Hot runners inject new options for molders making tough automotive parts
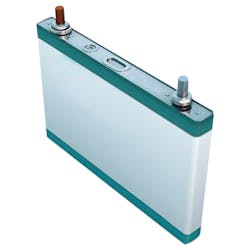
By Karen Hanna
The evolution of electric vehicles (EV), the demand for further lightweighting and the development of new resins, are creating continued interest in hot runners among molders of automotive parts, said representatives of Husky and Mold-Masters.
“We’ve seen this trend of lightweighting for quite a few years now, but then, when you fuel it with the push for more electric vehicles and the impact that weight has on essentially electric vehicle efficiency, it’s forcing companies to think about using plastic differently, think about using different types of resin,” said Michael Ellis, global business manager for Husky.
As EV technology gains traction, Ellis predicted more manufacturers will look to cut vehicle weight, to extend the range of the battery. New resins will be able to function in roles once filled by metals, reducing vehicle weight. And, with cars increasingly becoming mobile entertainment centers, consumers will look for interior finishes and features that allow them to ride in style.
The development of EVs is one factor pushing innovation, said Jordan Freise, product marketing manager for Mold-Masters.
“It’s a new segment of the vehicle versus traditional interior, exterior and under-hood parts, that pushes hot-runner companies to be more creative on our designs, material selections, coatings and applications engineering,” he said.
As an example of how molders can benefit from using his company’s innovations, Friese cited the problems one manufacturer had in making a cover for lithium-ion batteries. The molder used a very expensive engineered resin for the product. But the hot runner initially used in the application ran for only a short time before requiring extensive maintenance.
“The major issue with this resin is that during the heating process, the material releases a gas that is corrosive to steel. Both hot-runner system and injection molding machine are affected by this gas,” Friese said. “Once the corrosion starts, it spreads rapidly and leads to valve-pin seizure, potential leakage and defects in the part itself.”
To lower scrap and production rates, the molder turned to Mold-Masters.
“By utilizing Mold-Masters’ Summit-series hot-runner system, which incorporates a range of special materials and coatings, uptime was increased by at least 400 percent, compared to the competition,” Friese said.
The Summit hot runners incorporate special materials and coatings, allowing them to withstand corrosion, Friese explained.
“We’re definitely interested in the push and where the technology is going. The shift from internal combustion to EV is obviously an area of interest for us because we do believe that it will increase the plastic on the vehicle, specifically in the power train, you know, battery casing, cable connections, fluid delivery, things of that nature,” Kidd said.
Battery components can feature complex geometries and difficult-to-mold materials, said Vern Moss, Husky's business manager for controllers.
He and his colleagues noted that hot runners provide direct gating, which pushes the molten plastic directly into the cavity to make the part, sparing it from degradation and eliminating the use of wasteful runners that then must be removed.
“Some of those materials that they’re molding those parts out of are pretty challenging, and the geometries of those materials are very challenging,” Moss said.
In some cases, Ellis said automotive parts manufacturers could benefit from using Husky’s UltraShot, a new concept of melt-delivery system devised to combine injection and hot-runner capabilities for even more precise injection of sensitive resins.
Continued demand for lightweighting also presents opportunities for hot-runner OEMs. One strategy is co-injection, sandwiching materials with high-quality surfaces around less-dense materials.
Another option takes advantage of advances in materials; molders now have the freedom to create functional plastic parts that can be exposed to extreme conditions, such as ultra-high temperatures.
“As the hot-runner supplier, we have to be consultants and solutions providers to our customers as the evolution of vehicles continues and the proliferation of engineered resins with additives becomes more prevalent,” Friese said. “Bio-resins are starting to gain ground as the industry is focused more and more on the environment.”
New and demanding materials also play a role in vehicles’ appearance. Lenses, for instance, must look good to perform; they cannot work without the absolute clarity of the materials used to make them, Friese said.
When it comes to lenses and console features, the materials are tricky, and expectations are high.
“Technology advancements, for example through the use of various screens on the dash, offer a simple and elegant appearance but this could have an impact on small component tooling,” Friese said.
As driverless vehicles shoulder their way into the market, the demand for luxe comfort could increase, Kidd said, the car becoming “an extension of your home, essentially, because we’re not going to be driving.”
Whether it’s a push to punch up a vehicle’s looks, reduce its weight or improve its range, hot runners could play an increasing role.
“We’re able to do and basically manage certain resins differently than you could, let’s say with cold runners, but also when you talk about gaining efficiency and your ability to gain different areas apart, when you start to convert parts and make them differently and use different resins, that ability to be able to gate them effectively and efficiently using hot runners, it’s really nicely aligned with this push to use more plastic in vehicles,” Ellis said.
Contact:
Husky Injection Molding Systems Ltd., Bolton, Ontario, 905-951-5000, www.husky.co
Mold-Masters, Georgetown, Ontario, 905-877-0185, www.moldmasters.com
Karen Hanna, associated editor
Related:
The electric vehicle revolution opens doors for plastics, say industry experts.
Pressure is mounting for mold makers to adapt.
3-D printers carve out niche in automotive marketing.
Car-parts molders steer course for success as market evolves.
Changing designs create opportunities for injection molding machinery makers.
Ron Shinn: Electric vehicles are different, so processors need to adapt.
Karen Hanna | Senior Staff Reporter
Senior Staff Reporter Karen Hanna covers injection molding, molds and tooling, processors, workforce and other topics, and writes features including In Other Words and Problem Solved for Plastics Machinery & Manufacturing, Plastics Recycling and The Journal of Blow Molding. She has more than 15 years of experience in daily and magazine journalism.
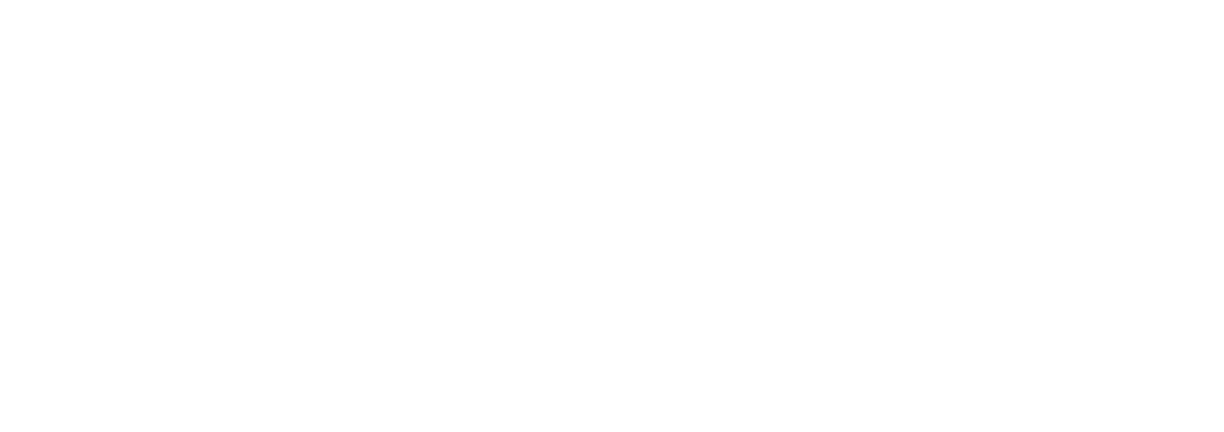