Customer feedback drives Maguire’s innovations
By Lynne Sherwin and David Tillett
Every product has a story behind it, according to Frank Kavanagh, VP of sales and marketing for auxiliary equipment maker Maguire.
“As you get products out in the field, and customers are using them, they give us feedback,” he said. “We're finding ways of learning, ‘OK, this is what they need now,’ and ‘This is what's going to help here,’ and ‘Here's how we're going to do that.’ We’re trying to improve upon them and make them more user-friendly.”
For Maguire, improvements driven by customer feedback can take many forms. This could involve scaling down advanced technology to handle smaller capacities—such as with the company’s specialty blenders—or combining a feeder and blender into a single unit. It could also involve services like empowering customers to handle routine maintenance or offering total equipment refurbishment.
Customization has become increasingly critical as processors incorporate more recycled resins, fillers, and other components into their processes. While Maguire offers over 150 off-the-shelf blender configurations, many customers require custom solutions.
“Customers are being mandated to add more PCRs [post-consumer recycled materials] and other components. Instead of a standard four, five, or six-component blender, you’re now seeing configurations with many more components,” Kavanagh said.
Maguire’s modular approach allows processors to start with a base blender and add hoppers or dispensing devices as applications evolve.
“It's a little more custom than the cookie-cutter approach of the past,” Kavanagh said, emphasizing the importance of meeting the growing demand for equipment that handles multiple major and minor components effectively.
At NPE2024, the company showed off its WSB 600 weigh-scale blender, which debuted at K2022. It’s the smallest so far in Maguire’s specialty blender line and can dispense up to 12 components, including pellets, powder, liquid, regrind, and poor-flowing materials such as wood flour.
Another piece of featured equipment in the NPE booth, the new Fusion, was designed to meet demand for quick material changeovers. It combines a weigh scale blender and a gravimetric feeder with a single integrated controller.
“When you're running additives through a blender, a material or color change requires cleaning the entire blender,” Kavanagh said. “With the Fusion, gravimetric feeders can be mounted on the feed throat of the processing machine, allowing primary materials to run through the blender while additives are dosed gravimetrically below. This setup significantly reduces additive clean-out time.”
Maguire also introduced Tracker, a web-based monitoring and control solution. Tracker integrates with Maguire’s WSB blenders, MGF feeders, ULTRA dryers, and FlexBus conveying systems, providing processors with centralized operational oversight and control.
Kavanagh said the company’s booth at NPE was busy, drawing a “very diverse group” of processors, many from the packaging and automotive fields, along with building and construction, household goods, medical and agricultural industries.
“I'd say 40 percent of our leads were from new customers. ... So, in that regard, we're pretty happy with the show,” he said.
While the company reported higher sales in 2024 compared to 2023, it had not yet observed a post-NPE sales surge by October. However, Kavanagh noted, “Quote activity is extremely high.”
Maguire’s MOU Program provides customers with tools and resources to maximize the lifespan and value of their equipment. Like many other equipment makers, Maguire is leaning into customer aftercare with its MOU Program.
Under the program, processors can access resources such as part libraries, exploded views, and calibration and maintenance checklists to keep their equipment running optimally, especially during the five-year warranty period.
“We want to provide the tools to allow our customers to really maximize the value of their investment and help them become masters of their blending,” Kavanagh said, echoing Maguire’s “Masters of Blending” advertising campaign.
For equipment requiring professional attention, the MOU Program offers assessments, upgrades, and refurbishments. Customers can send equipment to Maguire for repairs, or upgrades like new controllers. (The latest 4088 touch screen controller is backward-compatible with older models), or higher temperature capabilities, and even complete refurbishments.
“Sometimes, it’s equipment that has been running for 15 to 20 years,” Kavanagh said. “We clean it, refurbish it with new airlines and slide gates, upgrade the controller, and send it back. They’ve essentially got a brand-new blender for a third of the price, potentially extending its life by another 10 to 15 years.”
Maguire also offers a trade-in program, “but often, when our customers send us the units for refurbishment, they want them back. They're not looking to get rid of them. They still see the value in the unit,” Kavanagh said.
“There's 70,000 Maguire blenders installed out there in the world,” he said. “They've stood the test of time.”
Contact:
Maguire, Aston, Pa., 610-459-4300, www.maguire.com
Lynne Sherwin | Managing Editor
Managing editor Lynne Sherwin handles day-to-day operations and coordinates production of Plastics Machinery & Manufacturing’s print magazine, website and social media presence, as well as Plastics Recycling and The Journal of Blow Molding. She also writes features, including the annual machinery buying survey. She has more than 30 years of experience in daily and magazine journalism.
David Tillett
Associate Editor David Tillett writes and edits for Plastics Machinery & Manufacturing, Plastics Recycling and The Journal of Blow Molding. He covers new products, industry news, patents and consumer and business equipment. He has more than 20 years of experience in daily newspaper, online and magazine journalism.
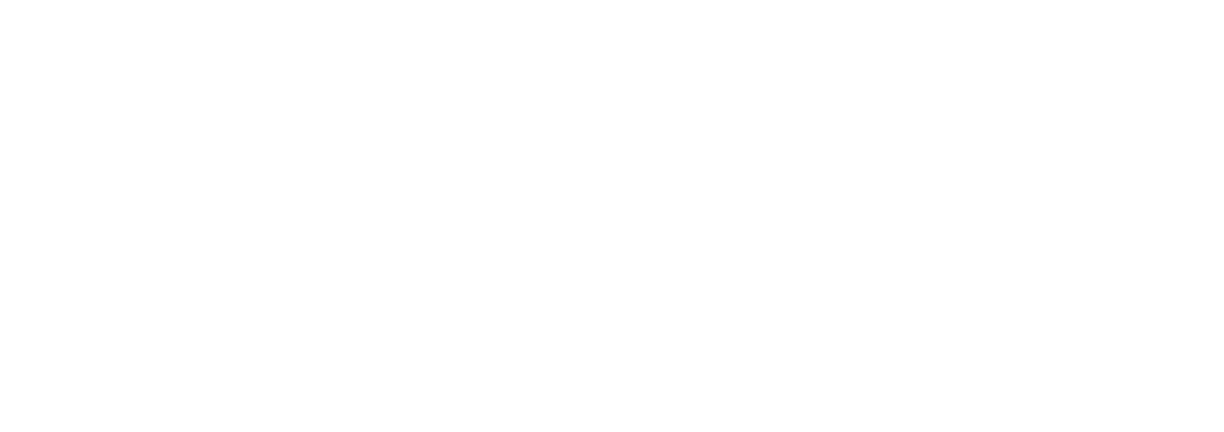