By Bruce Geiselman
Epson Robots has expanded its automation offerings for plastics processors.
The new C12XL robot is the company’s largest six-axis robot to date, with a reach of 4.6 feet and a payload of 26.5 pounds, said Scott Marsic, Epson’s group product manager for robotics.
“What is great about that robot is that like our other six-axis robots, our C12XL has a SlimLine design so it is able to get into smaller places with its dexterity,” Marsic said. “It works really well for load/unload, end-of-the-line handling, packaging, but it also has a long reach for injection molding machine tending — pulling plastic parts out of machines.”
The C12XL also is available in an ISO 4 standard clean room model and with optional electrostatic discharge protection for dust-free applications such as electronics and medical device assembly.
“We do a lot of work in the life sciences and medical device manufacturing space, and clean room [equipment] tends to be very important for that space,” Marsic said.
Epson also expanded its IntelliFlex line of parts feeders, which are used with the company’s robots to perform a variety of automated tasks. The company added two models, the IntelliFlex 80 and 380.
The 80 is the smallest in the line and can handle parts ranging in size from 3mm to 15mm. The 380 fits between the existing 240 and 530 models and can handle parts from 15mm to 60mm.
“This is our intelligent parts feeding system,” Marsic said.
Manufactured parts can be fed into a vibrating tray that spreads out the parts, an integrated vision system identifies them, and an integrated robot arm (SCARA or six-axis) can pick up the identified parts for placement, assembly or whatever is needed, Marsic said.
“It uses AI,” Marsic said. “It can sort and figure out which part to grab. It’s a very intelligent system and is fully integrated with our robots so it makes it really easy to use.”
One use for processors is assembling injection molded parts into a finished product or component.
“What happens typically is that all these parts get manufactured from injection molding machines, get put into a bag, and they get handed to someone who has to do something with all these parts,” Marsic said.
The Intelliflex Feeding System can automate that process, he said. It also could be used for simple pick-and-place tasks.
Epson also introduced the clean room version of its VT6L all-in-one six-axis robot, which offers a built-in controller and SlimLine design at a starting cost of $13,900.
The VT6L is ideal for simple pick-and-place applications, and, because it is able to handle two parts at a time, it can quickly assemble and disassemble parts.
“What we did in this past year is we launched a clean room version, which is really important for plastics, in particular life sciences and medical device manufacturing,” Marsic said. “These are fast. These are industrial robots. Collaborative robots, to be safe, have got to slow down, and you’re not getting the throughput you need. If you think about plastics manufacturing with small parts and putting things together, you need to be moving quickly These robots fit right into that.”
Contact
Epson Robots, Carson, Calif., 562-290-5910, www.epsonrobots.com
More on automation innovations
Epson adds six-axis robots, parts feeders
Hekuma meets pandemic demand for automated equipment for pipette tips
Muller debuts cobot case packer, takeout robot, in-mold labeling system
Stäubli expands six-axis robot line with medium-payload models
Wittmann Battenfeld introduces Primus 48T, upgrades others
Bruce Geiselman
Senior Staff Reporter Bruce Geiselman covers extrusion, blow molding, additive manufacturing, automation and end markets including automotive and packaging. He also writes features, including In Other Words and Problem Solved, for Plastics Machinery & Manufacturing, Plastics Recycling and The Journal of Blow Molding. He has extensive experience in daily and magazine journalism.
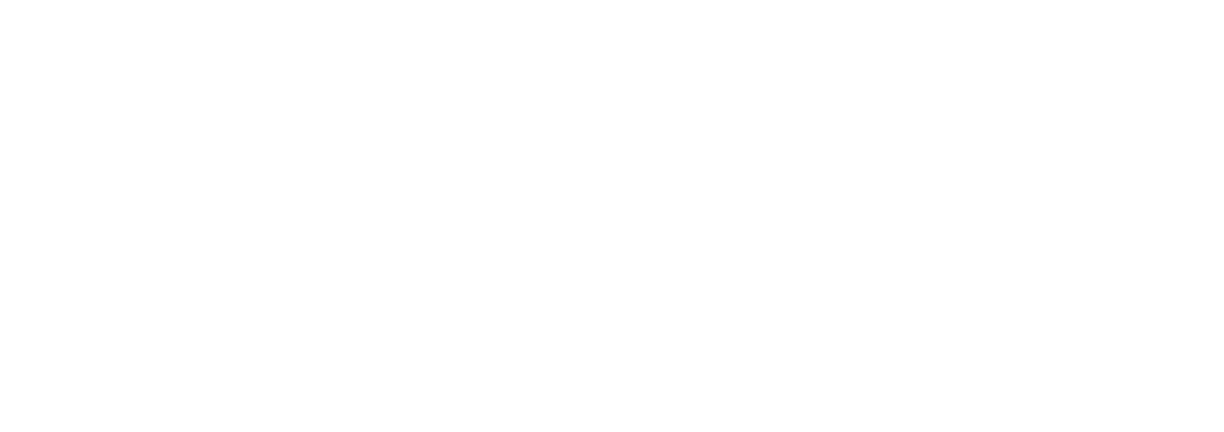