By Karen Hanna and Kathy Hayes
Robots spend no time planning their next vacation, and they don’t get sick. For manufacturers serving the medical market, the advantages of automation have never been more obvious. Robot OEMs have risen to the occasion with new and upgraded products tailored to clean rooms.
Fanuc: Robots building more robots
In a year defined by the COVID-19 crisis, robots have offered workaday predictability, a fact that has driven demand, as well as insulated production schedules for OEM Fanuc, where robots labor uninterrupted building the next generation.
“We have our own machines and robots and other automation building all of our product line, all the way from the motors in the servo motors that drive our products to motion controllers that run motors to the robot arms themselves. The machining operations, the assembly operation, we have robots,” said Dick Motley, director for Fanuc America’s authorized system integrator network.
With 10 robots for every human employed at Fanuc’s manufacturing facility at the foot of Mount Fuji, the Japanese company can churn out 1,000 robots a month. The pandemic has kept them busy, with robust demand for automation, including Fanuc’s latest innovations: the 22-pound-payload CRX cobots, released about a year ago; and clean-room-ready versions of the SR-12iA SCARA robot, which has a reach of about 3 feet and a payload of about 26.5 pounds, and the SR-20iA, which has capacities of about 3.6 feet and 44 pounds.
Both new SCARA robots feature a white epoxy coating, bellows covers, anti-rust bolts and seals, and an IP65 rating guaranteeing protection against dust and liquids.
“We’re always adding to that product line,” Motley said. “We just introduced it as an environmental option for our latest SCARA product. … That’s a class of robot arm that is ideally suited to work at high speed. It’s a relatively simple mechanism that can operate at high speed, very cost-effective, has to be very precise. And we just continued our tradition of adapting products for specialty environments like clean rooms and medical.”
Among health-care-parts manufacturers, cobots and vision systems have proved especially popular, Motley said. With them, manufacturers can speed up or increase production, achieve greater precision and spread out their workforce, in accordance with physical-distancing requirements.
“A lot of times, there’s a level of precision that is difficult to achieve with a manual operation. There are expectations of traceability that are much more robust, when it’s an automated process, and the pedigree of the product is documented through an automated process,” he said.
Kim Norris, senior marketing coordinator for ESS Technologies, a systems integrator that works with Fanuc, said her company has seen interest in robots among manufacturers of products used to combat COVID-19.
“We’ve designed automated test-kit-assembly systems that use robotics to assemble test tubes fitted with swabs and reagents, as well as filling and plugging test kit vials,” Norris said.
Fanuc robots and cobots can perform a host of upstream and downstream activities, including labeling, trimming, de-gating and packaging operations.
“Robots have been doing those kind of operations right around the press for a long time, and they’ve also been involved in the assembly of medical devices and anything from inhalers to respirators ... and various diagnostic kits and so forth, kitting those together,” Motley said.
At a lower cost than robots, cobots have allowed manufacturers to adopt automation quickly. Unlike robots, they don’t need a lot of space or guarding, and they can adapt to a variety of tasks.
“That was the silver bullet for a lot of our customers, as well, where they needed to respond to reduced staffing, but they couldn’t afford to put up large automation systems that claimed a lot of space, and so being able to place cobots was a big advantage,” Motley said.
Vision systems open even more possibilities.
“One of the things that is a really powerful enabling technology is machine vision,” he said. “Basically, when you connect a vision camera to a robot, you have a robot that can see, and that becomes really important in [making] medical devices for in-process validation, ‘do I have the right part?’ It can read a bar code to verify which part it is. … It also has some benefits in terms of product changeover where the robot can see what it’s working on. There’s less need to fix it in place with fixtures or dedicated types of tooling and those kinds of things … the robot can adapt based on its vision capability.”
Motley refers to the drivers behind automation as the dreaded D’s — dirt, danger, dullness and difficulty. The pandemic, with its pressures on both the labor force and essential supplies, has accelerated automation adoption.
In addition to being able to perform some tasks more accurately and consistently than humans, robots can reduce the risk of contamination, both from humans spreading germs, and from potent drugs that could potentially hurt workers. That could make the workplace safer — and reduce the cost of protective clothing, said Walter Langosch, global business development for ESS.
Motley’s dreaded D’s are also top-of-mind for ESS.
“One of the biggest challenges our customers have seen over the last year is finding and keeping personnel willing and capable to perform the repeatable action of loading and unloading product,” said Matt Kentfield, Southeast regional sales manager for ESS. “In many cases, integrating an automated solution can help to create jobs by reshoring more manufacturing work. Robots protect workers from repetitive, mundane and dangerous tasks, while also creating more desirable jobs, such as engineering, programming, management and equipment maintenance.”
Motley predicts some of the changes are here to stay.
“Yeah, for sure, there’s just a distinct shift triggered by COVID, where not only were there needs, higher demand for certain types of products … just massive demand that our customers were struggling to meet and they needed to be able to automate to be able to achieve that. You combine that spike in demand with the challenges of social distancing, and that really added up to some urgent needs on the part of our customers to implement robotics and other forms of automation to be able to deal with that one-two punch,” he said.
