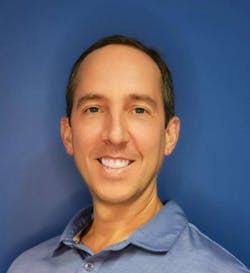
By Bruce Geiselman
With experience in integrating industrial automation since 1989, Applied Manufacturing Technologies (AMT) can draw up plans for both existing and new plants. But greenfield work is easiest.
“With greenfields, you have a little bit of luxury to design your operation around the best and optimal flow. You have the luxury of looking at your plant holistically,” AMT President Craig Salvalaggio said. “If you look at it from a layout perspective, you can look at all your different processes from incoming product, raw goods and any type of process that you have — whether it is machining, painting, spraying, packaging — you can look at it from a nice material workflow.”
Most projects, however, don’t come with a clean slate.
“Most of our work is within existing factories where you’re limited by existing equipment, aisleways, people, fork-truck traffic, and trying to maneuver around that,” Salvalaggio said.
When helping a client design a plant, AMT uses a variety of discrete event-simulation software and 3D simulation tools to lay out the factory’s eventual look. The software can help a client not only see what a plant would look like, but also understand the size and type of workforce that would be needed, given varying levels of automation.
The software also can be used to plan for possible future automation, allowing a customer to visualize, for example, the effects of adding AGVs, AMRs or fork trucks. Each of those options might require a different layout as the vehicles have different turning radiuses and widths.
When designing new plants, Salvalaggio encourages companies to plan for future growth and the possible addition of automation because it is much easier to add automation in the future when such planning takes place. For example, AMT consultants might ask a client not only about current production volumes, but about projected volumes over the next five years.
“Then we help them lay out what’s called the factory of the future,” Salvalaggio said.
Manufacturing facilities where manual labor was used extensively often bring in integrators when planning automation. Labor or ergonomic issues, or the need to add a shift, can force companies to take a new look at technology.
“When that happens, they look at automating,” Salvalaggio said.
That puts a premium on space. When machines are close together, positioning a robot that might require a safety zone around it can be challenging.
As another example, Salvalaggio said an employer might have the people arranged in a C or an S curve to perform manual tasks. However, if the employer wants to perform the same tasks with automation, they might need a space with a long linear flow.
“And you may not have the space to do it,” he said. “A lot of times, you’re restricted by your current infrastructure and how the plant was designed. That’s probably about 90 percent of the automation going into plants right now.”
Bruce Geiselman, senior staff reporter
Contact:
Applied Manufacturing Technologies, Orion, Mich., 248-409-2000, www.appliedmfg.com
Bruce Geiselman | Senior Staff Reporter
Senior Staff Reporter Bruce Geiselman covers extrusion, blow molding, additive manufacturing, automation and end markets including automotive and packaging. He also writes features, including In Other Words and Problem Solved, for Plastics Machinery & Manufacturing, Plastics Recycling and The Journal of Blow Molding. He has extensive experience in daily and magazine journalism.