By Ron Shinn
North American subsidiaries of foreign machinery manufacturers generally say they pursue the best available markets for the machines they have to offer, but localization of a global strategy is not good enough for KraussMaffei Corp.
“We have a lot of activity going on in Europe, but we are also addressing the market needs here in North America with some strategies that are unique to this region,” said Nolan Strall, president of the U.S. operations, based in Florence, Ky.
Strall, who became president of the U.S. operations in January 2022, also serves as VP of sales. “We really believe [in my combined responsibilities] from a management perspective because we want to keep our ear to the market and be very regionally focused in terms of what the market needs us to develop,” he said. “It is important for our leadership team to stay very dialed in and close to what the customers are saying and where we see technology going.”
KraussMaffei worldwide sold about $1.09 billion worth of machinery in 2022. Injection molding presses accounted for about 60 percent of that; extrusion machinery, 30 percent; and RPM, 10 percent.
In North America, where sales totaled about $230 million in machinery and $90 million in after-market services, the machinery mix is different – 40 percent injection, 40 percent extrusion and 20 percent RPM.
KraussMaffei is 185 years old but is undergoing significant change:
- In 2016, China National Chemical Corp. Ltd. (ChemChina), one of the largest chemical companies in China, acquired majority ownership, and the company now is listed on the Shanghai Stock Exchange.
- Production of extrusion and recycling equipment was consolidated in a new 1.045-million-square-foot plant in Laatzen, Germany, at the end of 2022.
- The company headquarters and manufacturing for injection molding, RPM, additive manufacturing, mechanical production and automation machinery moved into a state-of-the-art, 2.2-million-square-foot plant in Parsdorf, Germany, this summer.
While it doesn’t build injection molding machines, the Florence plant handles retrofits, automation upgrades and other modifications. For single- and twin-screw extruders 133mm and smaller, it adds upstream and downstream equipment and power panels, and completes assembly. Pumps and mixing heads for RPM come from Germany, and the Florence plant handles assembly and adds downstream equipment.
KraussMaffei has 238 employees in the U.S.
Injection molding machinery sales for manufacturers worldwide is flat, generally reflecting the overall economy. But RPM offers an opportunity for growth, Strall said.
“Our advanced technologies — where we combine our injection molding with our reaction processing offerings or extrusion offerings with injection molding — is where we see opportunities,” he said.
The best examples are in the electric vehicle industry, aerospace, other commercial applications and anywhere light weighting is needed.
One example — a direct-compounding injection (DCIM) molding setup — will be on display at the NPE 2024 show, he said. “Our DCIM technology, which is a single-screw extruder that is extruding directly into the injection cylinder, will be on display.”
“We can combine carbon fiber, we can combine glass fiber, we can do lightweight,” Strall said. “We’ve got a lot of different opportunities for material cost and weight savings for the customer.”
Machinery in the Innovation Center can produce 4-inch profiles and pipe up to 4 inches in diameter.
Edward Gay, process technology manager in the extrusion division, directs the Innovation Center. He works with in-house technicians and customers to expand the projects KraussMaffei machinery can accomplish, and he conducts customer trials.
“This is our chance to put our best foot forward,” Gay said. “We have a complement of extruders and a wide range of auxiliary equipment so we can run trials with the same equipment the customer uses.”
But some of the most promising research and product development takes place elsewhere. This is where Strall’s efforts to develop new markets are best seen.
During the past two years, KraussMaffei has partnered with the Clemson University Composites Center in Greenville, S.C., and the National Institute of Aviation Research (NIAR) and its Advanced Technologies Lab for Aerospace Systems (ATLAS) at Wichita State University in Kansas.
“Both of those locations have extremely complex technical solutions, primarily wrapped around injection molding, RPM, high-pressure RPM and polyurethane molding,” Strall said.
The Clemson facility worked with KraussMaffei and the SC Fraunhofer USA Alliance to develop a process to build composite bicycle frames that will be used by Time Bicycles at a new plant in Spartanburg, S.C. The process the European manufacturer of high-end bicycles and e-bikes will use was developed on a 1,000-ton vertical KraussMaffei press with integrated RPM, injection molding and heating systems. The new procedure replaces a manual RPM process Time Bicycles uses in Europe with a more efficient automated process.
“Some of these technologies, customers in the U.S. didn’t even know we even had in our portfolio.” Strall said. “It is pretty exciting for us.”
In its partnership with NIAR, KraussMaffei is focusing on aerospace applications. KraussMaffei has installed a dual-injection SpinForm machine with a FiberForm system. The system adapts a KraussMaffei automotive system to make production aerospace parts in higher volumes than is currently possible.
An expert has relocated from KraussMaffei in Germany to Wichita to work with NIAR and the ATLAS laboratory.
The KraussMaffei injection molding machines sold in North America are built in Germany and shipped here for installation and commissioning, Strall said. “The mission we set out on a year ago is to add more value to those machines here locally with the infrastructure we have, the people we have, the service we have, the engineering we have so that we can maximize local solutions for our customers.”
One solution is automation, he said.
Mike Gunner, VP for automation, said his team can step in to help processors manage their automation programs.
“The idea is that we are fully integrated into KraussMaffei,” Gunner said. “I am really listening to where our customers want to go with the technology, what they want to do and to help guide them a little bit. Basically, I want to be able to highly customize the automation.”
