3-D printers carve out niche in automotive manufacturing
By Bruce Geiselman and Karen Hanna
Although it is best known for prototyping and short runs, additive manufacturing could play a bigger role in the production of auto parts, as carmakers navigate a period of rapid change.
"There’s a lot of innovation happening in the space, fundamental innovation," said Kevin Baughey, 3D Systems’ segment leader for transportation and motorsports.
The potential of additive manufacturing continues to draw attention from the auto industry, despite challenges, such as processing-time limitations. Experts predict it will gain prominence as the industry transitions from internal-combustion-engine platforms to electric vehicles. With carmakers seeking to customize and innovate, 3-D printing could cut the time and expense involved in tooling production, as well as provide greater design freedom.
Creating a personal touch
“In the future, automakers will be able to design customized, 3-D printed interiors that reflect [buyers’] personalities and preferences while still maintaining the highest safety standards, creating a better driving experience for consumers and new revenue streams for this massive industry,” said Jon Wayne, head of HP’s 3-D printing and digital manufacturing’s commercial business.
Along with Carbon and EOS, HP provides the technologies to allow BMW Mini customers to 3-D print decorative trim, including covers for their cars' dashboards.
In addition to the Mini project, BMW has been printing a limited number of production parts for the Rolls-Royce Phantom and the BMW i8 Roadster. In 2019 alone, the BMW Group printed over 300,000 parts, including a convertible roof bracket for the i8 Roadster.
HP’s Multi Jet Fusion printers also are among the portfolio of technologies at GM’s new 15,000-square-foot Additive Industrialization Center just outside Detroit. The center’s 24 3-D printers use a variety of technologies, including selective laser sintering, selective laser melting and fused-deposition modeling, to produce plastic and metal parts.
“This is just the beginning,” said Audley Brown, GM’s director of additive design and materials engineering. “Ultimately, we see the potential for 3-D printed parts to be used in a wide variety of production applications — from greater personalization options for new-vehicle buyers, to unique accessories and reproductions of classic car parts.”
The Cadillac CT4-V Blackwing and CT5-V Blackwing will be the first GM production vehicles to have 3-D printed parts, including an emblem on the manual shifter knob, an electrical harness bracket and two HVAC ducts. Cadillac expects the cars to become available late this summer.
Moving into production
Unlocking additive manufacturing’s potential requires accounting for its current restrictions.
Modi believes 3-D printing won’t become commonplace until sometime after 2030.
But 3-D printing is faster than tooling development, giving it an edge when it comes to producing some types of parts.
“Compared to traditional processes, 3-D printing can produce parts in a matter of days versus weeks or months at a significantly lower cost,” Brown said.
Increasingly, carmakers are using 3-D printing to make short-run parts, as well as tooling, like jigs and fixtures for robots, Baughey said.
3D Systems’ partners are exploring ways to exploit 3-D printing’s advantages, and at bigger volumes, Baughey said.
“It's starting out in what we call the high-value, low-volume production, things like investment castings for gearbox assemblies,” Baughey said.
New materials, new opportunities
One major step forward is the continuing development of new materials that can handle high temperatures or continuous, long-term use.
This could allow automakers to produce parts from plastic that previously have been made from metal. The freedom of design afforded by 3-D printing could make the technology appropriate for some under-the-hood parts.
“PP allows automakers to replicate a traditional material that’s used for a wide variety of interior, exterior and under-the-hood parts. These parts, such as ducts to help direct air and gas flow and gas/liquid separators, offer significant advantages to automotive customers,” he said.
Additive manufacturing might be the next “big thing” as automakers shift from metal to plastic under the hood, said Dan Hearsch, a managing director of AlixPartners and a leader in its automotive industrials practice.
“A lot of people are talking about carbon fiber,” Hearsch said. “I think carbon fiber does have a place, but additive manufacturing looks like it’s going to allow companies to jump past that in some cases and use higher-tech materials.”
