Stäubli expands six-axis robot line with medium-payload models
By Bruce Geiselman
Stäubli recently introduced three TX2 six-axis robot models, expanding the line to nine models.
TX2 robots are suitable for mold tending, part trimming, part assembly, ultrasonic welding and packaging tasks.
The models include the TX2-140 with a reach of 5 feet, and the TX2-160 with a reach of 5.6 feet. Each has a load capacity of 88 pounds. The new TX2-160L, a long-arm version of the TX2-160, has a reach of 7 feet with a load capacity of 55 pounds.
Stäubli specifies that all three feature repeatability of plus or minus 0.05mm, putting the robots on a par with the most accurate in the market. The accuracy is due, in part, to Stäubli developing and manufacturing its own gearbox.
“We’re the only manufacturer in the world that does its own gearbox,” said Sebastien Schmitt, robotics director, North America. “It’s allowing us to have that rigidity, precision and accuracy that we have, and speed.”
The new machines are compact, with all cables and hoses inside the robot housing.
The TX2-140 and TX2-160 are replacing the predecessor model RX160, which has resulted in an additional advantage — now all of Stäubli’s six-axis robots use the same CS9 controller, which makes it easier to deploy multiple robots in a digitally networked production environment.
The robots function as traditional industrial robots at high speed, or they can be coupled with safety equipment for what Stäubli refers to as MRC (man-robot collaboration) concepts. The new TX2 models have a digital safety encoder on each axis that communicates the position and movement of a robot’s arm and ensures that safety features like SafeSpeed and SafeStop (which control a robot’s actions when interacting with humans) are operating properly.
The new TX2 models can perform collaborative functions when combined with a third-party laser scanner that can sense when a worker is approaching the robot and slow its motion to protect the worker. The robot can also be programmed to come to a complete stop when a worker gets too close.
In addition, the new models are available with an optional “safe touch skin.” The skin senses human touch, so it stops the robot if a worker touches the robot or if the robot arm contacts a person.
“Our argument is that you don’t have to compromise between productivity and safety,” Schmitt said. “If you go with what is known as a standard lightweight cobot, they can’t go fast. They are compromised into having to go into a lower productivity — a lower speed. This is a different approach we are taking. We are saying you can go to the full speed if it is safe to do so. If nobody is around, then you run your production full speed. As people come to interact with the machine, the system will slow down or come to a full stop, if needed.”
The robots also come in clean-room versions.
Contact:
Stäubli Corp., Duncan, S.C., 864-486-5421, www.staubli.com
Bruce Geiselman
Senior Staff Reporter Bruce Geiselman covers extrusion, blow molding, additive manufacturing, automation and end markets including automotive and packaging. He also writes features, including In Other Words and Problem Solved, for Plastics Machinery & Manufacturing, Plastics Recycling and The Journal of Blow Molding. He has extensive experience in daily and magazine journalism.
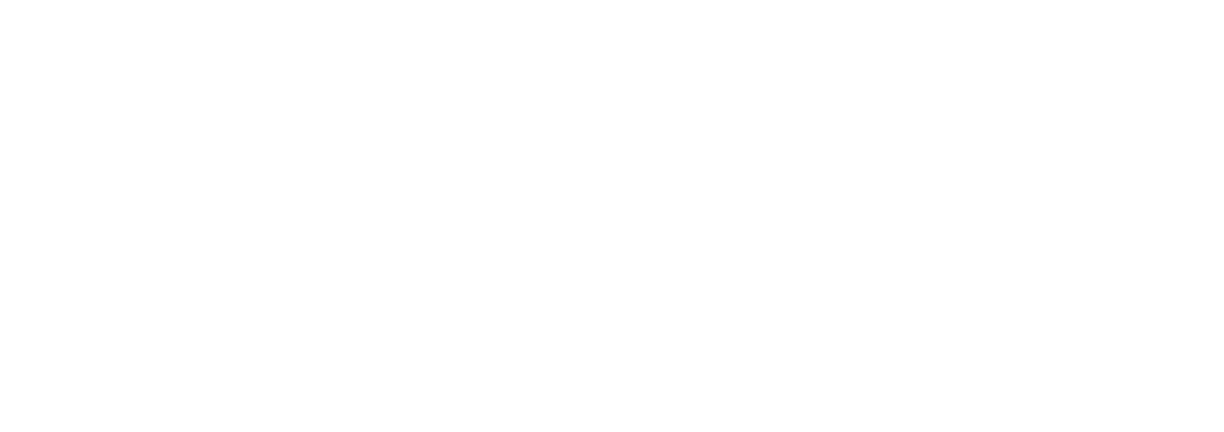