By Bruce Geiselman and Karen Hanna
For a heavily regulated industry that typically moves in stops and starts, the early stages of the pandemic presented a need for speed.
Injection molding machine (IMM) manufacturers, among others, responded.
“In the last few months, the biggest challenge was to get machines and system solutions very quickly, as many projects were directly related to COVID-19. Medical enquiries therefore enjoyed the highest priority in Engel's worldwide production plants and were processed with highest priority,” said Christoph Lhota, VP for the medical division of Engel Austria GmbH, based in Schwertberg.
Like Engel, many OEMs reported they have tried to prioritize orders related to medical parts manufacturing.
But, while COVID-19 case numbers are falling and vaccinations are readily available in the U.S., OEMs still are coping with supply-chain disruptions, as well as the technological challenges inherent in medical molding — trends toward exotic materials, smaller size, greater precision.
The machine demand scene
Many countries are unable to produce essential medical goods without depending on international trade, said Cyril Liang, VP for sales and service for Bole America.
“Yes, supply-chain is very tight,” he said. “Not just raw material, but also equipment. As an equipment supplier, our manufacturer is in China and we have a very complete supply-chain list for machine parts and keep updating to guarantee our production and delivery. However, the increase in part prices will inevitably cause the cost of machines to rise. It is a problem that manufacturers, agents and customers have to face together now.”
Tony Marchelletta, the U.S. sales manager for Sumitomo (SHI) Demag, said his company has been able to continue to serving its customers because it has a large inventory of machines and a substantial field-support infrastructure.
However, outside of his company, he knows many molders have faced “a significant challenge” in sourcing machines.
“Although this challenge was due primarily to the COVID-19 pandemic, medical molders frequently have difficulties with timely machine delivery and startup. A new medical product may take years to get validated and FDA approval, and many fail to get approval at all,” he said. “This process often results in a medical molder having to wait and then gear up for production with virtually no lead time. The second problem is that many machines coming in from abroad have a long delivery time, plus a long wait for installation.”
According to Wittmann Battenfeld, demand for machines, as well as robots, has outstripped supply. While the first three months of the pandemic brought economic shutdowns, the period since has been punctuated by sharp sales increases. With inventories low, prices have been rising, but logistical challenges have added to the pressure on the supply chain.
To cope, molders employ a variety of strategies, said Peter Gardner, business director for LS Mtron Injection Molding Machine USA.
“We have some U.S.-based customers who have supply-chain diversity initiatives. Some limit their machinery suppliers to those who produce equipment in regions which are more geopolitically stable with regards to their relationship with the USA. For others, they are seeking to avoid punitive tariffs and high import duties. This limits choices even more and constrains quick availabilities of machines,” Gardner said.
He noted the favorable trading partnership of the U.S. and South Korea, where LS Mtron makes its machines. Because it has own steel casting facility in South Korea, the company can fulfill most orders within 12 weeks, and importers of machines entering the U.S. are responsible for no duties or tariffs, he said.
Thomas Bontempi, head of medical business development at Husky, said the company has seen shifts in the types of machines on order.
“The mix of product is slightly changed because of the COVID impact. COVID-driven laboratory applications have been high, even with constraints in the supply chain,” he said.
Fraying links along the supply chain
Machines aren’t the only essentials in short supply. Resin and labor also have been hard hit.
For Husky, resin shortages have presented an opportunity to provide service.
“Everything has contracted,” Bontempi said. “Supply chains have been cut in the midst of the pandemic. … We hear of some shortages, but it's not the same for all the materials. I heard about polypropylene being constrained, but I haven't seen the same for PET, for example.”
Because Husky manufactures not only IMMs but also hot runners and molds, it has many opportunities to optimize processing and reduce consumption of material through lightweighting.
In addition, Husky can help customers adapt to processing lower-cost materials as an alternative to high-cost, or hard-to-find, resins.
