By Ron Shinn
KraussMaffei Technologies GmbH unveiled a pair of industrial 3D printers at K2022, a liquid-resin-based stereolithography system for smaller, precision parts, and an extruder-based system for large parts.
The Munich-based company first hinted about entering the additive manufacturing equipment market in June. At K2022 in Düsseldorf, it staged a splashy show with loud music and smoke when the curtain dropped. The unveiling drew a large crowd.
Michael Ruf, KraussMaffei CEO, said the company has focused on more than just the technology of the 3D printing machine. KraussMaffei will offer training and consulting, printing services and material selection as well.
The goal is to help customers make a part right the first time and at the lowest possible manufacturing cost, he said.
“For us, this is about taking our capacity for productivity, quality and efficiency in industrial plastics processing and applying it to additive manufacturing solutions,” Ruf said.
He predicted a big market for 3D printing. “Many of the applications for additive manufacturing are not even known today,” Ruf said.
Digital manufacturing today resembles start-ups in the digital world, Ruf said. “Companies come up with product ideas that they think are crazy ideas, but now it is possible to produce these crazy ideas.
“How big is the market? I can’t tell you,” he said. “Is the market there? Yes, definitely.”
The company described the liquid-resin-based laser 3D printer, called precisionPrint, as an end-to-end additive manufacturing processing system based on the stereolithography (SL) process. KraussMaffei said its proprietary, high-speed laser system offers high surface quality and accuracy.
It can print different resins depending on the part requirement. The company said it is cost effective for small lot runs up to mass customization.
Maximum part size is 9.84 inches long by 9.84 inches wide by 15.7 inches high.
“There is no other machine out there that has the industrialization, the automation that we have,” Ruf said.
The second printer, called powerPrint, uses a proven extruder design for the best reliability and process stability, according to Michael Helneder, KraussMaffei’s manager of customer success for additive manufacturing.
Resin, including fiber-reinforced material, is processed in a heated chamber to also improve reliability.
The unit can build large and complex parts about 6.6 feet long by 8.2 feet wide by 6.6 feet high.
Ruf said both printers are designed to run 24/7 in either small-scale or large-scale operations.
The machines will undergo beta testing next year and be sold first in Europe and the U.S., then rolled out to the rest of the world. He predicted the new printers will be embraced by the medical technology, construction and foundry industries.
Arburg was the first legacy injection molding manufacturer to market 3D printers. It launched the Freeformer line in 2013 and continues to add new models. Like the powerPrint, the Freeformer uses standard resin pellets.
Contact:
KraussMaffei Corp., Florence, Ky., 859-283-0200, www.kraussmaffei.com
Ron Shinn, editor
Ron Shinn | Editor
Editor Ron Shinn is a co-founder of Plastics Machinery & Manufacturing and has been covering the plastics industry for more than 35 years. He leads the editorial team, directs coverage and sets the editorial calendar. He also writes features, including the Talking Points column and On the Factory Floor, and covers recycling and sustainability for PMM and Plastics Recycling.
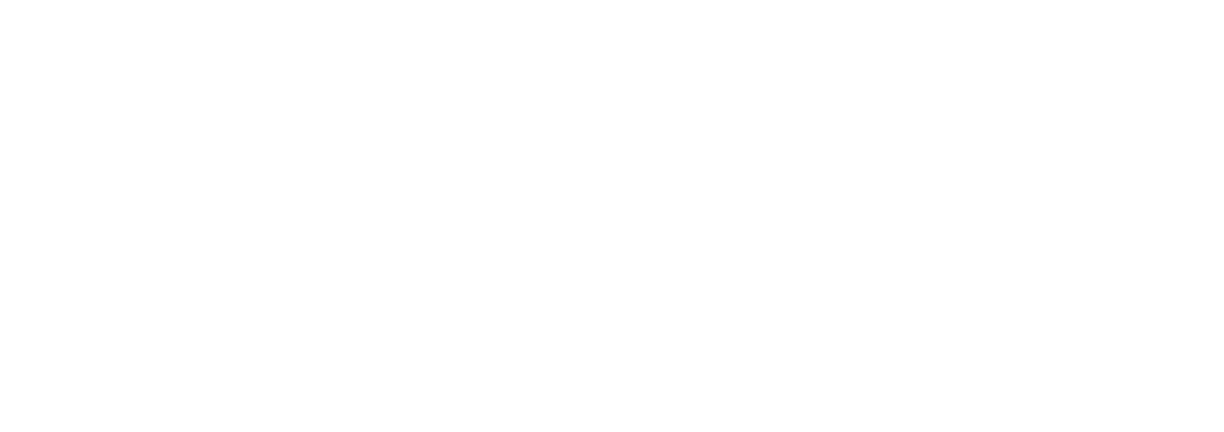