By Ron Shinn
Having the latest option on a new injection molding machine might make you feel good when writing the check, but the next question should be how easily it communicates with the auxiliary equipment. That’s where money is on the line.
Seamless data exchange between every component in a work cell is a feature Austria’s Wittmann Group takes for granted because it has been offering it for more than 10 years. Wittmann builds molding machines and just about everything that connects to them.
“Connectivity is what goes beyond being a machinery manufacturer,” said Jason Long, VP of sales at Wittmann USA in Torrington, Conn. “We control all the engineering in the background. We have the robot and the TCU and everything else communicating with the molding machine. If you buy the same equipment from multiple vendors, you end up with competitors talking to competitors to try to make the process work.”
Plant floor operations are changing and the days of cobbling together equipment from a hodgepodge of vendors are slowly coming to an end.
“We see it over and over again,”said Sonny Morneault, who this spring was named president of Wittmann USA. “The resources at our customers have been dwindling over recent years. Now, we might see one maintenance guy for 50 machines. That was unheard of back in the day when you’d have five guys to handle that many machines.
“All of us struggle with finding talent and resources,” Morneault said in a recent interview. “So we are able to provide some of those resources with the seamless integration of what we call plug and produce. We just use an Ethernet connection. There is no one else in the industry that can do that.”
How it all began
The Wittmann company was founded in Vienna in 1976 by Werner Wittmann,, who saw a need for a better water flow regulator when he was working for Engel. His first manufacturing facility was his garage and his workforce consisted of his two sons, Michael and Thomas. Michael is now president of the Wittmann Global Group, and Thomas is managing director of the company’s expanding operations in Hungary.
Three years later, Werner Wittmann was building temperature control units, and in 1985, he started manufacturing CNC robots.
Wittmann USA was launched in 1989 as the company continued to acquire and develop new product lines and spread across the globe.
Wittmann took over the struggling Battenfeld injection molding machinery company in 2008 and since has focused on integrating its full line of molding machines, automation and auxiliary products.
The Wittmann Group, with 10 production facilities in six countries, had worldwide sales of about $427 million and USA sales of nearly $90 million in 2023, edging Germany for the first time to claim the top country in sales.
American-made robots
The mix of U.S. products sold in the U.S. varies from year to year, but Morneault said robots make up about 40 percent of sales, molding machines about 30 percent and materials-handling products about 30 percent.
In the U.S., Wittmann has 158 employees, with 120 located in the 145,000-square-foot Connecticut facility. Separate business units in Canada and Mexico serve those countries.
The company also has U.S. technical centers in South Elgin, Ill., and Placentia, Calif.
Unlike most of the other non-U.S. plastics machinery manufacturers that have a big presence in this country, Wittmann manufactures robots, one of its major products, in Torrington. Annual production capacity is about 500 robots. In addition to selling the U.S.-made robots, Witttmann sells some here that are built in Hungary and Austria.
In the U.S., Morneault said Sepro and Yushin are Wittmann’s biggest competitors for robots.
“We make robots for every size molding machine, from little micro-
powered up to 8,000-ton presses,” Long said.
Building the robots in the U.S. lets Wittmann offer extensive customization. “We have medical molders that run 32-cavity molds,” Long said. “They need cavity separation so we can offer 16 vacuum circuits.”
It takes about 40 man-hours to build a robot in Torrington.
Local manufacturing makes that customization possible, Long said. “A customer calls and says, ‘I need robots, and I need them to be this spec,’ ” he said. “Just about everything we do is special. That’s because the application is driving the U.S. market.”
Generally, about 35 standard robots are in stock for immediate shipment.
Multiple lines of IMMs
Wittmann manufactures three lines of all-electric molding machines, ranging from the MicroPower (16 tons of clamping force) and EcoPower (60 tons to 600 tons) to the EcoPower Xpress (175 tons to 600 tons).
There are six lines of servo-hydraulic machines. The SmartPower (30 tons to 450 tons) and MacroPower (450 tons to 2,500 tons) are Wittmann’s standard offerings. The rest of the line are specialized vertical machines: the CM series (45 tons to 90 tons), which is tie-bar-less; the VM (65 tons to 225 tons); the VM R (45 tons to 340 tons) with rotary table; and the VPower R (135 tons to 340 tons). The CM, VM and VM R machines can all be equipped with either vertical or horizontal injection units.
