By Karen Hanna
As we enjoy the holiday season, let me make a confession: I am not lean.
But, no, I’m not talking about my cookie consumption habits.
Instead, my problems are deeper. I lose things, break things, buy things to replace things that mysteriously reappear months later on the kitchen table. I am scattershot and clumsy, with the attention span of a squirrel. As my mom would say, I am the reason I can’t have nice things.
This is no way to run a household, or worse, a manufacturing plant. But according to some sources, up to 90 percent of all manufacturing activity is devoted to tasks that add no value.
In other words, you're chasing your tail.
You could be like me, standing in the aisle of a big box store last month contemplating drill speeds and sizes to complete a project that, it turned out, required no drill. Cost of the drill: About 90 bucks. Time spent pondering all the options: About 30 minutes.
Realizing the old drill was in the basement all along: Priceless.
All that wasted time and cash add up.
The good news is, if you're in a situation like this, improvement is in reach. You already know you have a problem.
Maybe your employees are wasting precious minutes trekking across the plant floor to retrieve a tool that should live at the machine where it’s frequently required. Or a less-experienced worker is killing time waiting for a more-senior colleague to explain a procedure or troubleshoot a process. Maybe you can’t find a mold.
Peyton ”Chip” Owen, president and CEO of D&M Plastics, has some advice. Eleven years into his Burlington, Ill., molding shop’s lean journey, he thinks about lean 24/7.
“I want the people at my company to be asking themselves every single day, ‘How can I take 2 seconds out of everything I do?’ ” he said.
At his shop, all employees meet for a short huddle at the beginning or end of their shift to brainstorm ways to improve processes either at the plant, or at their home. Owen or other managers share data with them, and he, along with anyone who volunteers, offers up a reason to be grateful.
Workers have suggested fixtures that can help them hold parts so they can inspect them more quickly. When they need to meet with someone at the other side of the shop, they try to combine tasks to minimize wandering.
Currently, they’re considering how to reuse scrap, rather than trashing it, second-shift foreman Kyle Bellon said.
“We find out about issues and can pinpoint them more directly, and people who are more experienced can see these ideas from people who they would normally not talk to or maybe hear from if they were on an off-shift,” Bellon said.
But for Owen, devotion to lean doesn’t stop at the shop.
At home, he’s tried to optimize his workout routine. He’s even tried to show his wife how to improve the dishwasher-loading process. (Warning: Do not assume that lean optimization and marital harmony are compatible.)
Owen’s company has achieved some big results — including significant savings on its electric bill, which you can read about in a story covering the intersection of lean and sustainability on Page 4.
Evidence of the approach’s success also comes in a metric no plant wants on its books: Workplace accidents.
As of late October, the plant hadn’t had a lost-time accident in nearly 2,700 days.
Let’s hope that number continues to grow.
Owen is rightfully excited about the culture that’s become embedded at D&M Plastics, where workers have made 20,000-some recommendations to improve, with around 85 percent having been implemented.
“Some of them are kind of silly,” he conceded. “I’m not going to tell you every one of them is groundbreaking or earth-shattering. But they’re their ideas, and every idea is just as valid as any other idea. Some of them have saved us tens or thousands of dollars. ... Some of them haven't saved us a penny.”
But that doesn’t always matter so much as the spirit of collaboration and goodwill Owen and his employees have developed simply by listening to each other.
“It's the sharing, it's the ideas themselves, it's the camaraderie,” he said.
He believes there’s value in all the ideas, big and small.
Because, as we head into the new year, with all our resolutions to do better, it’s important to remember that even small changes — just like unnecessary purchases — can add up.
Karen Hanna | Senior Staff Reporter
Senior Staff Reporter Karen Hanna covers injection molding, molds and tooling, processors, workforce and other topics, and writes features including In Other Words and Problem Solved for Plastics Machinery & Manufacturing, Plastics Recycling and The Journal of Blow Molding. She has more than 15 years of experience in daily and magazine journalism.
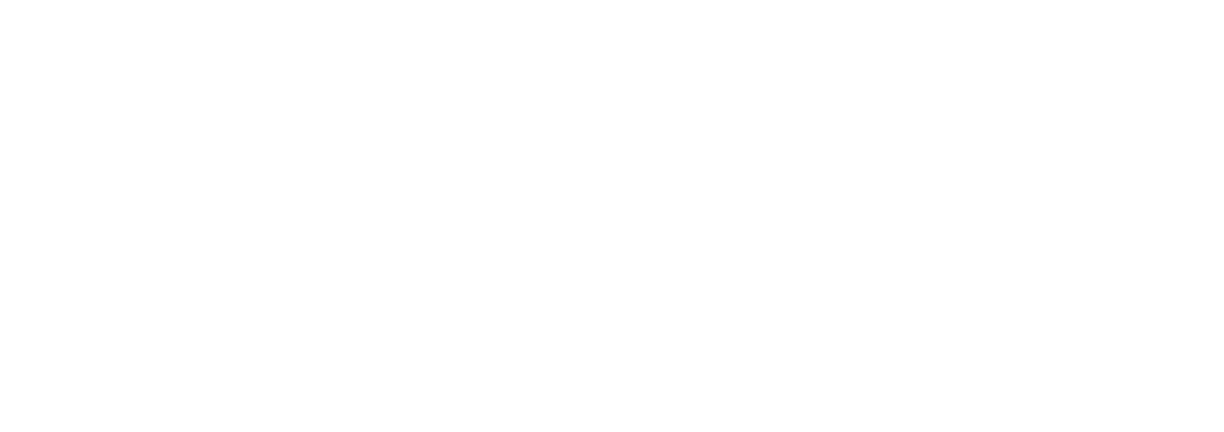