By Bruce Geiselman
Yaskawa has launched several new robots and upgraded existing systems that are applicable to injection molding, blow molding and other plastics processes.
Yaskawa’s six-axis GP4 robot, introduced in March, has an 8.8-pound payload for high-volume, small component processing. It has a 3.3-foot vertical reach, a 1.8-foot horizontal reach and repeatability of plus or minus 0.01mm.
“The GP4 is a very small new robot,” said Dean Elkins, segment leader for materials handling at Yaskawa Motoman. “It’s going to be applicable in the staging of inserts or perhaps in some post-process or pre-process applications.”
For example, it could be used for bin picking, sorting parts and loading inserts into another robot’s gripper for placement into a mold. It also could be used for assembling and trimming parts and small case packing, he said.
In February the company launched the extended reach six-axis GP280L robot, which offers fast and powerful performance for machine tending.
“It’s going to be used for injection molding extraction more than anything else,” Elkins said. “It’s going to be used on larger parts, perhaps parts that are being molded for the automotive industry or things that are very deep, like garbage cans, that require a longer reach to get to the center line of the mold inside the injection molding machine.”
The GP280L has a 617-pound payload capacity, a 10.2-foot horizontal reach, an 11.7-foot vertical reach and repeatability of plus or minus 0.1mm.
“When we look at a robot that has 3,100mm of reach, that allows us to set the robot back from larger injection molding machines at a distance where we can easily articulate in and out of the machine,” Elkins said.
The streamlined upper arm allows it to easily access parts in tight spots and a wide range of motion for the wrist eliminates potential interference with fixtures, the company said.
The GP280L also includes Yaskawa’s newest Euromap 67 interface, which makes interfacing with an injection molding machine much easier, Elkins said.
Yaskawa’s PL190 and PL320 palletizing robots, also launched in March, are suitable for moving boxes and filling pallets.
The PL190 has a 418.8-pound payload capacity and the PL320 has a 705.4-pound capacity. Each features a 10.4-foot horizontal reach, a 9.9-foot vertical reach and plus or minus 0.05mm repeatability.
A one-piece upper arm reduces mass and increases durability, while parallel-link construction for strength and heavy-duty bearings for smooth arm rotation support the handling of large, heavy payloads, the company said. The robots also can handle unbalanced loads, can be floor-mounted and include brakes on all axes.
The PL190 and PL320 are particularly suited to palletizing large quantities of blow molded bottles or containers, Elkins said.
“The palletizing arms allow you to pick up an entire row of product or actually an entire unitized layer at a time and place it onto a pallet,” he said.
In the spring, Yaskawa announced enhancements to its MotoSight 2D vision hardware and software system for robot guidance and inspection.
The system now uses new Cognex cameras — the MS8101, MS8401 or MS8402 — with high-speed PatMax technology for part and feature location, providing high accuracy and repeatability, according to the company.
“It’s a new evolution in the sense that we have moved to a new series of cameras for it, which is the 8000 series of Cognex cameras, which give you pattern matching, better resolution, and more flexibility in the machine vision process,” Elkins said.
The MotoSight 2D system is ideally suited for general robot guidance, part identification, part inspection and high-speed picking, the company said. Target applications include machine loading, pick-and-place transfers, assembly, packaging, palletizing, depalletizing and welding.
Yaskawa last year introduced the HC20XP, its largest collaborative robot.
“These collaborative robots are all the buzz right now,” Elkins said. “Everybody needs one. The nice thing about our robot is it boasts 1.7 meters [5.6 feet] of reach and a 20-kilogram [44-pound] payload. Not only can it be used for part extraction, mold insertion, degating or routering applications, it can also be used for collaborative palletizing applications in the plastics industry, which are becoming much more common.”
The robot also is the industry’s first IP67-rated cobot, the company said. It is equipped for continuous use in damp or splash-prone environments.
The HC20XP features a 5.6-foot maximum reach and can reach full pallets loaded 6.7 feet high without an elevator or lift mechanism. It can easily shift between collaborative speed in power- and force-limiting mode and full speed in industrial mode to optimize cycle times based on risk assessments and process requirements.
Contact
Yaskawa America Inc., Motoman Robotics Division, Miamisburg, Ohio, 937-847-6200, www.motoman.com
More on automation innovations
Epson adds six-axis robots, parts feeders
Hekuma meets pandemic demand for automated equipment for pipette tips
Muller debuts cobot case packer, takeout robot, in-mold labeling system
Stäubli expands six-axis robot line with medium-payload models
Wittmann Battenfeld introduces Primus 48T, upgrades others
Bruce Geiselman
Senior Staff Reporter Bruce Geiselman covers extrusion, blow molding, additive manufacturing, automation and end markets including automotive and packaging. He also writes features, including In Other Words and Problem Solved, for Plastics Machinery & Manufacturing, Plastics Recycling and The Journal of Blow Molding. He has extensive experience in daily and magazine journalism.
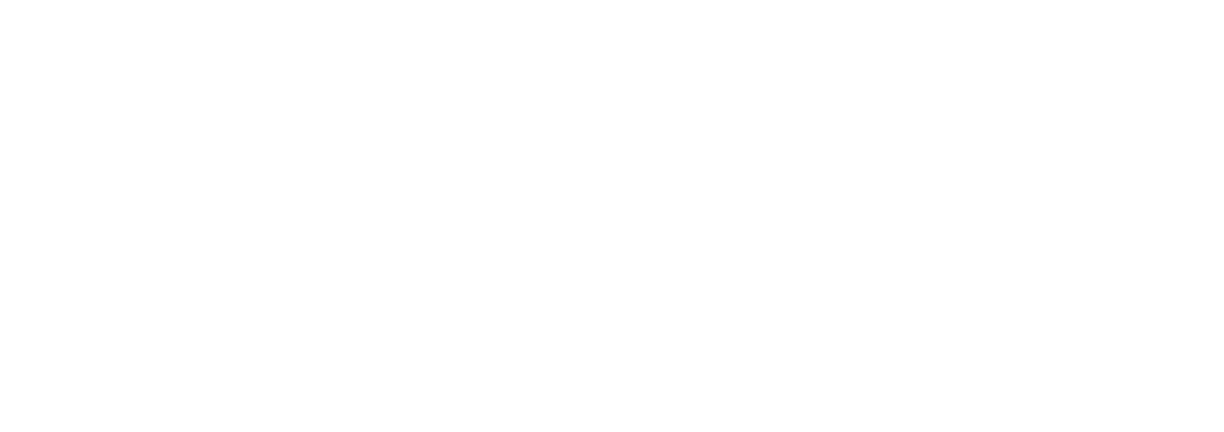