Hekuma meets pandemic demand for automated equipment for pipette tips
By Bruce Geiselman
The pandemic has spurred demand for pipette tips used in lab testing, and that has boosted the need for automated equipment to produce the tips, according to Hekuma, a manufacturer of modular automation systems.
“If you look at the demand and growth rates that happened in pipette tips, it’s astounding,” said Rick Shaffer, USA regional sales manager for Germany-based Hekuma. “In 2019, the total demand would have been something around 8 billion pipette tips. From ’19 to ’20, that increased to 11 billion, about a 40 percent increase due to an increase in testing. A lot of people were thinking, it’s a COVID blip, but the common wisdom is, it’s not a blip. It’s a step change. In 2021, it’s going to increase again to about 17 billion and then go up to about 22 billion [in 2022].”
In addition, there is a trend towards higher quality tips. Regulatory requirements are making filtered tips the majority of those produced almost overnight, Shaffer said.
In addition to increased demand overall, manufacturers of the injection molded tips are dealing with a massive number of SKUs resulting from greater need for various tip sizes, material types and barriers, as well as different systems of packaging.
Many pipette tip manufacturers can easily justify systems with high-cavitation molds, but there are many others who simply have too many SKUs and they need a low-volume, high-mix solution. The low volume, however, does not mean low quality or a compromise in the degree of automation, Shaffer said.
To meet the changing demand, Hekuma now offers its HekuTip modular automation systems for pipette tips in three pre-configured models for different size production runs — the HekuTip 70, the HekuTip 350, and the HekuTip 700.
Typically, a HekuTip automated system consists of a high-speed take-out robot that reaches into a mold with end-of-arm tooling to remove the tips. The robot transfers the tips to a transfer gripper that orients them and places them onto a turntable. The tips then are transferred to a tray-loading station or optional visual inspection system that separates out any rejects. The pipette tips then go to a filter insertion and inspection station, if required, before they are packaged or sent to a separate packaging line.
“The reality is that if you only scale back the productivity using the same components, the capital costs will be too high,” he said. “The key to an effective modular design is to ‘right size’ the components for the throughput and output and not to over-engineer the flexibility and functionality.”
All three systems can achieve an overall cycle time of 4.8 seconds, he said, which is significantly faster than a Hekuma system from about two years ago. At that time, cycle times were around 5.5 seconds.
The HekuTip 70 is the smallest automated system the company now offers and works with up to 16-cavity molds to process 70 million tips per year. The equipment is optimized for smaller machines and more moderate cycle times, the company said.
Hekuma offers optional vision inspection, filter assembly and packaging equipment that is tailored to the HekuTip 70’s output capacity, Shaffer said.
The HekuTip 350 is designed for higher output applications with fewer SKUs and can process about 350 million pieces per year, but it is capable of lower production volumes as well. It is designed to produce mid-range annual quantities using up to 64-cavity molds.
The third size in the series is the HekuTip 700, which offers the greatest productivity and can handle 700 million tips annually. It is designed to work with molds with up to 128 cavities.
New regulatory requirements have resulted in a surge of requests for an optional filter assembly and inspection station on all the HekuTip models, Shaffer said. Pre-COVID, approximately 65 percent of tips were made without filters. However, the projections for 2022 indicate that filtered tips will be the majority of those produced, and by 2025 the trend points to 65 percent having filters, Shaffer said.
“Everything is 100 percent coupled in-line with no human interface,” Shaffer said. “There’s nothing here that needs an operator to do it, other than replenish the buffer [with] filters and make sure that buffers for the tip trays are there. It’s pretty much 100 percent automated — no touch.”
Contact:
Hekuma GmbH, Hallbergmoos, Germany, 49-811-999-77301, www.hekuma.com
More on automation innovations
Epson adds six-axis robots, parts feeders
Muller debuts cobot case packer, takeout robot, in-mold labeling system
Stäubli expands six-axis robot line with medium-payload models
Wittmann Battenfeld introduces Primus 48T, upgrades others
Bruce Geiselman
Senior Staff Reporter Bruce Geiselman covers extrusion, blow molding, additive manufacturing, automation and end markets including automotive and packaging. He also writes features, including In Other Words and Problem Solved, for Plastics Machinery & Manufacturing, Plastics Recycling and The Journal of Blow Molding. He has extensive experience in daily and magazine journalism.
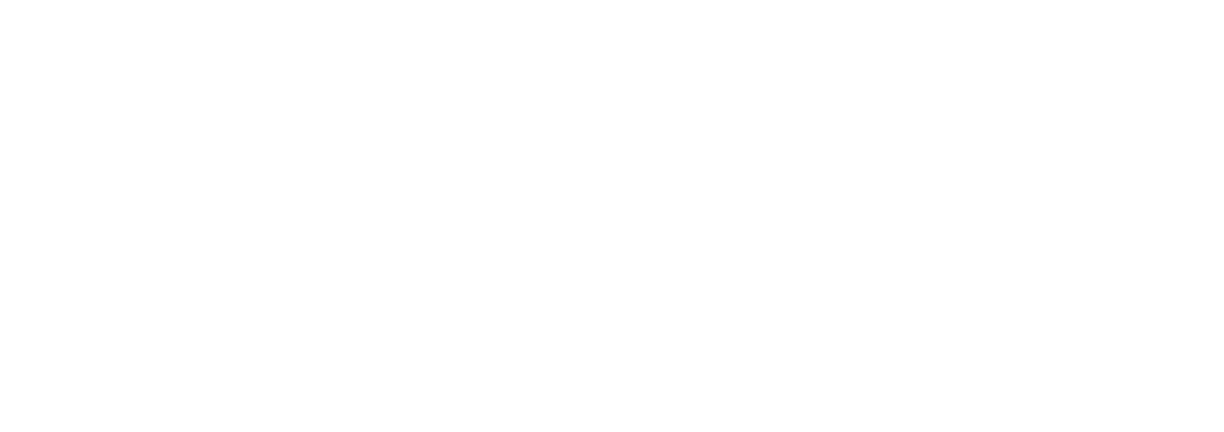