Injection unit, machine dedicated for test tubes among new processing technologies
By Bruce Geiselman and Karen Hanna
KraussMaffei, Engel and Husky are providing a shot in the arm for medical injection molders, with new technologies that respond to evolving production needs and changing requirements involving materials and parts.
The new developments include machine-monitoring technologies; an injection unit for liquid-silicone-rubber (LSR); a blood-collection-tube manufacturing system; a new system combining hot-runner and injection functions; and a cube mold technology.
Digitalization is one trend.
Making their debut earlier this year, KraussMaffei’s smartCube hardware and socialProduction mobile app bring social-media-type interactivity and immediacy to the collection of molding data. In the midst of the pandemic, such features have supported requirements for physical distancing and helped to alleviate labor-availability pressures.
SmartCube is hardware now standard on all new KraussMaffei injection molding machines, and retrofittable to most older machines. It enables the use of digital products, including socialProduction. Together, they capture, analyze and store data streams right at the machine in real time and provide regular updates to ensure the security of globally distributed devices.
OEMs also are responding to the challenges of processing certain materials, including liquid-silicone rubber, PET and PET-glycol (PET-G). LSR continues to grow in popularity for medical parts such as membranes and implants, OEM representatives said.
But, due to its extremely low viscosity, it’s challenging to process.
In October at its Engel live e-xperience, the company showcased a new LSR injection unit that follows a trend toward ever-smaller shot weights. Created in partnership with Fischlham, Austria-based ACH Solutions, which also supplied a quality-control camera cell and an LSR metering pump, the injection unit delivered shots for precision ophthalmic parts weighing 0.0013 gram each. It ran on an all-electric, tie-bar-less e-motion 50/30 TL IMM.
“Due to its outstanding properties and very good biocompatibility, LSR is becoming increasingly established for medical applications in general,” said Christoph Lhota, VP of the medical division of Engel Austria GmbH in Schwertberg.
Within the medical industry, micro technology and LSR loom large.
“Medical technology is currently the biggest driver for the further development of microtechnology,” Lhota said. “Applications exist, for example, for ophthalmology and increasingly in the field of microfluidics for point-of-care diagnostics.”
LSR isn’t the only challenging material.
Husky has set its sights on PET and PET-G with its development of a new blood-collection-tube production system, due out later this year.
“This is what we would say is the first integrated injection molding system for a medical application,” said Thomas Bontempi, head of medical business development at Husky. “In the medical space today, you normally find a supplier of hot runners, a supplier of the mold and a supplier of a machine. Customers used to put these pieces together, but this is what we believe is a suboptimal solution because there are always boundaries, and the pain comes at the boundaries.”
In addition, to help medical molders and molders of other particularly demanding parts, Husky recently introduced its UltraShot injection system, which combines injection with hot-runner functions. The new system brings the injection point as close to the mold cavity as possible, making possible previously unmoldable parts, Bontempi said. For example, parts that used to require assembly can now be molded as a single piece.
Bruce Geiselman, senior staff reporter
Contact:
Engel Machinery Inc., York, Pa., 519-725-8488, www.engelglobal.com
Husky Injection Molding Systems Ltd., Bolton, Ontario, 905-951-5000, www.husky.ca/en
Krauss-Maffei Corp., Florence, Ky., 859-283-0200, www.kraussmaffei.com
More on medical parts and plastics
Parts makers step up their processes to meet needs
Health-care market keeps IMM makers busy
Extruder OEMs respond to changing medical landscape
Auxiliary makers prioritized medical orders during pandemic
Robots shine in clean room duties
Economist: Run on medical goods provided jolt to plastics manufacturers
University speedily designs and prints nasal swabs
Geisinger’s 3-D lab printed devices to help health care workers stay safe
Beckwood Press designs compression molding equipment for medical devices
Quick deliveries, new products: Husky details COVID-19 response
Bruce Geiselman
Senior Staff Reporter Bruce Geiselman covers extrusion, blow molding, additive manufacturing, automation and end markets including automotive and packaging. He also writes features, including In Other Words and Problem Solved, for Plastics Machinery & Manufacturing, Plastics Recycling and The Journal of Blow Molding. He has extensive experience in daily and magazine journalism.
Karen Hanna | Senior Staff Reporter
Senior Staff Reporter Karen Hanna covers injection molding, molds and tooling, processors, workforce and other topics, and writes features including In Other Words and Problem Solved for Plastics Machinery & Manufacturing, Plastics Recycling and The Journal of Blow Molding. She has more than 15 years of experience in daily and magazine journalism.
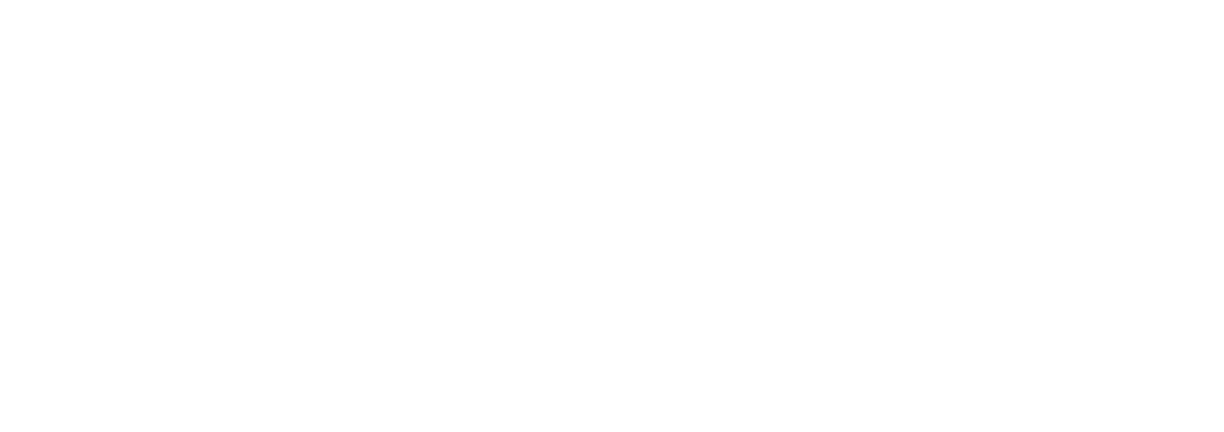