Sepro: New MED line made for clean rooms
Sepro is targeting injection molding clean rooms serving the medical and pharmaceutical industries with a new line of three-, five- and six-axis robots.
The MED-series robots include design and operational features that ensure clean operation, precision and productivity.
“Sepro robots increase productivity and enhance workflows,” said Claude Bernard, product marketing director. “Within the clean-room market, our robots can be used across the entire production line — from assembly to inspection, traceability and packaging.”
MED-series robots use FDA-approved lubricants on all linear guiding surfaces and gears; locations where lubricants are used are enclosed so they cannot contaminate the molding area.
Components, such as end-of-arm-tooling (EOAT), that contact the molded parts are protected against corrosion as standard. Depending on the requirements of a particular clean room, the EOAT can be made from clean materials such as anodized aluminum, stainless steel or polyoxymethylene, according to the company.
All MED-series robots can be equipped with pneumatic filtration as fine as 0.3 micron; 5-micron filtration is standard to protect the robot’s pneumatic actuators from particles.
The three-axis robots — designated 3 15 MED, 3 25 MED and 3 35 MED — have maximum payloads ranging from 11 to 44 pounds and can serve injection molding machines with clamping forces ranging from 30 to 800 tons.
There are two types of five-axis robots in the series, each available in three sizes. The 5X MED robots have a two-axis servo wrist for five numerically controlled axes of motion. The S5 Line MED robots have three servo-driven axes and a pneumatic wrist. Like the three-axis robots, their payloads range from 11 to 44 pounds, and they are appropriate for IMMs ranging from 30 to 800 tons. They can be installed in transverse or axial layouts.
Sepro collaborated with Stäubli Robotics to create the MED-series six-axis servo articulated-arm robots, which can serve molding machines with clamping forces ranging from 20 to 1,300 tons. Available in four sizes — designated 6X-60 MED, 6X-90 MED, 6X-160 MED and 6X-200 MED — each robot consists of a standard Stäubli arm that is certified for use in Class 100 clean rooms. The robots feature smooth, white surfaces for easy cleaning and can be mounted on the floor or ceiling.
Vital statistics: Sepro three-axis and five-axis models (axes denoted by the first number in the model name)
3 15 MED S5 15 MED 5X 15 MED | 3 25 MED S5 25 MED 5X 25 MED | 3 35 MED S5 35 MED 5X 35 MED | |
Horizontal (X-axis) stroke range (feet) | 4.9 to 13.1 | 4.9 to 19.7 | 6.6 to 29.5 |
Demolding (Y-axis) stroke (feet) | 1.7 | 2.3 | 2.9 |
Vertical (Z-axis) stroke (feet) | 3.3 (direct arm) | 4.6 (telescopic arm) | 5.9 (telescopic arm) |
Vital statistics: Sepro six-axis models
6X-60 MED | 6X-90 MED | 6X-160 MED | 6X-200 MED | |
Reach (feet) | 2.2 | 3.9 | 5.6 | 7.2 |
Long-arm-version reach (feet) | 3 | 4.8 | 6.6 | 8.5 |
Payload (pounds) | 7.7 | 13.2 | 44 | 220 |
Long-arm-version payload (pounds) | 4.4 | 11 | 30.8 | 132 |
ABB: Six-axis robots can lift heavy, complex loads
ABB’s IRB 1300 six-axis industrial robot, launched in September, now comes in an ISO 4 clean-room version that is appropriate for use in plastics facilities serving the medical and pharmaceutical industries. The company also introduced a version with IP67-rated seals to protect it from dust and water.
The company designed the IRB 1300 to meet customer demand for a fast, compact robot that can lift heavy objects or loads with complex and irregular shapes.
The clean-room model includes new features that enable it to be used in contamination-free production processes. For example, it is coated in chemical-resistant paint that doesn’t degrade when exposed to antibacterial cleaning agents.
Additionally, the robot’s design minimizes the number of gaps where bacteria could form. It has a particle filter and is fully sealed to prevent grease, oil and particles from contacting the products it handles.
“The IRB 1300 is the perfect partner for a wide variety of tasks, including materials handling, machine tending, polishing, and assembly and testing, and can now help more businesses achieve new standards of speed and accuracy as they develop solutions to lift and handle heavy, complex or irregular shapes, even in small workspaces,” said Darren Hung, ABB’s global product manager for small robots.
Specifically for clean-room plastics processing, the IRB 1300 is suited for tending injection molding machines and for handling post-processing steps such as parts degating, handling, assembly and packaging, a company spokesman said.
The IRB 1300 is appropriate for use in confined spaces, with a footprint of 8.7 inches by 8.7 inches. It comes in three sizes: a model with a payload of 24.3 pounds and a reach of 2.3 feet; one with a payload of 22 pounds and a reach of 3.8 feet; and one with a payload of 15.4 pounds and a reach of 4.6 feet.
