By PMM Staff
The automotive industry is ramping up production of zero-emission electric vehicles, which is creating opportunities and challenges for parts suppliers and suppliers of resins used to manufacture those parts.
The Biden administration announced a goal for clean energy vehicles (including battery electric, plug-in hybrid electric, and fuel-cell electric vehicles) to make up 50 percent of all vehicles sold in the United States by 2030.
Celanese Corp., a global chemical manufacturer, is a major supplier of resins to the automotive industry.
Plastics Machinery & Manufacturing recently asked Celanese officials how the transition was affecting their company. Celanese supplied written answers to our questions.
What opportunities does the transition from internal combustion engines (ICE) to electric vehicles open for Celanese?
As the automotive industry ramps up its production of electric vehicles, Celanese sees the emergence of a wide range of new requirements for engineering thermoplastics – as well as design challenges for Tiers and OEMs.
“Automakers are taking more stringent carbon-dioxide regulations and consumer preference toward clean-transport solutions into account. This, together with the downward trend in battery costs, is at the heart of the changes we’re seeing,” said Frank Reuter, director of Program Management Automotive Electric Powertrain, Celanese.
“Believe it or not, plastics are still not as well utilized in the automotive industry as they could be. We bridge this knowledge gap with deep application, industry, and product knowledge, supporting global automakers and their engineers from design through development and production to help make their future goals a reality.”
A key challenge faced by EV engineers is the need to increase power density. This, in turn, improves range without adding weight. Polymers can help by consolidating functional parts to remove mass. Essentially, several metal components can be integrated into a single polymer part that performs multiple functions. Plastics can also help to improve thermal management, including within cooling lines and battery cooling systems.
Reuter also sees a trend toward higher voltage (800 kW) batteries, which increases the efficiency of the powertrain.
“Plastics provide electric isolation in these higher-voltage systems, because they can meet the elevated requirements for insulation and heat management,” he adds.
In addition, electric vehicles pose unique challenges when it comes to isolating structure-borne noise and vibration originating from their electric drive units. Without the relatively loud internal combustion engine masking them, these noises become much more apparent. It’s a complex issue involving vehicle safety and passenger comfort, while engineers find it difficult to point to a single part or component that is the root cause of the noise.
Many designs still rely on metal for structural chassis and suspension system applications. However, replacing that metal with a newly formulated PA66 material, Zytel NVH Gen 2 from Celanese, offers a host of compelling improvements. This lighter-weight, next-generation composite technology gives drivers and passengers a superior driving experience by controlling noise and vibration more effectively than metal. The polymer offers high damping yet keeps its base polymer’s robust structural properties for parts that need sustained mechanical strength throughout their lifecycles.
“This new Zytel grade takes a different approach to high-frequency vibration isolation by utilizing the material’s structural damping ability without sacrificing extended fatigue resistance over time,” explains Gabe Knee, Automotive Market Manager, Celanese. “We’ve created a cost-efficient, mass-saving, and tunable solution for electric drive units that mitigates NVH [noise, vibration, and harshness] problems in electric vehicles, making them even quieter and more comfortable.”
The material can endure high-stress conditions and provide stable characteristics under varying ambient and loading conditions.
In a recent commercial application in North America involving EV motor mounts for the Cadillac Lyriq, Zytel NVH Gen 2 maintained structural integrity while offering over 20 percent direct mass savings and considerable material cost savings compared to aluminum. With these mounts, designers were able to tune, mitigate, or eliminate irritating harmonics that would otherwise be transmitted and detected by drivers and passengers in the cabin.
“With our design and prototyping capabilities,” adds Knee, “we help customers identify problematic component designs that are contributing to NVH issues, then help create the solution for managing them.”
What challenges does this transition present for the plastics industry?
“It’s tough to speak for the entire industry, but at Celanese, first and foremost, we will continue to accelerate our support for our customers. We are focused on expanding our solutions and product range,” says Reuter.
There are five main areas where Celanese materials can help EV designers achieve their goals:
- Battery System and Thermal Management: Efficient energy consumption and improved charging time are critical to electric vehicles. Celanese polymers help lighten battery housings while also improving battery performance and thermal management to help any car or truck boost performance. GUR UHME-PE stands out in innovative solutions for battery separator films for Li-Ion batteries. Celanese Frianyl PA, Celanex, Crastin PBT and Fortron PPS offer excellent electrical insulation properties in combination with high flame retardancy and thermal shock resistance for various parts in the battery system. Santoprene TPV, Hytrel TPC-ET, and Zytel LCPA are very well suited for tubes and hoses used in thermal management system of modern electric cars.
