I am a little bit uneasy about the high-speed shift to electric vehicles. Maybe it is an age thing or maybe I still worry too much about the battery going dead late at night on a lonely road. Or maybe I just like the ethos of all things internal combustion.
Our cover story this month is about cars, trucks and plastics. The future is definitely all about electric motors. Does it mean internal combustion engines will no longer be available? I hope not.
But the shift to electrification is happening and has consequences for the plastics industry. Opportunities? Yes! Transition pains? Almost certainly!
There is no doubt that hybrid automobiles and early electrics have caused metal parts to be replaced with plastic to reduce overall vehicle weight. I have never seen an estimate on how much business it has generated for the plastics industry, but it is certainly substantial.
While much of the most intense vehicle development focus has now shifted away from lightweighting toward battery development, lightweighting will continue. The redesigning of cars and trucks also means new opportunities for consolidating multiple parts into one, which reduces manufacturing, labor and spare parts costs.
Plenty of electric vehicles are available for under $50,000, including the BMW i3 (base price $44,450), Chevrolet Bolt ($36,500), Ford Mustang Mach-E ($42,895), Hyundai Kona Electric ($37,390) and Ioniq Electric ($33,245), Mini Electric Hardtop ($29,900), Nissan Leaf ($31,620), Tesla Model 3 ($37,990) and Volkswagen ID.4 ($39,995). This list features subcompacts, small crossovers, midsize cars and small SUVs, with battery ranges of 110 to 263 miles. A big selection of electric pickup trucks is just around the corner.
Prices are going to come down and choices are going to increase significantly as car makers reorient their product lines. We might be surprised at how the electrification of vehicles builds momentum in the next 10 years.
Climate change should be important to everyone, and switching to zero-emission vehicles, while not the whole answer to correcting the damage we have done to the environment, is an important step.
The automotive industry drives a big portion of the North American plastics industry, and we must face the fact that it is on the cusp of the biggest change in its history.
What does it mean for plastics processors?
Processors will need to be flexible, work with and educate new car manufacturers, and, in some cases, move away from the mindset that automotive programs mean years-long part runs.
There could be a period when some processors can no longer compete for the automotive business they have now.
New grades of steel and aluminum will also mean additional competition for plastics in lightweighting, industry analyst Shashank Modi told senior staff reporter Bruce Geiselman.
Dan Hearsch, another automotive industry analyst, described lightweighting as a mature movement.
Mold industry analyst Laurie Harbour predicts mold makers will have to cope with automakers selling models in lower volumes and putting more cost pressures on mold makers, at least for the foreseeable future.
Molding a plastic fender is a prized job for processors, but many future opportunities might be related to sensors, electrical componentry and computer controls.
The number of cars and light trucks being built each year probably will not decline once automakers have made the shift to electrics. Processors making parts for automobiles powered by internal combustion engines will still need to make parts for electric-powered vehicles. But the plastics components are going to evolve in ways we really cannot yet know.
A processor that wants to replace an automotive program that disappears with a similar job might have to deal with a customer that has a culture and supply chain that are different from the automotive companies we know today.
Here is another interesting automotive trend that could have long-term impact on plastics processors.
I saw a post on our Nextdoor neighborhood social media website from a young man who was looking for a small part for a Nissan Leaf charging port cover. He had made a repair to the charging door latch on his Leaf and in the process lost a small part.
He was not trying to buy a replacement plastic part. He was looking for another Leaf owner who would let him measure the part so he could duplicate it on his own. “I have 3-D printers. I can make the part myself,” he wrote.
There is a processor somewhere that won’t get to make that part.
It would also appear that future generations of shade-tree mechanics will need a laptop to read engine and drivetrain computer codes and a 3-D printer to make parts. That is an interesting thought.
Ron Shinn, editor
Related stories:
The electric vehicle revolution opens doors for plastics, say industry experts.
Pressure is mounting for mold makers to adapt.
3-D printers carve out niche in automotive marketing.
Car-parts molders steer course for success as market evolves.
Changing designs create opportunities for injection molding machinery makers.
Hot runners inject new options for making tough automotive parts.
Ron Shinn | Editor
Editor Ron Shinn is a co-founder of Plastics Machinery & Manufacturing and has been covering the plastics industry for more than 35 years. He leads the editorial team, directs coverage and sets the editorial calendar. He also writes features, including the Talking Points column and On the Factory Floor, and covers recycling and sustainability for PMM and Plastics Recycling.
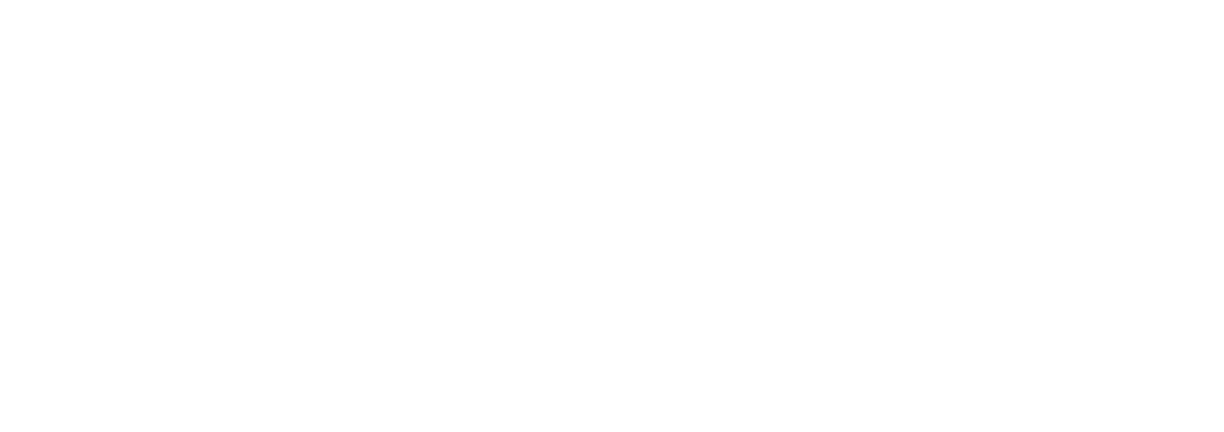