Since acquiring the Battenfeld press line in 2008, Wittmann has invested about $70 million in plant and manufacturing improvements. Morneault said all the machines except the VM and CM series have been totally redesigned from the original Battenfeld lines. “That includes the ergonomics, quality and serviceability,” he said.
Morneault said the Wittmann MicroPower is the leading micro-molding machine in the U.S. It is an all-in-one production cell that makes very precise parts. The company claims it produces 100 percent good parts.
The EcoPower line claims the best energy efficiency, lowest cycle times and very quiet operation.
The SmartPower servo-hydraulic machines are “incredibly energy-efficient and are the most repeatable and accurate molding machines in the industry,” Morneault said. Energy efficiency is the result of Wittmann’s patented kinetic energy-recovery system (KERS). SmartPower is technically flexible for multiple processes and applications.
The company switched its large-tonnage MacroPower line last year from a hydraulic to servo-hydraulic platform. “It is one of our top sellers,” Morneault said. “MacroPower and SmartPower machines are our most popular in the U.S. market.”
MacroPower machines are the most compact large-tonnage machines available, according to the company.
The EcoPower Xpress is high-speed with an all-electric platform and offers long service life at maximum utilization.
Multi-component molding has always been a strength for Wittmann machines in all sizes and tonnages. “Two-shot, three-shot, every configuration you can imagine,” Morneault said. “We will put a second or third injection unit wherever the customer needs it. We are very competitive in this market.”
Wittmann introduced the latest version of its B8X controller to the U.S. market at NPE. Built entirely in-house, it is the first control system for molding machines it has designed. Supply-chain shortages severely limited the number of controllers Wittmann could buy during the COVID pandemic. “To prevent it from ever happening again, Wittman developed a proprietary design we can manufacture in-house,” Morneault said. “We are no longer reliant on any other controller suppliers.
“It is the exact same software, and from the outside it looks and feels the same, but the software inside is now Wittmann,” Morneault said. That follows the same philosophy Wittmann adopted earlier for its robot controllers.
The previous controller was Wittmann’s Unilog B8.
All injection molding machines and components are built in Austria or Hungary. There are generally about 30 presses kept in the U.S. for quick delivery.
A range of auxiliary equipment
Wittmann has a wider range of auxiliary equipment than any other primary processing machinery manufacturer, and with one exception, it is all built in-house.
The lineup includes gravimetric and volumetric blenders, central conveying and drying systems, vacuum loaders, dryers, granulators, temperature control units, mold area protection and internal air cooling systems and water flow regulators. Only the gravimetric feeders are not built by Wittmann.
Wittmann builds an extensive line of granulators including G-Max blade and S-Max screenless units, as well as Minor under-the-press models. The Torrington plant is set up to test a customer’s material on different granulators, analyze the results and recommend the best type and size granulator for the application. “There is a huge technology backing to make sure the customer gets the right regrind,” Long said.
Plastics processors are showing more interest in buying complete molding cells instead of piecemeal equipment they have to assemble into a working cell. This plays into one of Wittmann’s major strengths.
Molding cells or molding machines with any additional Wittmann product are called multi-line projects. A project manager is assigned for these projects “and they work for the customer,” Morneault said. “Project managers are the ones who are integrating and coordinating shipments, timing installations, managing details of the installation and tracking service time and dollars.
“That is a big advantage for a customer who does not have in-house resources to do that,” Morneault said. He described a recent customer in the appliance industry who purchased multiple work cells. Wittmann supplied all the equipment, seamlessly integrated all the individual pieces and trained the customer’s staff.
Wittmann has 35 field service technicians in the U.S. and supplements that with four independent service providers. In the past, service technicians specialized in molding machines, robots or materials-handling equipment. They are currently being cross-trained to work on everything Wittmann sells.
“It’s more seamless for the customer,” Morneault said. “It is less time for the customer and saves us and him money.”
Web service is also available around the clock.
Smart technology links components
Wittman’s take on Industry 4.0 is called Wittmann 4.0. It consists of smart production components such as TEMI+, a modular MES that supports old and new Wittmann machine models and Wittmann 4.0 auxiliaries; the QuickLook 4.0 app, which provides a production status check via smartphone; HiQ packages to monitor material quality, control viscosity and active closure of a non-return valve; and Expert StepForce, which provides step-by-step clamping force build-up during injection.
Wittmann defines a smart work cell as one in which an injection molding machine has access to the capabilities and status of auxiliary units in order to make intelligent changes. This improves part quality and ensures the collection of traceability data.
