Key points
- Bioresins are gaining traction as governments and consumers are pushing for alternatives to traditional plastics in single-use applications, but shortages, high prices and processing difficulties hinder widespread use.
- Biopolymers are heat- and shear-sensitive, requiring special processing techniques to prevent degradation during extrusion or compounding.
- Companies like Magic and Bekum America are working with bioresins in blow molding, using specialized extrusion heads and other machinery modifications, in addition to tight temperature control.
- Continued advancements in materials, technology and cost reduction could drive wider adoption.
By Bruce Geiselman
Governments and consumers are pushing for stores, restaurants and manufacturers to eliminate the use of traditional plastics in single-use applications including straws, food packaging and grocery bags.
That has led to increased interest in biodegradable polymers, which typically decompose more quickly in the environment.
But efforts to switch to biopolymers face hurdles due to a shortage of materials, high prices and challenges in processing, according to equipment manufacturers familiar with the trend. However, biopolymer production is increasing, and solutions to the processing challenges are available.
“In the last few years, we’ve had more interest, more new players coming onto the scene running bio-related compounds in our lab,” said Dean Elliott, technical processing manager at Entek, a global extruder manufacturer based in Lebanon, Ore. “We’ve sold some equipment to some new customers in that space, some of it in California, but it seemed like, back in the early 2000s, the bioresin market was very active. There was a lot going on, and then it seemed like it went quieter for a number of years, but it seemed to have picked up a little bit more in the last few years.”
He said polyhydroxyalkanoates (PHAs) have generated significant interest.
In 2020, for example, Bacardi, the world’s largest family-owned spirits company, announced plans to introduce what it called “the world’s most sustainable spirits bottle” made with Nodax, a PHA derived from the oil of canola plant seeds and produced by Danimer Scientific.
According to Danimer Scientific and Bacardi, while a regular plastic bottle can take more than 400 years to decompose, a PHA bottle biodegrades in a wide range of environments, including compost, soil, freshwater and sea water, and after 18 months can disappear without leaving behind harmful microplastics.
More on bioresins
Plastics machinery makers can help processors adapt to biomaterials. Often, the machines can run without modifications.
What are biomaterials? Terms to know.
Biomaterials are drawing interest from the plastics industry, but supply so far is weak, driving up prices.
On its website, Danimer Scientific says applications for PHA are enormous and include straws, cups, lids, bottles, produce bags, shopping bags, utensils, diaper linings, plates, wipes, toys, trash bags, seals and labels.
PHAs offer decent physical and mechanical properties, Elliott said.
However, he said, depending on the intended use, biopolymers often do not meet product property requirements in their pure form. Additives, fillers, impact modifiers, masterbatches and sometimes a portion of petroleum-based polymers are compounded into a biopolymer matrix to enhance the properties of the biopolymer or to reduce costs. Often, biopolymers are compounded on a co-rotating twin-screw extruder, which can be challenging.
Compounding: Control shear, heat
Biopolymers tend to be shear-sensitive, and can experience physical property degradation, Elliot said. Compounders must take care to thoroughly distribute any fillers or additives without degrading the material. Shear can be reduced by slowing the extruder speed while increasing the gap between the extruder screws and the barrels.
“When you open up that gap, the shear intensity gets less,” Elliott said. “Or you slow down the screws, and the shear intensity gets less, but you can’t run your screws at 5 or 10 rpm because you won’t be able to push any materials through. It’s a balance.”
That also is why sometimes when running biopolymers, a melt pump is added at the end of the extruder to help move the material through the die.
In addition, configuring the melting and mixing zones of the screw with narrow disc kneaders is less aggressive and results in lower melt temperatures. Elliott also recommended avoiding reverse- convey screw elements that pump the compound back toward the extruder throat because while it can result in more thorough mixing, it is more intensive and increases residence time, which could degrade the temperature-sensitive bioresins. He also recommended avoiding short, aggressive mixing zones by spreading out the mixing and melting zones to limit shear and heat from the mixing screw elements.
