G-Max The compact granulators in Wittmann Battenfeld’s G-Max series were created for the closed-loop recycling of sprues, runners and defective parts from injection molding machines. They are appropriate for grinding soft to medium-hard plastics, such as PP, PE, ABS and PU, and can handle materials that are still warm from processing. They feature a rotor with open spaces between the rotating knives and the center of the shaft, which provides unrestricted airflow through the cutting chamber. Wittmann Battenfeld offers material screens with different sizes of perforations to accommodate a variety of materials and throughputs. A magnet is a standard feature to prevent the processing of metals.
What’s new? Upgrades to the G-Max 23 and G-Max 33 models that standardize their design based on the line’s smaller G-Max 13 model. The G-Max 23 and G-Max 33 models now come with larger hopper openings and a choice of fixed and rotatable versions of their material outlets. The G-Max 23’s cutting chamber measures 12.2 inches by 9.3 inches and its motor output is 3 kilowatts (kW). The G-Max 33 has a cutting chamber measuring 18.1 inches by 9.3 inches and a motor output of 4 kW.
Benefits Quiet, efficient operation and easier maintenance. The granulators’ tiltable material hoppers are simple to clean and service; screen changes can be carried out quickly, without tools.
Wittmann Battenfeld Inc., Torrington, Conn., 860-496-9603, www.wittmann-group.com
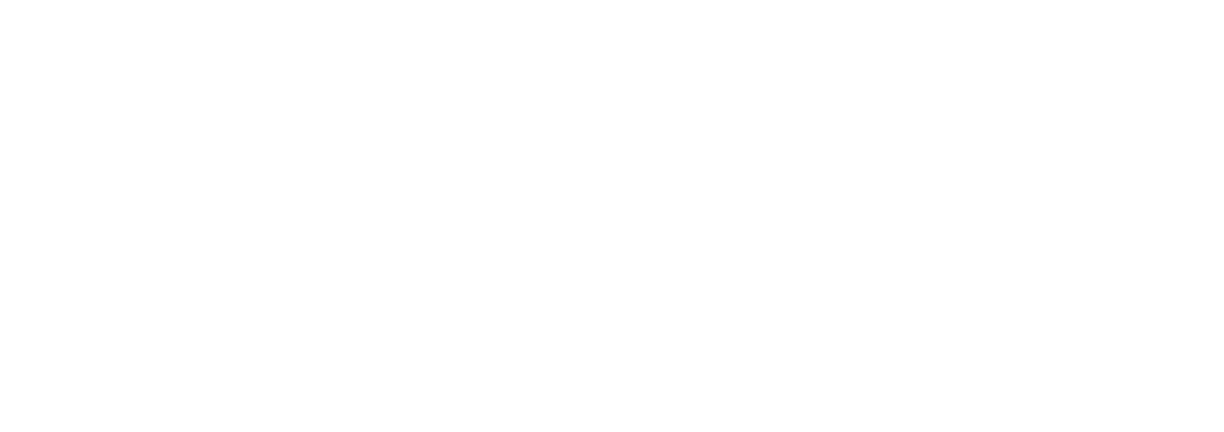