Some 3-D printed parts in the future could be hybrids that include both metal and plastic, he said. For example, metal components could be embedded inside plastic or joined together with plastic in a part that could not be created with traditional insert molding.
“You could 3-D print plastic and metal in a much more intricate geometry,” Hearsch said.
Design freedom, the elimination of the costs and time associated with tooling development and the ability to produce one-off parts quickly make 3-D printing technologies valuable tools for an automotive industry that’s looking to evolve.
“Already, the automotive industry has turned to 3-D printing technology toManufacturers' partnerships with 3-D printer OEMs could drive significant advancements for 3-D printing automotive solutions in materials, software and equipment, 3D Systems' Baughey said.
“This is definitely a bi-directional relationship,” he said. “We partner with and we have agents with our OEMs and tiered suppliers to drive those requirements into the product roadmap.”
Bruce Geiselman, senior staff reporter
Karen Hanna, associate editor
Contact:
3D Systems Inc., Rock Hill, S.C., 888-598-1438, www.3dsystems.com
HP Inc., Palo Alto, Calif., 650-857-1501, www.hp.com
Related stories:
The electric vehicle revolution opens doors for plastics, say industry experts.
Pressure is mounting for mold makers to adapt.
Car-parts molders steer course for success as market evolves.
Changing designs create opportunities for injection molding machinery makers.
Ron Shinn: Electric vehicles are different, so processors need to adapt.
Hot runners inject new options for making tough automotive parts.
Bruce Geiselman
Senior Staff Reporter Bruce Geiselman covers extrusion, blow molding, additive manufacturing, automation and end markets including automotive and packaging. He also writes features, including In Other Words and Problem Solved, for Plastics Machinery & Manufacturing, Plastics Recycling and The Journal of Blow Molding. He has extensive experience in daily and magazine journalism.
Karen Hanna | Senior Staff Reporter
Senior Staff Reporter Karen Hanna covers injection molding, molds and tooling, processors, workforce and other topics, and writes features including In Other Words and Problem Solved for Plastics Machinery & Manufacturing, Plastics Recycling and The Journal of Blow Molding. She has more than 15 years of experience in daily and magazine journalism.
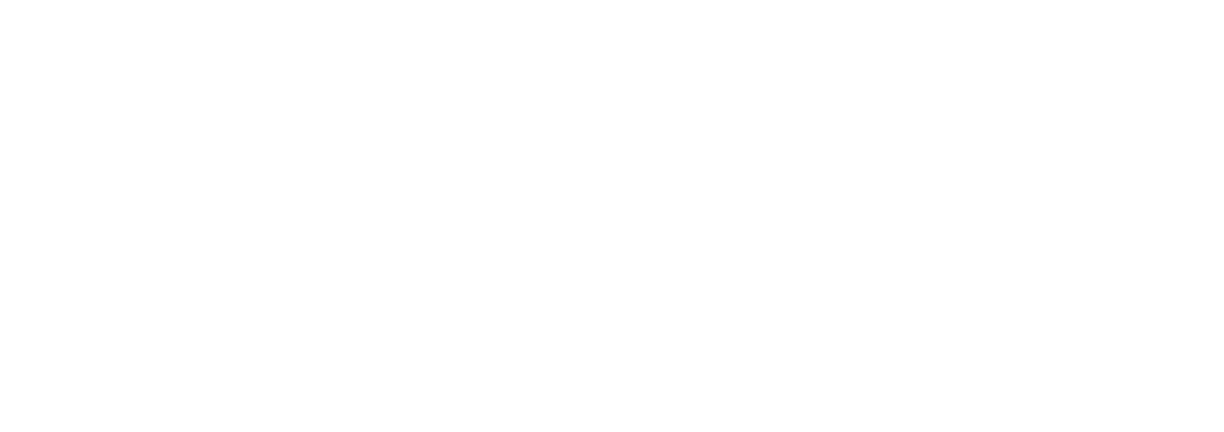