Wittmann Battenfeld reported that some molders are altering production schedules to accommodate lower-than-expected resin supplies.
OEMs also are looking to help their customers deal with the U.S. labor shortage, emphasizing the same solution they’ve employed to steer through the pandemic — Industry 4.0 and web-enabled tools that allow remote access to machine data, insights and training.
“One way to solve this worker shortage is to provide the molder with the tools for allowing their in-house process and production experts a way to manage a greater number of machines, even remotely,” Gardner said.
For instance, Engel’s Lhota cited his company’s intelligent assistance systems, which adjust the process parameters cycle by cycle based on current conditions. The company’s iQ weight control automatically compensates for external influences such as fluctuations in the raw material, while iQ flow control enables precise, repeatable temperature control.
“Digital service products, such as remote maintenance and online support, are shifting into the focus. They are key to ensuring productivity and delivery capability. Even companies that have not worked with these systems in the past are now addressing the question of how they can safeguard their productivity in the event of future crises,” he said.
Parts on parade
Underlying the urgency of the supply-chain challenges is the mission of the ultimate end products. Increasingly manufactured from exotic, hard-to-process materials, medical parts are growing ever-smaller and more complex.
Taking a place of prominence in the pandemic are syringes and packaging, as well as testing devices. That could be the new normal, as booster shots might be required, as a representative for Wittmann Battenfeld pointed out.
Also growing in popularity, according to Juergen Giesow, director of technology and after sales service for Arburg in the U.S., are monitoring and measuring devices similar to smartwatches; devices and filters for managing diabetes; and lab-on-chip technologies. In addition, the pandemic has driven demand for pipette tips, and both prefilled syringes, complete with an oxygen barrier, and non-prefilled syringes, especially in the West, where health-care administrators have been transitioning from glass sharps.
Further complicating production are patient-specific parts, manufactured as one-offs. For these sorts of applications, Giesow said Arburg’s additive-manufacturing platform is especially adept.
“The trend towards more individual therapies increasingly requires production of small-volume batches, down to one-piece flow. Geometric freedom, combined with material freedom, enables the Freeformer to achieve entirely new plastic applications — including for use within the human body,” he said. “The open system is in high demand for additively manufacturing custom implants made of biocompatible, resorbable, sterilizable and FDA-approved original materials, individual orthotics and models for surgery preparation.”
Material matters
Based in Malmö, Sweden, parts maker TePe uses a KraussMaffei CXL 160 SilcoSet injection unit and a 256-cavity mold to produce toothpicks with a polybutylene terephthalate (PBT) body and an overmolded outer layer of liquid silicone rubber (LSR). Changing trends in plastics — including challenging materials, like LSR, which is growing in popularity — raise the level of processing difficulty.
“We were particularly impressed by the startup of the LSR components. After just three shots in semi-automatic mode, we were able to launch fully automated production,” said TePe's Product Developer Alexander Dingizian.
According to KraussMaffei, the SilcoSet technology, which is gaining in popularity, provides the precision and stability required for LSR, an extremely low-viscosity material.
LSR is appropriate in implants, respiratory masks and components for measuring instruments, among other products, Engel’s Lhota said.
“LSR is biocompatible and superior to organic polymers in terms of thermal and chemical resistance. It’s extremely resistant to environmental influences such as UV radiation and can be used over a very wide temperature range," he said.
Like LSR, bioresorbables can be used internally in devices such as implants. Increasingly, they’re also found in drug-delivery and diagnostic devices, Marchelletta said.
The Sumitomo (SHI) Demag representative summarized the challenges: “They tend to be highly sensitive to temperature and shear, making them prone to degradation. Physical properties can be altered without any visual indication in the part, driving the need for thorough and tight process control and validation.”
In addition, he said, they’re expensive, making efficiency and scrap minimization vital.
When handling resins used in parts designed for internal use, processors have a special responsibility.
“For a machine supplier like LS Mtron, it also means we must keep traceability records for the components which come into contact with these resins,” said Gardner.
