By Bruce Geiselman
ABB surveyed 1,650 large and small businesses in the U.S., Europe and China, and found that 84 percent of them said they will introduce or increase the use of robotics and automation during the next decade, while 85 percent said the pandemic had been “game-changing” for their business and industry.
They cited COVID-19 as a catalyst for accelerating investment in automation, according to ABB. Forty-three percent of the companies said they wanted robotics to improve workplace health and safety; 51 percent said it would enhance social distancing; and 36 percent thought robotics and automation would improve the quality of work for their employees.
ABB’s GoFa and Swifti cobots, unveiled in late February, offer higher payloads and faster speeds than have been available on previous ABB cobots. The new cobots are engineered to help businesses automate processes to assist workers with tasks such as material handling, machine tending, component assembly and packaging in manufacturing facilities and warehouses.
“With this expansion, we are making cobots easier to use and deploy, withThe GoFa and Swifti cobots are designed for easy installation and operation straight out of the box with no specialized training, according to the company. Users comfortable with operating a tablet or smartphone will be able to program and re-program the new cobots using ABB’s fast set-up tools.
Programming is done through the company’s Wizard easy programming software, typically on a teach pendant, which comes with the robot, said Alex Miller, an ABB Robotics spokesperson.
ABB’s new GoFa CRB 15000 six-axis collaborative robot has an 11-pound payload and a reach of 3.1 feet with speeds of up to 7.2 feet per second. ABB incorporated numerous safety features that allow it to operate alongside human workers without the space and expense associated with physical barriers.
The safety features include intelligent torque and position sensors in each of the cobot’s six joints thatThe GoFa’s payload is 9.9 pounds greater than ABB’s previous YuMi cobot, and the reach is 70 percent longer than YuMi’s single-arm robot. The longer reach allows loads to be picked up, moved and placed over greater distances, making it an effective solution for applications such as machine tending, material handling, packing, and packaging.
The YuMi line was introduced in 2015, and GoFa’s greater payload and reach will be a “gamechanger” by supporting a range of new tasks and applications, said Andie Zhang, global product manager for collaborative robotics at ABB Robotics.
ABB’s new Wizard easy programming software uses an interface based on graphical blocks that makes it easy for non-specialists to automate their applications. The blocks represent actions such as “move to location,” “pick up an object,” and “repeat task,” making it easy and intuitive for new users to build a series of simple processes for the robot to perform, the company said.
ABB’s new Swifti CRB 1100 cobot is faster than theThe Swifti cobot can operate at speeds of up to 16.4 feet per second with a payload of up to 8.8 pounds. It has what the company calls “best-in-class” accuracy and position repeatability of 10 microns, which the company said exceeds other cobots and industrial robots.
The Swifti offers faster operating speeds that are more typical of industrial robots. However, it has an integrated safety laser scanner with ABB’s SafeMove Collaborative safety software that can detect whenever a human approaches and slow down or stop to ensure worker safety, according to the company.
As the worker moves away, the cobot will restart, returning to full speed and movement for full productivity once it senses that its work zone is clear.
As an additional safeguard, the Swifti includes an interaction status light (green, yellow and red) that provides a visual indication of the cobot's status when a person is in its workspace.
“By enabling safe collaborative operation at higher speeds with its speed and separation monitoring, Swifti bridges the gap between collaborative and industrial robots,” Zhang said. “By utilizing the expanded capabilities offered by next-generation cobots like Swifti, companies will be able to transform their productivity by automating repetitive, mundane and dangerous processes, while leaving employees free to perform more rewarding activities.”
The Swifti is aimed at tasks like assembly and polishing where human operators need to perform functions such as supervising and repositioning parts. Such applications typically have required physical barriers like fences to ensure no contact occurs between workers and high-speed robots.
Universal Robots adds to portfolio of collaborative robots
In May, Universal Robots announced the release of an enhanced UR10e cobot with a 25 percent greater payload of 27.6 pounds.
