Beckwood Press designs compression molding equipment for manufacturing medical devices
PMM Staff Report
Beckwood Press Co., a St. Louis-based manufacturer of custom hydraulic and servo-electric presses, recently was awarded a contract to build two custom hydraulic presses for WHK BioSystems, a contract manufacturer of medical device components.
One press will be a 110-ton, four-post compression molding machine designed for research and development. The press will include 12-inch-by-12-inch heated platens with a bed shuttle and a heated mold.
The other machine will be a 1,650-ton compression molding press for producing UHMW (ultra-high-molecular-weight) PE sheets, with heated platens measuring 3 feet by 5 feet. UHMWPE is a tough, abrasion-resistant, low-cost plastic with applications in smaller medical devices and implants. Both machines will feature hot oil heating systems with temperature capacities up to 500 degrees Fahrenheit and temperature tolerances to within plus or minus 5 degrees, according to a Beckwood press release.
The presses will include Beckwood’s proprietary PressLink remote support module, which uses an internet connection to remotely connect Beckwood technicians with presses in the field for troubleshooting. If a customer’s press starts operating outside of predetermined parameters, a Beckwood specialist can begin troubleshooting within minutes, according to the company.
“Over the last five years, we’ve seen a dramatic increase in demand for machinery to produce UHMW as its use expanded into the medical, aerospace and defense sectors,” said Caleb Dixon, sales engineer at Beckwood, in a press release. “In response to this need, Beckwood has developed multiple press systems that are optimal for manufacturing UHMW sheets.”
WHK BioSystems, headquartered in Clearwater, Fla., is an FDA-registered facility that manufactures medical devices and components in ISO Class 7 clean rooms.
“In order to mitigate lead times and contamination risks associated with the implant materials supply chain, we made the decision to bring UHMW sheet manufacturing in-house with our own Class 7 clean-room environment,” said Robert Klingel Jr., WHK BioSystems president, in a statement. “With so few manufacturers capable of creating UHMW components for implantable medical devices, we saw this as an opportunity to add to our list of growing capabilities for the medical and life science communities.”
Contact:
Beckwood Press Co., St. Louis, 636-343-4100, www.beckwoodpress.com
More on medical parts and plastics
Parts makers step up their processes to meet needs
Health-care market keeps IMM makers busy
Injection unit, machine dedicated for test tubes among new processing technologies
Extruder OEMs respond to changing medical landscape
Auxiliary makers prioritized medical orders during pandemic
Robots shine in clean room duties
Economist: Run on medical goods provided jolt to plastics manufacturers
University speedily designs and prints nasal swabs
Geisinger’s 3-D lab printed devices to help health care workers stay safe
Quick deliveries, new products: Husky details COVID-19 response
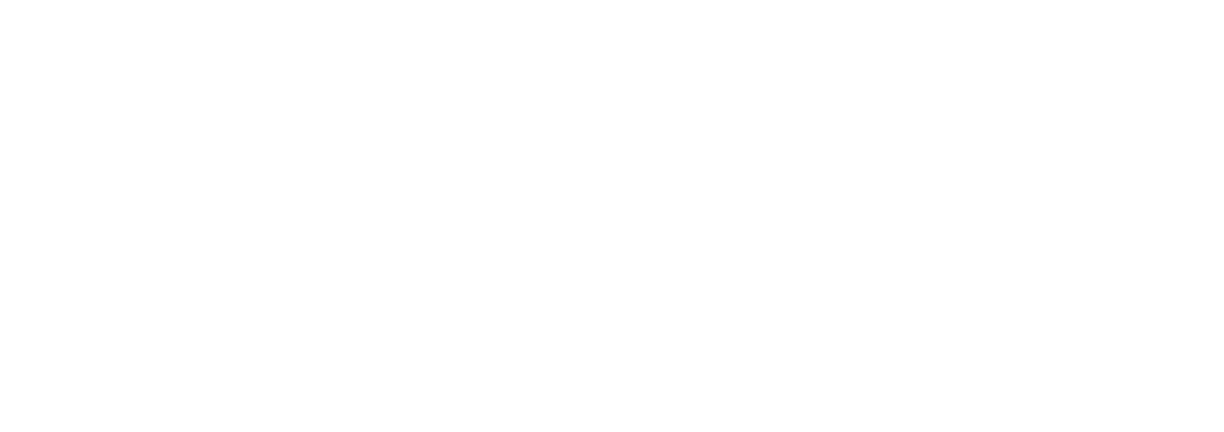