In addition to LSR and bioresorbables, materials that offer sustainability benefits also are trending.
How materials are used also is evolving. For example, Arburg’s Giesow said, in some cases, processors are looking for ways to make parts that incorporate just one material, rather than several.
“This also allows for an increased recycling rate,” he said. “If you look at the amount of plastic waste generated in hospitals, for example, and their current recycling rate of only around 10 percent, we can clearly see that much more can be done to increase this percentage. In future, the increased use of bio-based, recyclable and biodegradable materials will be of help in this respect.”
On the other hand, Lhota said two-component applications also are becoming more common to produce devices such as pacemaker housings.
Betting big on micromolding
Medical devices run the gamut in terms of size, but small parts play a big role in the industry.
The smallest medical parts can require just fractions of a gram of resin.
Marchelletta pointed to the growing use of devices and parts that support minimally invasive procedures.
“These procedures require equipment and devices with smaller and more intricate components, and we’re also seeing requirements for ergonomic features and more multi-shot and insert/overmolding applications combining metals, TPE, etc.,” he said.
Arburg Allrounder work cells can produce micro parts for such procedures, Giesow said. Capable of performing a precise, economical and reproducible production process, the cells are fully equipped and automated. As an example, an Arburg Allrounder 270 A, equipped with a Size 5 micro injection unit and an 8mm screw produced LSR caps for microswitches, each weighing just 0.009 gram.
Sumitomo (SHI) Demag’s machines can take on small sizes, too, Marchelletta said. Together with the SL screw, which can handle even tough-to-process resins, the company’s SE30EV-A MM can handle the speeds, pressures, precision shot control and short residence time that micromolding requires, he said.
“From a product shot size perspective, our customers are currently molding medical parts anywhere from a fractional gram up to high cavitation molds with a shot size upwards of 80 ounces,” he said.
Prescription for production
For medical molders, precision, repeatability, flexibility and speed are just what the doctor ordered. But their requirements don’t stop there.
“As for the medical molding machine, the key is the stability of the production. So, the requirements of technologies such as high plasticization, precise injection, accurate platen position and stable ejection are very important and test the manufacturing level of manufacturers,” Bole’s Liang said.
For example, he said screws used in medical molding are different than general-purpose screws.
“Medical parts can be divided into PP, PVC and so on,” he said. “The screw design is different. Also, the injection speed requirement is different.”
One trend in medical molding is the use of higher-cavitation tooling, especially as demand for essential supplies surged during the pandemic.
“Increased cavitation has been a significant trend over the last year, due in part to the COVID-19 pandemic’s requirements for fast scale-up of production of medical disposables, personal-protective equipment and testing/diagnostic supplies,” Marchelletta said. “For example, some of our customers running pipette molds were previously running lower cavitation (32 cavity) in 100-ton machines on a 10-second cycle, and now we’re seeing up to 128-cavity molds running in our ultra-high-speed [500-ton] hybrid El-Exis SP 450 running on a 6-second cycle.”
In addition to churning out vials, pipettes and syringes in large volumes, molders also seek to optimize part wall thickness, which places demands on the machine.
In addition to the move toward higher-cavitation tooling, Marchelletta said molders want the flexibility to run multiple molds in one machine. They look for machines that have ample mold space, and can accommodate quick changeovers, high speeds and pressures. The ability to store mold data also is important.
Other machine characteristics important to medical molders include quality control, traceability and inter-equipment communications.
Keeping a clean room
Depending on the parts they’re producing, the work cell is just as important as the machine. Integrating all the components — and keeping them clean — is imperative.
As an example, Giesow described a cell at Chinaplas 2021, where Arburg produced 48 pipette tips every 6 seconds.
“There is a rising demand for turnkey projects in the field of medical technology,” he said.
At Chinaplas, the company showed a hybrid Allrounder 470 H featuring a modular design that makes it easily adaptable to changing requirements and different products. The cell had automation for removal, camera inspection and order picking.
