By Bruce Geiselman
Husky, which manufactures injection molding machines, hot runners and molds, is responding to meet the changing needs of its customers producing medical and diagnostic equipment, according to the company.
Over the challenging past year, Husky has arranged for quick deliveries, especially for urgent and mission-critical medical applications.
Husky also is introducing new products to address the changing needs of the medical market, said Thomas Bontempi, head of business development for medical business at Husky.
The company expects to launch in the second half of this year a new system for producing PET and PET-glycol (PETG) blood-collection tubes. The system, which will hit a market that’s experiencing demand for the collection tubes, will include an injection molding machine, hot runner and mold.
“This is what we would say is the first integrated injection molding system for a medical application,” Bontempi said. “In the medical space today, you normally find a supplier of hot runners, a supplier of the mold and a supplier of a machine. Customers used to put these pieces together, but this is what we believe is a suboptimal solution because there are always boundaries, and the pain comes at the boundaries.”
With the ability to supply all components, Husky can create a system that is optimized for producing collection tubes.
Husky also recently introduced its UltraShot Injection System, which combines hot runner and injection functions. The technology brings the injection point as close to the mold cavity as possible, according to the company.
Typical design rules for injection molding do not apply with the UltraShot Injection System, according to the company.
“For us, that means giving customers in the medical space the ability to mold what previously we considered unmoldable while also providing major advantages for scaling up fast or reducing the time to market,” Bontempi said.
For example, parts that used to require assembly can now be molded as a single part.
UltraShot Injection Technology produces pressure near the cavity with a precise, servo-controlled injection system that provides what the company calls unmatched control of cavity filling and balance for critical parts and challenging applications.
One benefit of the system is that parts that used to require post-mold assembly can now be produced in a single cycle at higher cavitations.
Compared with conventional hot runners, melt in the UltraShot system experiences fewer high-pressure injection cycles, preserving the original resin properties. That can result in better physical properties for molded parts, according to the company.
COVID-19’s impact on sales
While the pandemic had a devastating impact on many businesses worldwide, Husky experienced increased demand for some medical equipment in certain markets over the past year, Bontempi said.
“There has been an increase in sales in an aggregated way with certain markets more active than others,” Bontempi said.
In some markets, where economies virtually shut down due to the pandemic, Husky saw a decrease in sales. But in other markets, like the United States, which saw its economy temporarily slow down but then quickly mount a rebound, Husky saw stronger sales, Bontempi said.
Husky also experienced a change in demand for the types of equipment it sold.
“The mix of product is slightly changed because of the COVID impact,” Bontempi said. “COVID-driven laboratory applications have been high, even with constraints in the supply chain.”
Along with blood-collection tubes, demand for pipette tips, prefilled syringes and the equipment to produce them has been high. Prefilled syringes, which ensure the administration of proper dosages, are frequently used when distributing COVID-19 vaccines. The syringes minimize the waste that can occur with other vials, where a small amount of vaccine can remain, unused, after administration. To extend the shelf life of the vaccine, prefilled syringes require an oxygen barrier.
For OEMs like Husky, a trend in the West favoring the use of plastic syringes over glass syringes, which are breakable and temperature-sensitive, also is driving demand.
Shortage of raw materials
Husky’s medical customers, like other plastics processors, have dealt with resin shortages during the pandemic.
“Everything has contracted,” Bontempi said. “Supply chains have been cut in the midst of the pandemic. … We hear of some shortages, but it's not the same for all the materials. I heard about polypropylene being constrained, but I haven't seen the same for PET, for example.”
Raw material shortages have led to higher prices. “We see this as a challenge, but we see it also as an opportunity,” he said.
Since Husky manufactures not only individual injection molding machines but also hot runners and molds, it has many opportunities to optimize the processing of plastics and help its customers reduce their consumption of material through lightweighting.
In addition, Husky can help customers adapt to processing different materials that might have a lower cost.
