Talking Points: EVs spell big market shift for auto parts processors
I used to think the shift from internal combustion engine (ICE) to electric-powered vehicles would be a gradual adaptation for the plastics industry. It would be a normal business progression where the plastic parts on today’s cars would morph into the plastic parts on tomorrow’s cars.
I might have been wrong.
There is nothing gradual about the transformation, and the changes taking place involve more than just vehicles’ power sources. There is the simultaneous adoption of autonomous driving systems that rely on radar and lidar, new demands for sensors molded into all sides of the vehicles and lighting systems replacing front grills. High-temperature battery systems and exterior panel designs to make vehicles more aerodynamically efficient also are needed.
“We are in a seismic shift,” Dhanendra Nagwanshi, EV batteries and electricals leader at Sabic, a global chemical company, told a recent automotive conference in Novi, Mich., sponsored by Engel.
Kevin Riddell, senior manager of powertrain forecasts at LMC Automotive, said about 60 brands already are producing electric vehicles (EVs) in the U.S. market, but that number is projected to increase to about 300 brands by 2030. LMC, a forecasting firm, predicts battery electric vehicles will amount to about 10 percent of new vehicle sales this year and 25 percent by 2030.
Related: Ford firms up key suppliers to produce 2 million EVs by 2026
Some speakers urged suppliers to embrace an all-electric philosophy because auto manufacturers are coming to realize that producing both ICE and EVs is not sustainable.
Another speaker said the global auto market has reached a tipping point and that big investment dollars are going into sustainable vehicles. “I see it from the investor side,” said Hinrich Woebcken, now a partner with Blue Lagoon Capital and senior adviser to Apollo Global Management. He is the former CEO of Volkswagen Group of America and started his business career with injection molding machinery maker KraussMaffei Group.
“The big investments are really more and more being channeled into companies where the management and the technology stands behind sustainability,” he said. That means opportunities for the plastics industry as automakers produce more sustainable vehicles.
Woebcken said he is stunned by how fast EV companies are bringing new products to market. He said these new automakers work more closely with suppliers than legacy manufacturers. He urged plastics parts suppliers to work with these innovative new companies despite seemingly small production volumes early on.
Related: PMM looks at the future of plastics in automotive parts
Tier 1 automotive supplier Magna International Inc. recently told a Canadian automotive magazine that 70 percent of its research and development projects are now geared toward EVs or hybrid vehicles. Only 15 percent of current production goes into EVs. Magna, North America’s largest automotive supplier, said it expects 30 percent to 40 percent of its business to come from EVs or hybrids by 2030.
Magna, based near Toronto, said it expects growth in its divisions that make exterior body panels, lighting and electronics as EV demand picks up.
Engel partnered with Sabic to include an in-person tour of its nearby Automotive Development Center. The materials supplier showed EV parts already being made with Sabic plastic materials as well as some in development. An example is a battery enclosure that withstands heat, flame and impact better than the aluminum covers that are most commonly being used.
It also demonstrated two-shot composite structural parts including a front-end module, lift gate and truck toolbox.
What does this mean for plastics processors? The automotive market is the biggest driver of the plastics industry, and a significant number of processors like to say they are a Tier 1, Tier 2 or an automotive supplier.
There is no doubt we are at the beginning of monumental change in automotive-related processing and big players such as Magna, which have the ability to invest in research and development right now, are going to grow.
But Tier 2 suppliers and others do not need to be left behind. I recently visited a mid-sized Tier 2 processor that is working closely with an auto manufacturer and materials supplier on an EV drive-train part. That same processor knows it is going to lose some of its traditional, under-the-hood parts business as ICE vehicle sales decline.
Very early automobiles were mostly horse-drawn carriage bodies with horses replaced by an ICE. Today’s hybrids and EVs are ICE vehicles with a newer, more sustainable power source.
New design is starting to evolve. Lucid Air, which won the prestigious MotorTrend Car of the Year for 2022, focuses on aerodynamics, rolling resistance and powertrain efficiencies to push the technology forward. “The Lucid Air is a new breed of super-efficient EVs,” said Eric Bach, senior VP of product and chief engineer at Lucid Motors.
Processors need to pay attention to these new opportunities. It will be too easy to be left behind.
Ron Shinn, editor
Ron Shinn | Editor
Editor Ron Shinn is a co-founder of Plastics Machinery & Manufacturing and has been covering the plastics industry for more than 35 years. He leads the editorial team, directs coverage and sets the editorial calendar. He also writes features, including the Talking Points column and On the Factory Floor, and covers recycling and sustainability for PMM and Plastics Recycling.
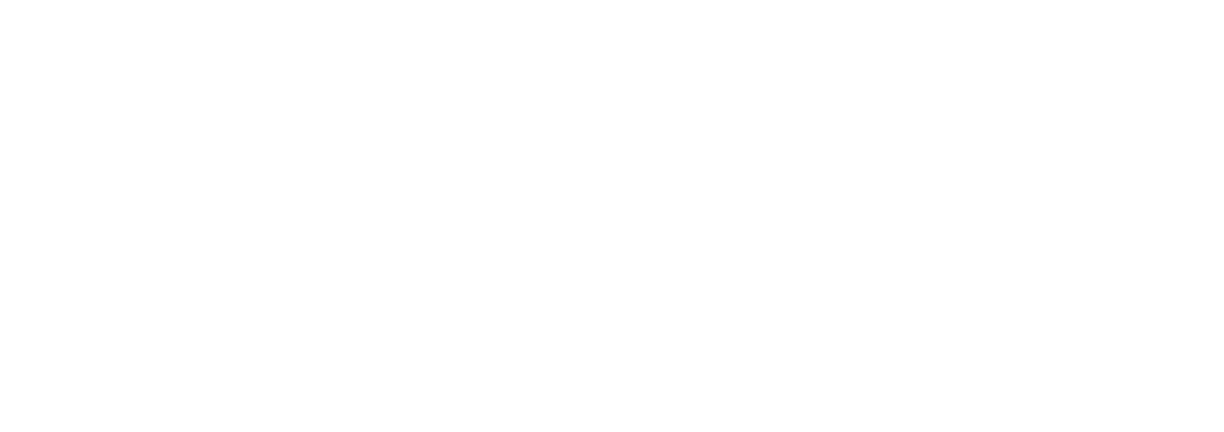