He said that is the value proposition KraussMaffei aims for.
“Investment in automation continues to be very strong,” Gunner said. “The way that we are approaching this is by creating partnerships with our customers, work out where they are and look for synergies.
“I’m very lucky," Gunner said. "I’m attached to a large organization, and we can bring extra value to our customers without adding significant infrastructure or personnel. We are just adding capability so we can take on the smaller projects.”
Gunner said automation can help a processor take operations to the next level.
Gunner has overall responsibility for KraussMaffei's plant in Brighton, Mich., which serves as an incubator for automation initiatives and produces tooling and various panels.
Strall said his approach is to automate the processes. “We are a plastics company, and we are an OEM,” he said. “But we are open to helping our customers in other areas in the plant that are outside of the injection molding room. That’s something we’re doing a little differently here in North America.”
KraussMaffei also is seeing growth in the recycling market.
“We’ve got some really exciting projects with chemical-based recycling and see a lot of opportunity going forward,” Strall said. The new PureCycle recycling plant in Ironton, Ohio, uses KraussMaffei Blue Power twin-screw extruders and KE single-screw extruders.
“We have a lot of different projects in the U.S. and Canada that we are working on,” Strall said. Some of those projects are related to compounding machines.
“We also see some new opportunities using natural fibers and composites extruded into pellets that will then be used in the injection molded electric vehicle market.”
Money from the federal Inflation Reduction Act is changing the market as automobile manufacturers shift to electric vehicles. “We are uniquely positioned to address that need in the U.S. with the people, service, automation, technology and the applications to do that,” Strall said.
KraussMaffei introduced its first additive manufacturing machines with much fanfare at the K Show last October, and they will be available in the U.S. at the end of this year. The company has already started phasing in the launch in Europe. Is Strall worried about the head start other additive machine manufacturers have had?
“We make RTM [resin transfer] molding equipment through our RPM product portfolio,” Strall said. “Why couldn’t we use our additive manufacturing machine to demonstrate tooling or prototype tooling for our customers? It comes to the point where you can buy our machine for additive that may support your other equipment in terms of rapid prototyping or tooling or whatever the case may be.”
Strall said KraussMaffei thinks artificial intelligence (AI) has a role in the plastics industry and the company is looking at use cases where an engineer or technician can ask a question and get an answer without consulting a manual. “I don’t think it is a silver bullet, but it certainly has a place in manufacturing.”
The company has continued to invest in customer-care managers, stationed around the country to work with customers who need repair or other on-site support. It has 66 customer-care reps, up from 49 two years ago. The goal is to get to 77, according to John Fini, VP of digital solutions and service.
Fini said KraussMaffei has developed a reliability program for hydraulic oil, machine lubrication and analysis, and repair programs for high-value items such as cylinders, pumps, motors and valves.
How does the near term look for KraussMaffei?
“Globally, we are seeing the same type of recession activity that everyone else is seeing,” Strall said. “But we have a strategy and vision, along with an incredible team in the U.S., which will allow us to navigate the situation successfully.”
Ron Shinn, editor
Contact:
KraussMaffei Corp., Florence, Ky., 859-283-0200, www.kraussmaffei.com
Ron Shinn | Editor
Editor Ron Shinn is a co-founder of Plastics Machinery & Manufacturing and has been covering the plastics industry for more than 35 years. He leads the editorial team, directs coverage and sets the editorial calendar. He also writes features, including the Talking Points column and On the Factory Floor, and covers recycling and sustainability for PMM and Plastics Recycling.
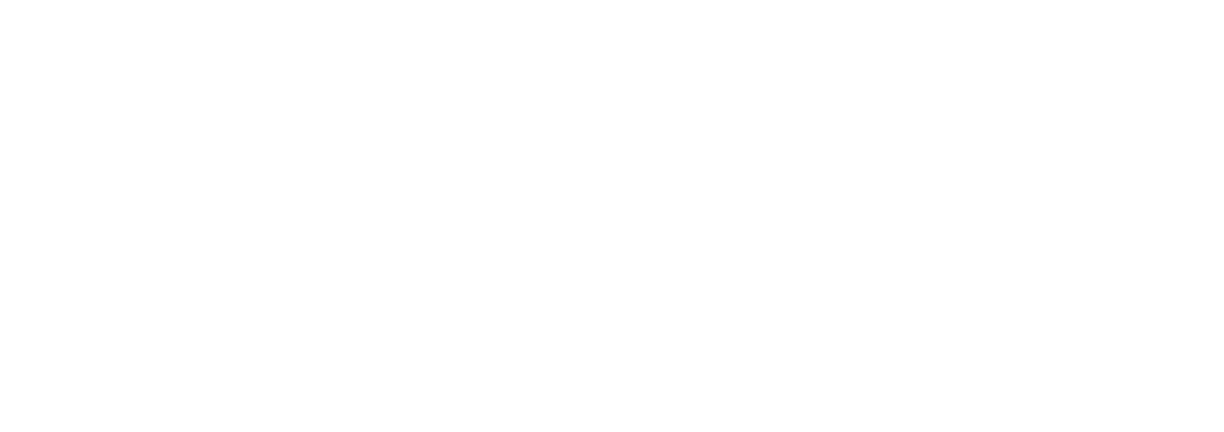