Muller debuts cobot case packer, take-out robot, in-mold labeling system
By Bruce Geiselman
Muller Technology, a supplier of molds and automation systems for thin-wall packaging, is offering what it calls the industry’s first self-contained collaborative robot case packer for the packaging of lids and containers.
The new automation system is centered around an Omron six-axis cobot and helps plastics processors bridge a labor shortage in the industry.
“The biggest thing that we’ve seen is the labor issues that were caused initially by COVID and now continue as the economy opens up, but people are not necessarily going back to work,” Taras Konowal, director of sales and marketing for North America, said. “A lot of our customers are having issues of not having enough labor, and the majority of what we’re seeing is in packing … Our customers have the molding machine. They have the mold. They have the resin, but they don’t have a person to pack the parts. So, they shut down complete cells due to the lack of labor.”
That is the single largest factor driving plastics processors to purchase new automated packing systems, Konowal said.
In addition, about 10,000 baby boomers are reaching retirement age every day, and the problem for plastics manufacturers is that millennials and Generation Xers are not interested in filling manufacturing jobs, according to the company.
Muller’s new cobot packer can work side-by-side with employees doing many basic tasks. When a person nears the cobot, it slows down but continues to work. The cobot does not require external guarding and all safety features are built in.
The cobot packer includes a Muller HMI that stores multiple recipes for a wide range of stack and box sizes. The case packer can be purchased separately or integrated into an automation line, including Muller’s new M-Line system for removing injection molded containers from their molds.
M-Line flexible take-out robot
Muller’s new M-Line take-out robot removes injection molded packages from their molds and places the containers on a conveyor belt for labeling or packaging.
The M-Line offers significantly greater versatility than most take-out robots for injection molded packaging, the company said.
The robot accommodates multiple mold types and from one to 48 mold cavities, unlike many robots that are restricted to certain mold types and cavitation levels. The M-Line’s low-cost end-of-arm tooling can be changed out quickly, allowing for changes in the number of mold cavities and types of packaging.
“It’s a unique design where it’s highly flexible,” Konowal said. “You can run any cavitation with that same take-out robot. It takes the parts out of the mold and it stacks them all with one arm, or two arms for a stack mold, or four arms for a four-face mold.”
The automation system is built on one frame and has a small footprint with no assembly required. The M-Line is motorized, with no pneumatics, which dramatically reduces the system’s consumption of energy and air.
The M-Line consists of three models for various sizes of injection molding machines. Seven units already have been sold in North America.
In-mold labeling automation system
Finally, Muller recently launched an in-mold labeling (IML) system for 5-gallon pails that reduces costs, improves productivity and enhances product appearance, the company said.
The one-piece IML system measures less than 8 feet wide as compared to competitive IML systems that are 12 to 14 feet wide, the company. It fits conveniently into existing production lines and works with any any injection molding machine height.
The IML system places a wraparound PP label into the mold, removes the pail after molding, and transports it to a visual inspection station. The pails are then directed to handle-assembly and stacking stations. The system can easily be converted from one-cavity to two-cavity, which allows for the production of one- to five-gallon pails.
More plastics processors are adopting IML systems due to labor shortages, Konowal said.
“Previously, they were using pressure sensitive labels or printing, and when you do either one of those, it’s a secondary function,” Konowal said. “So, you mold the pail; you put it in a warehouse or you put it through another secondary piece of equipment, and you have to have people do that. The IML is becoming much more cost effective. Label prices also have come down. But the [high quality of the] graphics that you get off of it, and one step and you’re done, have been big drivers in IML for the pail market.”
Five-gallon pails are used extensively for packaging home-improvement products, such as paint, and for restaurant products like mayonnaise and butter.
Manufacturers often face the high costs of scrapping finished pails due to label misalignment, but Muller’s IML system uses a digital label placement system that makes label placement more precise than standard, manually adjusted magazines, Muller said.
Muller’s new products were jointly developed by Muller Technology Colorado and its sister company, Switzerland-based Muller Technology Conthey. The machinery is being manufactured in Switzerland and Colorado.
Bruce Geiselman, senior staff reporter
Contact:
Muller Technology Colorado Inc., Fort Collins, Colo., 970-229-9500, www.muller-technology.com
Case packers in action
Six-Axis Automated Case Packer: https://www.youtube.com/watch?v=_Er_l1QRbso
Cobot Lid Case Packer: https://www.youtube.com/watch?v=RPaPL41DD-c
Cobot Container Case Packer: https://www.youtube.com/watch?v=fG9PtZthViE
Bruce Geiselman
Senior Staff Reporter Bruce Geiselman covers extrusion, blow molding, additive manufacturing, automation and end markets including automotive and packaging. He also writes features, including In Other Words and Problem Solved, for Plastics Machinery & Manufacturing, Plastics Recycling and The Journal of Blow Molding. He has extensive experience in daily and magazine journalism.
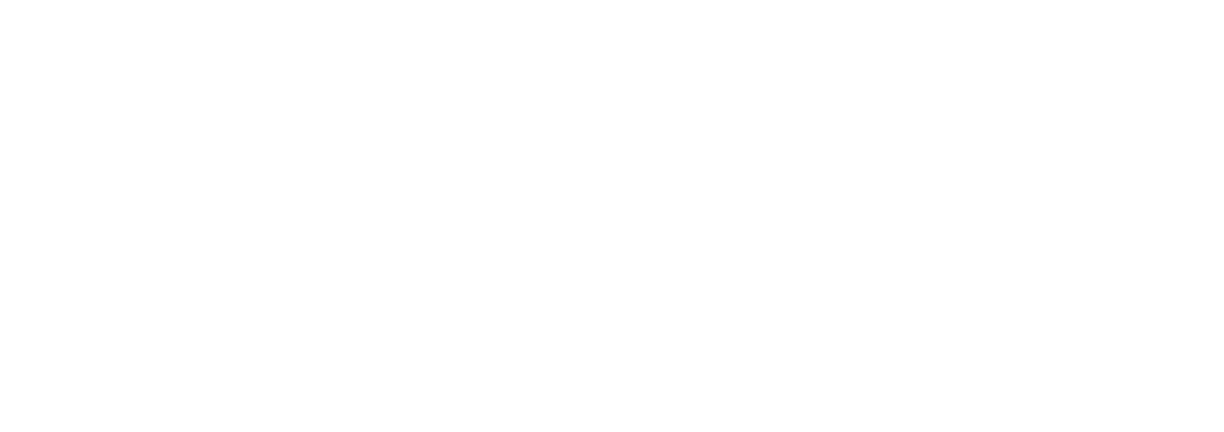