTip 70, the HekuTip 350, and the HekuTip 700.
Typically, a HekuTip automated system consists of a high-speed take-out robot that reaches into a mold with end-of-arm tooling to remove the tips. The robot transfers the tips to a transfer gripper that orients them and places them onto a turntable. The tips then are transferred to a tray-loading station or optional visual inspection system that separates out any rejects. The pipette tips then go to a filter insertion and inspection station, if required, before they are packaged.
“The reality is that if you only scale back the productivity using the same components, the capital costs will be too high,” he said. “The key to an effective modular design is to ‘right size’ the components for the throughput and output and not to over-engineer the flexibility and functionality.”
All three systems can achieve an overall cycle time of 4.8 seconds, he said, which is significantly faster than a Hekuma system from about two years ago. At that time, cycle times were around 5.5 seconds.
The HekuTip 70 is the smallest automated system the company now sells and works with up to 16-cavity molds to process 70 million tips per year.
Hekuma offers optional vision inspection, filter assembly and packaging equipment that is tailored to the HekuTip 70’s output capacity, Shaffer said.
The HekuTip 350 can process about 350 million pieces per year, but it is capable of lower production volumes as well. It works with molds with up to 64 cavities.
The third in the series is the HekuTip 700, which can handle 700 million tips annually. It works with molds with up to 128 cavities.
New regulations have resulted in a surge of requests for an optional filter assembly and inspection station on all the HekuTip models, Shaffer said. Pre-COVID, approximately 65 percent of tips were made without filters. However, in 2022, filtered tips will be the majority of those produced, and by 2025 the trend points to 65 percent having filters, Shaffer said.
“Everything is 100 percent coupled in-line with no human interface,” Shaffer said. “There’s nothing here that needs an operator to do it, other than replenish the buffer [with] filters and make sure that buffers for the tip trays are there. It’s pretty much 100 percent automated — no touch.”
Bruce Geiselman, senior staff reporter
Contact:
Hekuma GmbH, Hallbergmoos, Germany, 49-811-999-77301, www.hekuma.com
Muller Technology Colorado Inc., Fort Collins, Colo., 970-229-9500, www.muller-technology.com
Stäubli Corp., Duncan, S.C., 864-486-5421, www.staubli.com
Wittmann Battenfeld Inc., Torrington, Conn., 860-496-9603, www.wittmann-group.com
Yaskawa America Inc., Motoman Robotics Division, Miamisburg, Ohio, 937-847-6200, www.motoman.com
More on automation innovations
Epson adds six-axis robots, parts feeders
Hekuma meets pandemic demand for automated equipment for pipette tips
Muller debuts cobot case packer, takeout robot, in-mold labeling system
Stäubli expands six-axis robot line with medium-payload models
Wittmann Battenfeld introduces Primus 48T, upgrades others
Bruce Geiselman | Senior Staff Reporter
Senior Staff Reporter Bruce Geiselman covers extrusion, blow molding, additive manufacturing, automation and end markets including automotive and packaging. He also writes features, including In Other Words and Problem Solved, for Plastics Machinery & Manufacturing, Plastics Recycling and The Journal of Blow Molding. He has extensive experience in daily and magazine journalism.
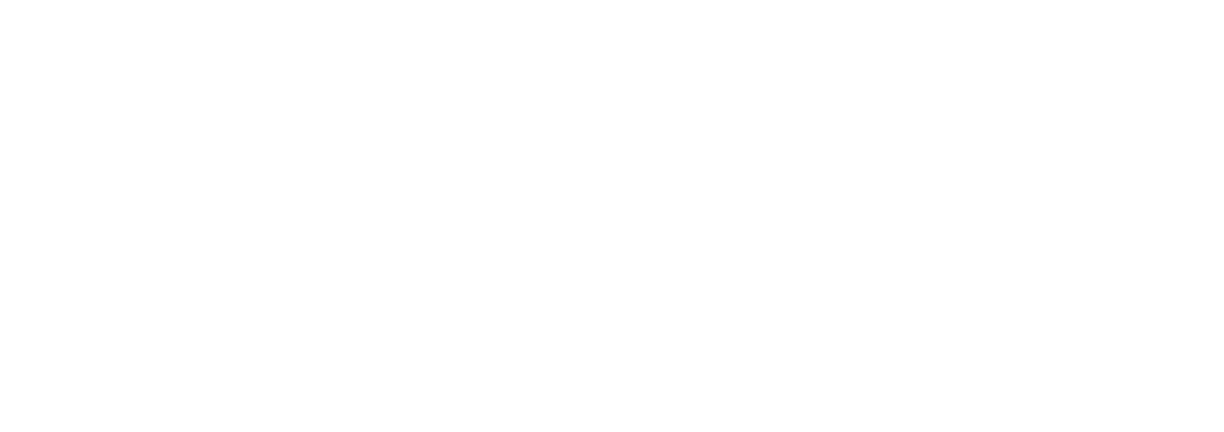