With Wittmann 4.0, robots and auxiliaries can be plugged into the molding machine and automatically recognized by it. Their displays are also available on the molding machine control panel.
Product connectivity is key to Wittmann, and it has invested heavily in software engineers. “We have a really big software organization,” Morneault said. “To make all these products communicate and sync together and integrate seamlessly has been a humongous challenge, but we have been doing this for many years now.”
This is how it works: Everything in the work cell is central to the machine controller. The controller on the molding machine recognizes what is plugged in. It confirms the identity of the auxiliary, then it calls up that machine’s software, so the same software is on both it and on the auxiliary control. The two machines can then communicate seamlessly. It is not a virtual network computing (VNC) connection or shadow connection.
This process enables useful error messages. If the molding machine controller sees that the TCU needs to reach 200 degrees Fahrenheit and the TCU that is plugged in is capable of reaching only 150 degrees Fahrenheit, it blocks production and alerts the operator that another TCU is needed.
Manufacturers in North America have generally been slow to embrace smart factory concepts.
“Captive molders who run one job don’t really care much about the connectivity,” Morneault said. “They care about data acquisition, maybe. But if they are not changing molds very frequently, they don’t really care about how easy it is to connect and push data out to the entire work cell.
“The guys who are doing 10 mold changes a day per work cell care a lot about it because if you can save 5 minutes or 10 minutes per mold change, that’s money.”
The knowledge of workers in processing plants is also changing, which makes another good argument for Wittmann’s plug-and-produce approach. “There are 75 million baby boomers who are going to retire over the next 5 to 10 years,” Morneault said. “That creates a huge gap for the next generation. We are going to lose so much talent in our industry over the next five years.”
Wittmann specializes in building automation solutions for customers, and items such as bowl feeders, conveyors and vision systems generally run off the robot. “Our robots have so much power that 80 percent of our customers only use about 10 percent of the functionality of their robots,” Long said. “The robot control incorporates all these things. We don’t need separate PLCs and HDMIs.”
Long said being able to work through the robot controller saves money.
Worldwide, sales of injection molding machines are slow and Morneault said he does not see that improving much this year. But Wittmann’s wide range of products serves as a cushion during slow periods.
Contact:
Wittmann USA, Torrington, Conn., 860-496-9603, www.wittmann-group.com/en/usa
Ron Shinn | Editor
Editor Ron Shinn is a co-founder of Plastics Machinery & Manufacturing and has been covering the plastics industry for more than 35 years. He leads the editorial team, directs coverage and sets the editorial calendar. He also writes features, including the Talking Points column and On the Factory Floor, and covers recycling and sustainability for PMM and Plastics Recycling.
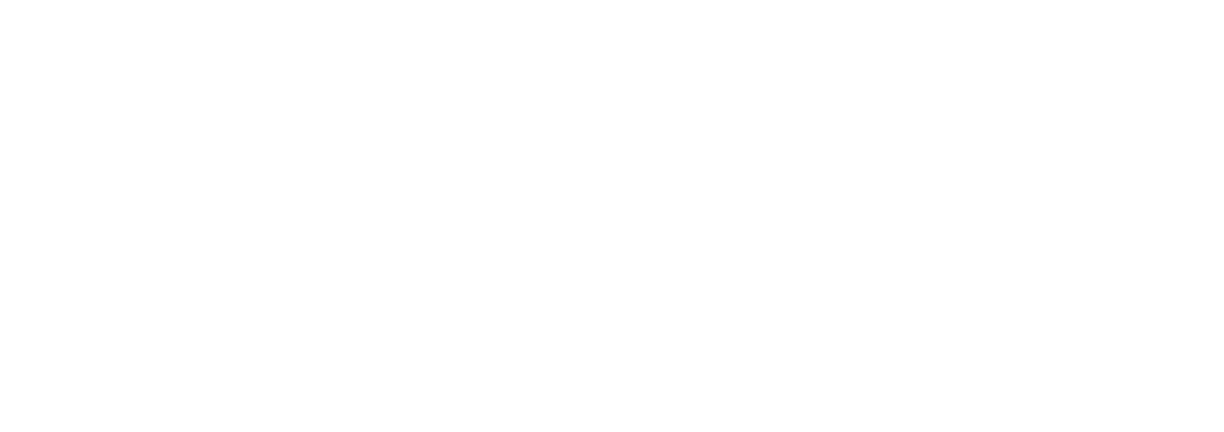