The hygroscopic nature of bioresins can complicate mixing on a co-rotating twin-screw extruder.
To prevent them from absorbing moisture, the materials should be stored in sealed containers. Using a melt pump between the exit of the extruder and the die can increase throughput rates, create a more stable flow of the extrudate and minimize melt temperature rise. Melt pumps have pumping efficiencies of 25 percent to 35 percent, compared with a co-rotating twin-screw extruder, primarily a mixing device, which is only 5 percent to 15 percent efficient as a pump, he said.
“You need vents and vacuum vents more than a traditional machine set up for a traditional polymer,” Elliott said.
Because biopolymers are heat-sensitive and degrade faster at elevated temperatures than their petroleum-based counterparts, Elliott recommends lowering the temperature on barrel heaters or turning off the heaters when the extruder is not running.
If abrasive fillers are compounded with the biopolymer, Elliott recommends metallurgy that protects the screw and barrel against corrosion and premature wear.
Meanwhile, the move toward bio-based materials isn’t limited to plastics. Companies also are developing bio-based additives and fillers, Elliott said.
“We have a customer now that we are working with on a bio-based carbon black,” he said.
“The source of that carbon black comes from an agricultural source. This comes from a bio-based source — pyrolyzing agricultural material to turn it into carbon black. So, it’s not just biopolymers — it’s also the additives and the fillers.”
Adjustments for blow molding with bioresins
Magic, an Italy-headquartered blow molding machine company with U.S. offices in Whitmore Lake, Mich., and Bekum, a German company with American offices in Williamston, Mich., have been working with clients interested in blow molding bioplastics.
Magic has been working with bioresins in its lab and has sold a machine to a customer in North America specifically for running bioresins, Spiga said. As a result of its experience, Magic can support customers in setting up machines to run bioresins, he said.
Modifications to the extruder and blow molding heads are necessary to accommodate bioplastics, although the changeover requirements are not extensive. “But how we do it is our secret,” he said.
Joe Slenk, applications manager with Bekum America, said one secret to successfully processing bioresins is to ensure your extrusion blow molding machine is properly equipped. As with twin-screw extruders compounding bioresins, extrusion blow molding machines need a modified screw.
“It does take a specialized feed screw to run these,” Slenk said. “Depending on the material type and grade, you would need a different feed screw. Most extrusion blow molders have a polyethylene feed screw that’s going to be incompatible with running a bioresin.”
The specialized screw is important because biopolymers like PHA and PLA have a “very, very small process window,” Slenk said. “The materials tend to be very heat-sensitive, so maintaining a correct stock temperature is absolutely critical. A couple-of-degree temperature change can mean the difference between running a good process and not making anything at all.
“We’ve also seen extrusion heads need to be of a center flow design because the reknitting of the biomaterials is a little more difficult, so some of the overlapping heart-shaped curve designs don’t lend themselves very well to running these materials.”
Another specialized blow molding machine feature required for many biopolymers is a hot knife, needed for cutting the parison.
“It’s a heated metal blade that kind of burns through the material because it tends to be a little bit tacky,” Slenk said. “Cold blades [used with HDPE blow molding] don’t work very well for parison cutting.”
Since bioresins tend to be hygroscopic, the materials must be dried before being blow molded, which isn’t necessary for traditional materials, like PE.
“They would need to add a dryer next to the machine,” Slenk said.
Processing scrap created during the blow molding process also can be more of a challenge with bioresins, Slenk said.
“Adding the regrind back in can be a challenge because now the material has an additional heat history, so, its melting characteristics are a little different and it tends to want to degrade a little more on that second heat cycle,” Slenk said. “We haven’t tried to do anything with regrind. That would certainly be a challenge.”
Bekum America’s experience with bioresins has, to date, focused on trials with customers interested in seeing the potential for the materials in blow molded bottles.
“We’ve done several trials with several different materials, different suppliers and grades,” Slenk said.
That experience has helped Bekum America develop knowledge about processing bioresins and how blow molding machines must be modified to accommodate the materials.