“Normally, they are produced in PETG, which is basically a variation of PET, but it has almost three times the price of basic PET,” Bontempi said. “If you're able to develop the system that has the capability to process standard PET, or let's say a PET that has a higher viscosity level because it's all related to the viscosity, basically you can save on the material, which is normally 90 percent of your production costs on a PET application. … We believe we have the basics to provide to the market some good solutions and alternatives.”
Localized production trends
The COVID-19 pandemic disrupted local supply chains, creating localized shortages in supplies of some medical components and supplies. The shortages have made the health-care and pharmaceutical industries and local governments aware of risks that could be posed during future pandemics.
“What happened is now, many governments around the world are aware that they rely heavily on imports,” Bontempi said. “We see a trend, or at least we see strong signals in the market, of more localized production.”
Local governments want to minimize the risk of future supply-chain disruptions by incentivizing local production.
Bontempi said he isn’t sure if manufacturers with centralized facilities will react to these concerns by decentralizing their production or if newcomers will enter into the market to provide localized production. Regardless, Husky is prepared to help meet demands for new equipment and tooling.
“This dynamic, we see it happening,” Bontempi said. “We think we are in a good position through our global network and presence to support any dynamic that moves forward.”
Bruce Geiselman, senior staff reporter
Contact:
Husky Injection Molding Systems Ltd., Bolton, Ontario, 905-951-5000, www.husky.ca/en
More on medical parts and plastics
Parts makers step up their processes to meet needs
Health-care market keeps IMM makers busy
Injection unit, machine dedicated for test tubes among new processing technologies
Extruder OEMs respond to changing medical landscape
Auxiliary makers prioritized medical orders during pandemic
Robots shine in clean room duties
Economist: Run on medical goods provided jolt to plastics manufacturers
University speedily designs and prints nasal swabs
Geisinger’s 3-D lab printed devices to help health care workers stay safe
Beckwood Press designs compression molding equipment for medical devices
Bruce Geiselman
Senior Staff Reporter Bruce Geiselman covers extrusion, blow molding, additive manufacturing, automation and end markets including automotive and packaging. He also writes features, including In Other Words and Problem Solved, for Plastics Machinery & Manufacturing, Plastics Recycling and The Journal of Blow Molding. He has extensive experience in daily and magazine journalism.
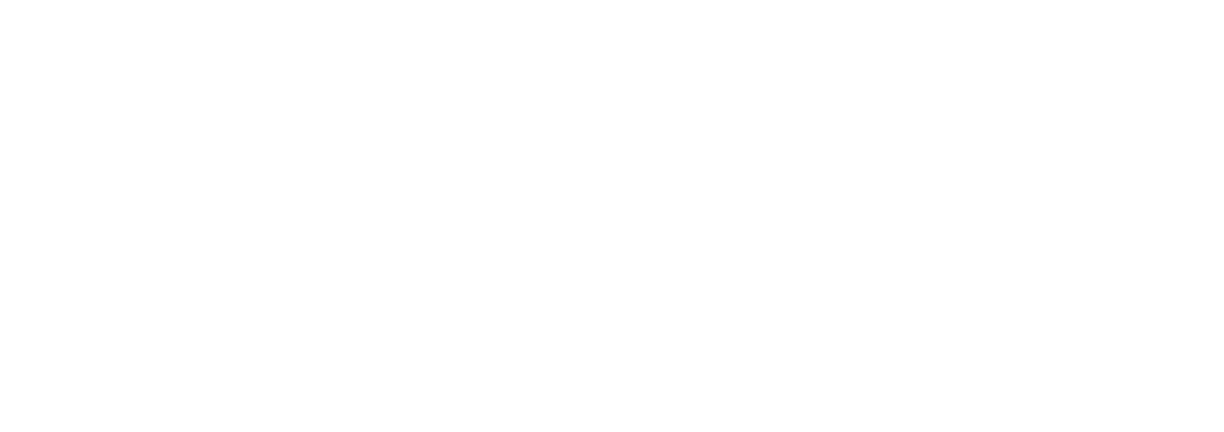