“Our customers have already deployed UR cobots on a wide variety of palletizing applications,” President Kim Povlsen said. “Over time, they have identified opportunities to utilize our UR10e cobot in handling tasks with heavier items. In response to this demand, we have enhanced the UR10e to support greater payloads, providing customers with exciting new deployment capabilities.”
Now, using a 5.5-pound gripper, the“The extra payload just gives us a bigger range of products that we can handle,” said Joe Campbell, senior manager of strategic marketing and application development.
With the possibility of equipping the cobot with dual grippers, one gripper could handle mold extraction while the second could carry a mold insert, he said.
In addition to removing parts from molds, putting inserts into molds, palletizing and packing, UR10e robots are appropriate for secondary processes such as sprue cutting, degating, trimming and embossing, Campbell said.
Shifting repetitive tasks and the handling of heavy parts to cobots can play an important role in reducing workplace injuries, according to Universal.
“Humans are not designed to lift heavy goods repeatedly, but our cobots handle these tasks with ease,” Povlsen said. “By taking over unergonomic activities, UR cobots boost productivity, improve product quality and help businesses rethink how to best use the creative and problem-solving abilities of their workforce, all while keeping people safe.”
While the UR10e can handle heavier payloads, it retains its compact 7.5-inch diameter base. It has a 4.3-foot reach. The cobot’s price remains unchanged, the company said.
Bruce Geiselman, senior staff reporter
Contact information:
ABB Robotics, Auburn Hills, Mich., 248-391-9000, www.abb.com/robotics
Universal Robots USA Inc., Boston, 844-462-6268, www.universal-robots.com
More on automation innovations
Epson adds six-axis robots, parts feeders
Hekuma meets pandemic demand for automated equipment for pipette tips
Muller debuts cobot case packer, takeout robot, in-mold labeling system
Stäubli expands six-axis robot line with medium-payload models
Wittmann Battenfeld introduces Primus 48T, upgrades others
Yaskawa goes big and small with new robots, upgrades
Webinar
Bruce Geiselman
Senior Staff Reporter Bruce Geiselman covers extrusion, blow molding, additive manufacturing, automation and end markets including automotive and packaging. He also writes features, including In Other Words and Problem Solved, for Plastics Machinery & Manufacturing, Plastics Recycling and The Journal of Blow Molding. He has extensive experience in daily and magazine journalism.
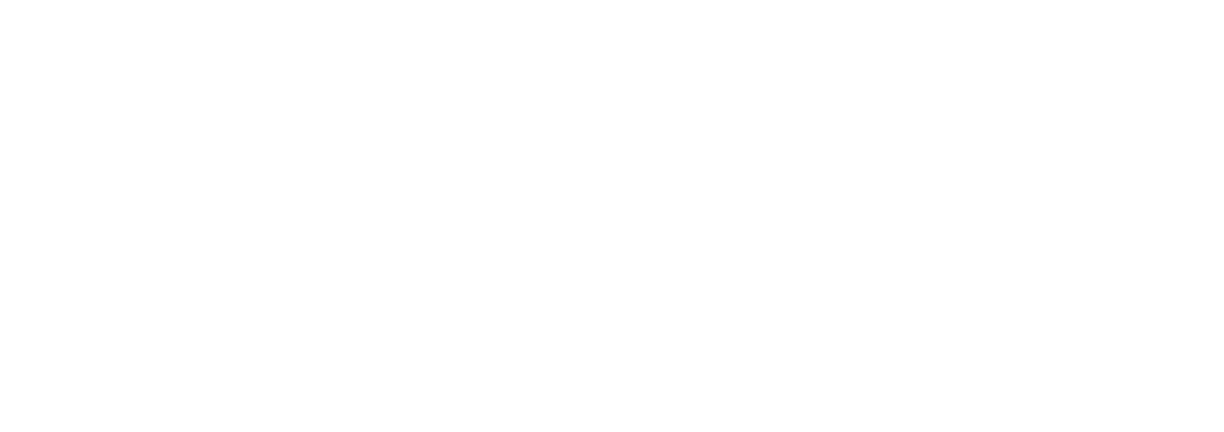