By Bruce Geiselman
A new biodegradable resin can degrade safely in nature if it escapes recycling and ends up as litter, according to Symphony Environmental, which developed it.
The new product, named NbR (Natural biodegradable Resin), is made with natural minerals to reduce the amount of fossil-derived polyethylene (PE) or polypropylene (PP) used, and it is compatible with traditional plastics recycling streams.
It is available worldwide, including in the U.S.
“This is a major innovation as it will make a dramatic environmental difference by reducing the fossil-derived content of plastic products by 20 percent, cutting CO2 emissions and reducing microplastics,” company CEO Michael Laurier says.
“Like ordinary plastic products, a product made with NbR can be recycled and made with recyclate, but it will biodegrade within months if exposed in the open environment instead of fragmenting into microplastics and lying or floating around for decades.”
The company has applied for trademarks. It is not releasing details about which minerals it uses in producing the resin.
“This is currently a trade secret,” Laurier wrote in an email interview with Plastics Recycling.
NbR packaging will completely biodegrade within two to three years or even less time, depending on the stabilization of the particular product, the age of the product at the time of disposal, and the extent to which it has been exposed to heat and sunlight, he wrote.
“It contains a special ingredient that accelerates the reduction of the molecular weight of the polymer, allowing it to be consumed by bacteria and fungi in the open environment,” he wrote. “It does not need to be taken to a composting facility because it will degrade anywhere with access to oxygen. By reducing the molecular weight, the special ingredient converts the fossil-based polymer into oligomers, ketones, aldehydes, etc., which are biodegradable and not plastic.”
But manufacturers and consumers do not need to worry about NbR packaging degrading prematurely while in use.
“It will not degrade prematurely because Symphony adjusts the balance between catalysts and stabilizers within the NbR to ensure the product has the shelf and service life the commercial end-user requires,” Laurier says.
The addition of NbR to PE or PP has no impact on the plastics’ recyclability, he wrote.
“NbR will typically form 25 percent of each plastic product and (unlike plastic marketed as ‘compostable’) would have no impact on traditional mechanical recycling and no effect on the recycled plastic.”
NbR is appropriate for use in a variety of packaging and other products—“all short-life products made with PE or PP, such as packaging, garbage sacks, bottles, pallet wrap, etc.,” Laurier says.
In addition, NbR offers improved post-mold shrinkage and barrier properties, according to the company.
Symphony began developing the technology in 2011, but growing demand for more-sustainable plastics led the company to upgrade the product and introduce NbR last year. Demand for more environmentally friendly resins coincides with a growing demand for packaging in the pharmaceutical, food and beverage, consumer goods and ecommerce sectors, according to the company. The global resin market, valued at $556 billion in 2023, is projected to grow to $859.27 billion by 2032, according to the company.
NbR complies with U.S. Food and Drug Administration regulations for food-contact packaging, and it has been tested for biodegradability and non-toxicity, according to the company.
Contact:
Symphony Environmental, Borehamwood, England, 44-208-207-5900, www.symphonyenvironmental.com
Bruce Geiselman | Senior Staff Reporter
Senior Staff Reporter Bruce Geiselman covers extrusion, blow molding, additive manufacturing, automation and end markets including automotive and packaging. He also writes features, including In Other Words and Problem Solved, for Plastics Machinery & Manufacturing, Plastics Recycling and The Journal of Blow Molding. He has extensive experience in daily and magazine journalism.
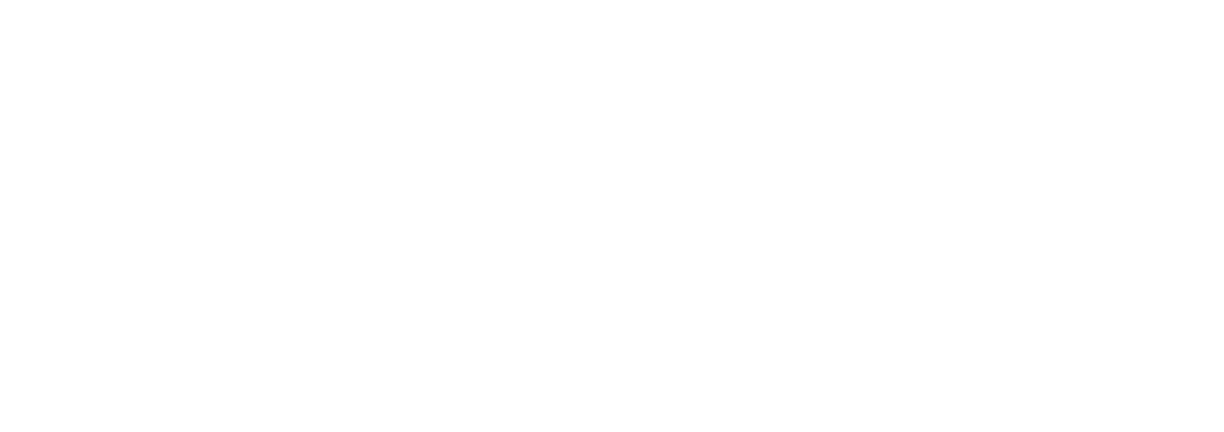