“Again, it’s a very small processing window, and that makes everyday operation of the machine a little more challenging,” he said. “At the end of the day, we can supply a machine that’s well-equipped to run bioresins.
“Temperature is absolutely key to these materials, including running a heated mold, so a Thermolator [temperature control unit] would be required on the machine as well.”
When processing a traditional plastic, temperature variations of only a few degrees might not be noticeable to a machine operator, but such variations can be “very noticeable and cause some problems” when using bioresins, Slenk said.
The challenges of processing bioresins might be limiting their adoption.
“I think there are a couple of factors involved in why they haven’t taken off,” Slenk said. “No. 1, I think the material technology still has a little way to go. We’re dealing with gravity when we’re doing extrusion blow molding, so we’re extruding a parison and hanging it out there before the mold closes. So, melt strength becomes very important. The melt strength of these materials is OK, but it’s not fantastic. That’s where the stock temperature comes into play. I think as the materials get more user-friendly, there could be more adoption. The simpler a material company can make it to run, the more people are going to be able to run it.”
The other issue is cost, he said. Bioresins can cost several times as much as traditional resins.
Despite the challenges, Slenk thinks bioresins will be around long-term.
“I don’t think it’s going to go away anytime soon,” he said. “With all the talk about sustainability, I think this is going to have a niche in the market.”
Bioresins might not go mainstream anytime soon, but they could be appropriate for certain applications, such as for high-end cosmetic bottles. In that case, those niche items would appeal to customers who might be more willing to pay more for a biodegradable material that’s good for the environment.
“I see that type of market being a success,” Slenk said.
Contact:
Bekum America Corp., Williamston, Mich., 517-655-4331, www.bekumamerica.com
Entek, Lebanon, Ore., 541-259-3901, www.entek.com
Magic North America, Whitmore Lake, Mich., 734-358-7722, www.magicnorthamerica.com
Bruce Geiselman
Senior Staff Reporter Bruce Geiselman covers extrusion, blow molding, additive manufacturing, automation and end markets including automotive and packaging. He also writes features, including In Other Words and Problem Solved, for Plastics Machinery & Manufacturing, Plastics Recycling and The Journal of Blow Molding. He has extensive experience in daily and magazine journalism.
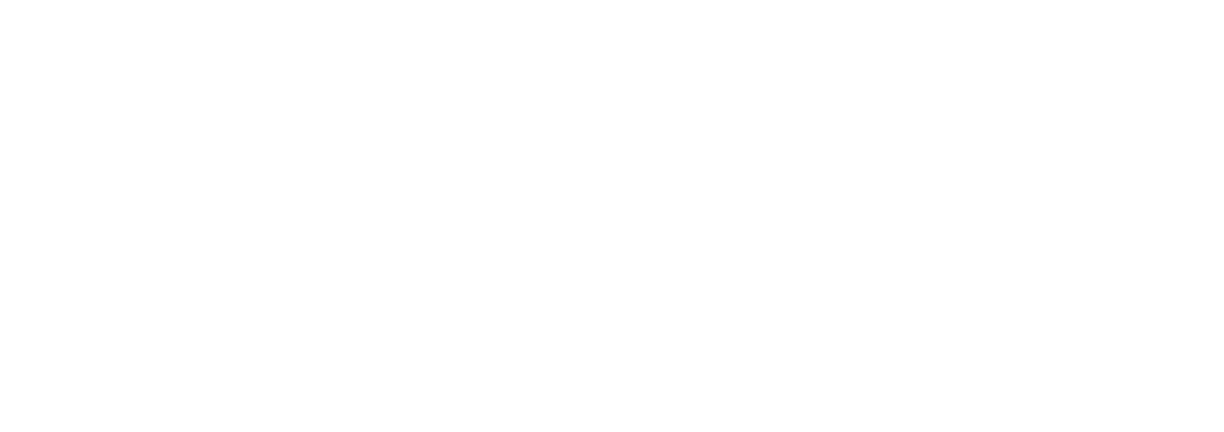