The robot’s OmniCore controller provides advanced motion control and best-in-class path accuracy, and can accommodate optional equipment such as vision solutions, force control and fieldbus protocols, the company said. The FlexPendant interface operates via the pinch, swipe and tap gestures used by smartphones, simplifying programming and operation.
Stäubli: TX2 cobot line grows
Stäubli has expanded its TX2 generation of six-axis collaborative robots by adding three cobots in the medium-payload range; they come in several versions tailored to specific environments, including a clean-room version.
“Our newly extended TX2 series offers added advantages of superior throughput capabilities and reliability, a higher load capacity, increased stiffness and higher dynamics, allowing for shorter cycle times, said Sebastien Schmitt, Robotics Division Manger, Stäubli North America. “Our fully encapsulated robot design is compatible for even the most challenging cleanliness requirements in medical plastic parts production.”
The TX2-140, TX2-160 and TX2-160L cobots join six other models in the TX2 line and are suitable for a wide variety of tasks. They feature a compact, streamlined design; a rigid structure; repeatability of plus or minus 0.05mm; and fast speeds.
The clean-room cobots have glossy surfaces and media and supply lines that run inside a housing that is sealed against dust and liquid to the IP 65 standard.
The TX2-140 has a reach of almost 5 feet, and the TX2-160 has a reach of 5.6 feet; both have a load capacity of 88.2 pounds. The TX2-160L — the long-arm version of the TX2-160 — has a reach of 6.6 feet and a load capacity of 55 pounds.
All of the company’s six-axis cobots use the same CS9 controller, which facilitates the use of multiple robots in digitally networked production environments. They are Industry 4.0-compatible. Safety features include a digital safety encoder on each axis and an integrated safety printed circuit board.
Contact:
ABB Robotics, Auburn Hills, Mich., 248-391-9000, www.abb.com/robotics
ESS Technologies Inc., Blacksburg, Va., 540-961-5716, www.esstechnologies.com
Fanuc America Corp., Rochester Hills, Mich., 888-326-8287, www.fanucamerica.com
Sepro America LLC, Warrendale, Pa., 412-459-0450, www.sepro-america.com
Stäubli Corp., Duncan, S.C., 864-486-5421, www.staubli.com
More on medical parts and plastics
Parts makers step up their processes to meet needs
Health-care market keeps IMM makers busy
Injection unit, machine dedicated for test tubes among new processing technologies
Extruder OEMs respond to changing medical landscape
Auxiliary makers prioritized medical orders during pandemic
Economist: Run on medical goods provided jolt to plastics manufacturers
University speedily designs and prints nasal swabs
Geisinger’s 3-D lab printed devices to help health care workers stay safe
Beckwood Press designs compression molding equipment for medical devices
Quick deliveries, new products: Husky details COVID-19 response
Karen Hanna | Senior Staff Reporter
Senior Staff Reporter Karen Hanna covers injection molding, molds and tooling, processors, workforce and other topics, and writes features including In Other Words and Problem Solved for Plastics Machinery & Manufacturing, Plastics Recycling and The Journal of Blow Molding. She has more than 15 years of experience in daily and magazine journalism.
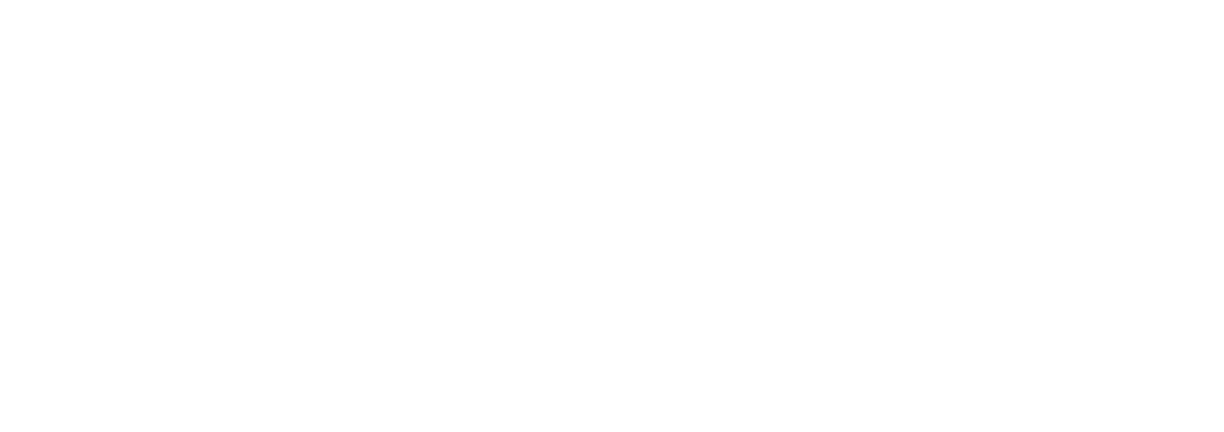