Arburg provides support for molders from concept design to the start of production.
Considerations for the machine and environment include minimizing or eliminating the need for grease, and creating a specialized environment around the machine.
Bole’s Liang pointed out that exact work cell requirements vary depending on how parts are used.
“Based on the usage, it can be divided into invasive, non-invasive, inspection utensils, etc. These parts have different requirements for the production environment,” he said “Most of medical products are required to be sterile and dust-free. It can be produced in a clean room, but the cost is high. Another solution is … a positive-pressure system with sterilization,” Liang said.
Clean-room requirements favor all-electric machines, and LS Mtron is among several OEMs that offers them.
“Medical molders are requiring the machine which can be suitable for the clean-room molding application. For virtually 100 percent of medical molders, this means an all-electric molding machine is preferred,” Gardner said.
His company’s line ranges from 20 tons to 950 tons of clamping force.
While Liang said Bole’s machines use no lubricating oil or grease, and feature a galvanized platen surrounded by easy-to-clean stainless steel, LS Mtron offers greaseless tie-bar options.
“Instead,” Gardner said, “linear guide bearings are used to support and keep the moving platen parallel with the stationary platen. This eliminates the need for grease to be applied to the tie bars and prevents accidental contamination of the parts removal area with grease.”
The guides require grease, but they are located away from the area where parts come out.
As another option, the company also offers an FDA-approved greasing system supplied by LubeCorp Manufacturing Inc., Calgary, Alberta, for lubrication of the moving platen linear guide bearings.
In many cases, molders need dedicated clean rooms or production cells. But space is at a premium, according to Arburg’s Giesow.
“If the machine is in the clean room, the room needs to be substantially larger and requires much more air-handling equipment,” he said.
Turnkey cells, including clean-room cells, that incorporate all components are popular, some OEM representatives said.
For example, Marchelletta sees a trend toward complete, pre-tested production cells that are fully assembled and validated prior to installation. Coordination is key, requiring “effective communication and closer collaboration/project management between the machinery supplier, mold builder, auxiliary/automation equipment suppliers, molder and customer/brand owner,” he said.
Managing tight space is a challenge that Lhota said Engel’s machines are especially designed to meet.
Because they have no tie bars, they can accommodate larger molds than comparably sized IMMs from other OEMs, he said.
To maintain quality — while keeping humans away from sensitive parts — OEMs emphasized the ability to monitor machines remotely.
“LS Mtron’s molding experts and production managers can check the production and quality control systems of the machines remotely, without having to suit up and enter the clean-room area,” Gardner said.
Looking ahead
Efforts involving quality, cleanliness, precision, small size and challenging materials have collided during the pandemic with demands for speed and scale. But the expectations remain the same: “Maximum product safety, precision and efficiency in production, as well as complete documentation and traceability — these are the central requirements for any medical product manufacturer,” Engel’s Lhota said.
An endless — and growing— array of molded parts is used to diagnose and treat patients — disposable medical products and packaging; personal devices, such as hearing aids, catheters, monitors and home test kits; devices used by medical staff, such as surgical devices, endoscopic devices and implantables; laboratory devices, equipment and supplies; and pharmaceutical equipment and accessories, such as drug-delivery systems.
It’s why OEMs have prioritized the work of medical molders. Asked what comes next, representatives expressed uncertainty.
Husky’s Bontempi said he isn’t sure whether the supply-chain disruptions will inspire moves to decentralize production, or if newcomers might jump into the market to provide localized production. Whatever happens, he said Husky will be ready.
“This dynamic, we see it happening,” he said. “We think we are in a good position through our global network and presence to support any dynamic that moves forward.”
The experience of the past year highlights the global community’s vulnerabilities.
“After the epidemic, the original economic structure will be broken,” Bole’s Liang said. “All countries tend to develop and produce independently within its own product alliance, resulting in a relatively fragmented market; at the same time, the stock of medical products must be on the rise, and the demand also increased.”
