Changing car designs create opportunities for molding machinery makers
By Karen Hanna
Automakers’ continuing efforts to reduce vehicle weight and improve on early versions of electric vehicles are among the challenges that injection molding machinery makers are helping their customers confront.
With the focus on electric vehicles, Füreder said he sees even more opportunity for injection molders, as concerns about battery range wthis lightweighting trend.
“Injection molding will play an even more prominent role in the future, as the proportion of plastics in vehicles continues to rise,” Füreder said.
The standards, too, are becoming stringent, said Neil Dueweke, Fanuc’s VP of automotive OEM sales, materials joining, new domestic and body-shop execution groups.
“The opportunity for plastic parts to deliver both needed weight reduction while providing a ‘high image’ level in terms of fit and finish has never been greater,” Dueweke said.
Bill Duff, GM of sales and marketing for Yizumi-HPM, said his company has seen continued demand for foaming technologies, such as MuCell from Trexel Inc.
“It can take 15 to 20 percent of the weight out of the part, and still give you a very stable and strong part. ...And that’s been going on for a lot of years, the MuCell process, or gas-assist, is another one that we’ve used for thick-walled parts,” he said.
In addition to parts they have traditionally made from plastics, manufacturers have been able to replace metal in some parts. With the launch of electric vehicles, demand for plastics will be even higher, Füreder said.
He explained that compared with combustion-engine vehicles, electric vehicles employ more connectors and cable entry seals, as well as high-precision, liquid-silicone grommet seals.
With more parts like these in demand, Füreder is optimistic about the role injection molding will play in the automotive industry in the years to come.
“It enables lightweight construction to be combined with functional integration and high-cost efficiency in mass production,” he said.
Exterior and under-the-hood components are not the only areas of the car where OEM representatives see opportunity.
The transition to electric vehicles requires more than just replacing the engine with a battery, Dueweke observed.
He pointed out that, in traditional cars, the engine supplies heat. Automakers will increasingly turn to foam materials, such as expanded PP and expanded PS, to insulate vehicle interiors. Thermal insulation in doors and headliners will help maintain the temperature with the car’s interior, as well as protect the battery against sudden temperature changes that could lead to the failure of the propulsion system.
Consumers’ high expectations regarding vehicle appearance and comfort will influence just how plastic is used inside vehicles, according to Dueweke.
He pointed to the sleek, space-age designs of Torrance, Calif.-based Canoo, an electric-vehicle maker hoping to launch its Lifestyle Vehicle by subscription.
Dueweke said interior finishes now are “light years” removed from the cars of 30 years ago.
“Companies like Canoo are working hard to provide an enjoyable riding experience with amenities similar to what you’d find in your family room. Leg room to stretch out or potentially lie down is planned,” Dueweke said.
“Whether it’s a robot loading and unloading an injection molding machine; applying, repeatedly, an adhesive bead to bond two plastic parts together; or automatically stacking your finished products into shipping containers, the business case in 2021 is easily made for inclusion of robots in many plastic parts making facilities,” Dueweke said.
As the auto industry evolves, Duff, too, noted that some of the demands required of the plastics industry remain the same: precision, repeatability, quality.
“With the modern controls and motion-control systems, we’re able to have a very repeatable cycle, so that, when they're trying to reduce the weight of a part, they’re relying on the machine to be able to perform at a higher level. The machine-controls technology and the motion-control systems, whether it be full-electric, or servo-hydraulic, we’re able to get a very repeatable process. And that’s really required on a part where you’re trying to reduce weight, and keep the integrity of the part at a certain level,” he said.
Engel Machinery Inc., York, Pa., 717-764-6818, www.engelglobal.com
Fanuc America Corp., Rochester Hills, Mich., 248-377-7000, www.fanucamerica.com
Yizumi-HPM Corp., Iberia, Ohio, 740-382-5600, www.yizumi-hpm.com
Karen Hanna, associate editor
Related stories:
The electric vehicle revolution opens doors for plastics, say industry experts.
Pressure is mounting for mold makers to adapt.
3-D printers carve out niche in automotive marketing.
Car-parts molders steer course for success as market evolves.
Ron Shinn: Electric vehicles are different, so processors need to adapt.
Hot runners inject new options for making tough automotive parts.
Karen Hanna | Senior Staff Reporter
Senior Staff Reporter Karen Hanna covers injection molding, molds and tooling, processors, workforce and other topics, and writes features including In Other Words and Problem Solved for Plastics Machinery & Manufacturing, Plastics Recycling and The Journal of Blow Molding. She has more than 15 years of experience in daily and magazine journalism.
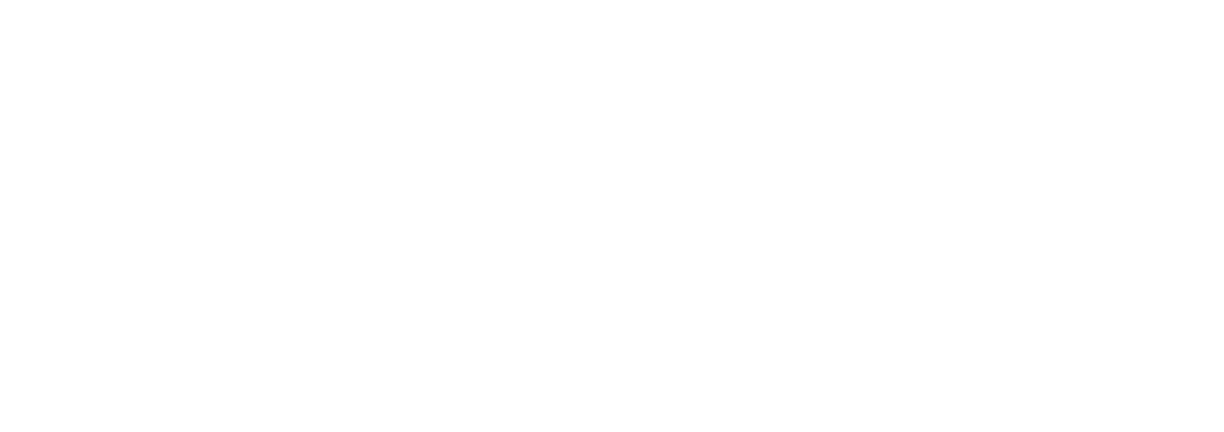