Governments will realize they need to do more to shore up their stockpiles of essential supplies, like ventilators, he predicted.
“We need a local supplier which can manufacture it without import from other countries,” he said.
Karen Hanna, senior staff reporter
Contact:
Arburg Inc., Rocky Hill, Conn., 860-667-6500, www.arburg.com
Bole Machinery Inc., Stow, Ohio, 330-983-4700, www.boleamerica.com
Engel Machinery Inc., York, Pa., 717-764-6818, www.engelglobal.com
Husky Injection Molding Systems Ltd., Bolton, Ontario, 905-951-5000, www.husky.co/en
Krauss-Maffei Corp., Florence, Ky., 859-283-0200, www.kraussmaffei.com k
LS Mtron Injection Molding Machine USA, Peachtree Corners, Ga., 678-395-4389, www.lsinjectionusa.net
Sumitomo (SHI) Demag Plastics Machinery North America Inc., Suwanee, Ga., 678-892-7900, https://sumitomo-shi-demag.us
Wittmann Battenfeld Inc., Torrington, Conn., 860-496-9603, www.wittmann-group.com/en_us
More on medical parts and plastics
Parts makers step up their processes to meet needs
Injection unit, machine dedicated for test tubes among new processing technologies
Extruder OEMs respond to changing medical landscape
Auxiliary makers prioritized medical orders during pandemic
Robots shine in clean room duties
Economist: Run on medical goods provided jolt to plastics manufacturers
University speedily designs and prints nasal swabs
Geisinger’s 3-D lab printed devices to help health care workers stay safe
Beckwood Press designs compression molding equipment for medical devices
Quick deliveries, new products: Husky details COVID-19 response
Karen Hanna | Senior Staff Reporter
Senior Staff Reporter Karen Hanna covers injection molding, molds and tooling, processors, workforce and other topics, and writes features including In Other Words and Problem Solved for Plastics Machinery & Manufacturing, Plastics Recycling and The Journal of Blow Molding. She has more than 15 years of experience in daily and magazine journalism.
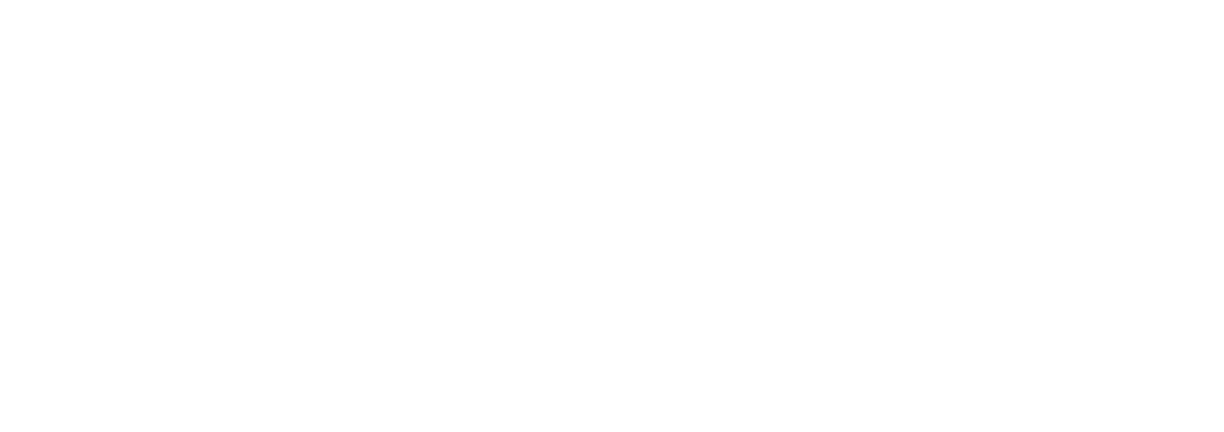