- Power Electronics: Inverters transform a direct current (DC), from a Lithium-ion battery, into an alternating current (AC) to drive electric traction motors. These processes create energy losses which are converted to heat. Plastic insulating parts like busbars in power electronics must withstand higher temperatures, and thermal shock cycles while keeping their insulation properties. Celanese Fortron PPS and Zytel HTN offer excellent thermal shock properties and electric insulating performance, combined with good temperature resistance and flame retardancy.
- High Voltage Connectors: connectors are key parts of the electric powertrain. Materials for these connectors must provide best electric insulation properties combined with flame retardancy and orange color stability. Frianyl PA, Celanex and Crastin PBT grades combine all these properties.
- Charging Technology: Charging technology and infrastructure are equally important to e-vehicle powertrain structure and battery architecture. Celanese delivers material solutions that address the wide range of stringent electrical and mechanical requirements associated with the different levels of charging.
- Autonomous and Connected Vehicles: Celanese delivers superior automotive plastic materials to meet the demands of the next evolution in transportation, ideal for control units, EMI shielding, head-up displays and sensors and cameras.
According to Reuter, outside of the electric powertrain, several challenges exist in structural areas. For example, tailgates, center consoles, overhead consoles, seatbacks, seat handles, door trim plates and visible instrument panel parts. “For the electric powertrain, we see a need for new mounts and bracket components that need to be attached to the body of the automobile. Another area that’s ideal for conversion to plastics is within the driver assistance systems that require sensors, control units, connectors, and high-speed data connectors,” he adds.
Do you have any knowledge about some of the unusual or new applications for plastics?
Plastics that intrinsically conduct energy (electrical or thermal), such as CoolPoly, as well as those that are typically filled with a metallic material to aid conduction have been in use for decades.
One of the newest Celanese applications in this area also involves Novares. Celanese worked with them to create a hybrid cooling plate that matches an aluminum sheet with a plastic layer that transfers cooling fluid. This announcement from K 2022 provides more detail.
Is the fact that plastic parts suppliers are having to meet automakers’ needs for parts for not only ICE but BEV creating a hardship for them? How are they/should they address this?
Tier suppliers and processors typically view the demand for both ICE and BEV modules as an opportunity rather than a hardship. Our customers are addressing the transition by collaborating with us more closely to identify the right materials, receive design support, and test/trial their newest products.
Are new technologies allowing automakers to begin using plastic parts for parts traditionally made from metal?
Yes, developing plastics that can replace metal in automotive applications has been ongoing in the plastics industry since the 1970s, when the first plastic parts were created to replace metal for use under the hood.
What are these new technologies and how have the technologies advanced?
Recently, Celanese has pioneered a new concept for higher-energy-density EV batteries called 3-in-1, which relies on metal replacement. The innovative 3-in-1 concept consolidates cell cooling, electrical interconnection, and structural components into an easy-to-expand, modular design. The consolidated module includes three main functions:
- Semi-direct cooling system that efficiently cools cells through their tabs
- Integrated electrical interconnects for simple assembly
- Modular Zytel HTN frame that holds all components together while offering easy expandability
This modular design also increases energy density and range. It also allows for more passenger room and improves cooling efficiency. Finally, it reduces the number of parts required, simplifies assembly, and decreases material use for a more sustainable solution and easier end-of-life cell extraction.
In addition, the Zytel NVH Gen 2 development described in the answer to question 1 is also a recent technology enabling metal replacement.
Are automakers trying to upgrade their sustainability goals? If so, what impact is this having on parts suppliers and their use of plastics?
Yes, EV and ICE manufacturers alike continue to seek improvements to their environmental footprint and that of their products. Celanese supports these efforts with a range of material solutions, including:
- Renewably sourced (RS) offerings enable lower CO2 emissions than fossil-based variants, such as Rynite ECO R and Hytrel ECO R.
- Materials that contribute to a lower overall Global Warming Potential, such as Zytel HTN51 and Hytrel ECO F.
Contact information:
Celanese, Irving, Texas, 859-372-3244, www.celanese.com
Bruce Geiselman | Senior Staff Reporter
Senior Staff Reporter Bruce Geiselman covers extrusion, blow molding, additive manufacturing, automation and end markets including automotive and packaging. He also writes features, including In Other Words and Problem Solved, for Plastics Machinery & Manufacturing, Plastics Recycling and The Journal of Blow Molding. He has extensive experience in daily and magazine journalism.
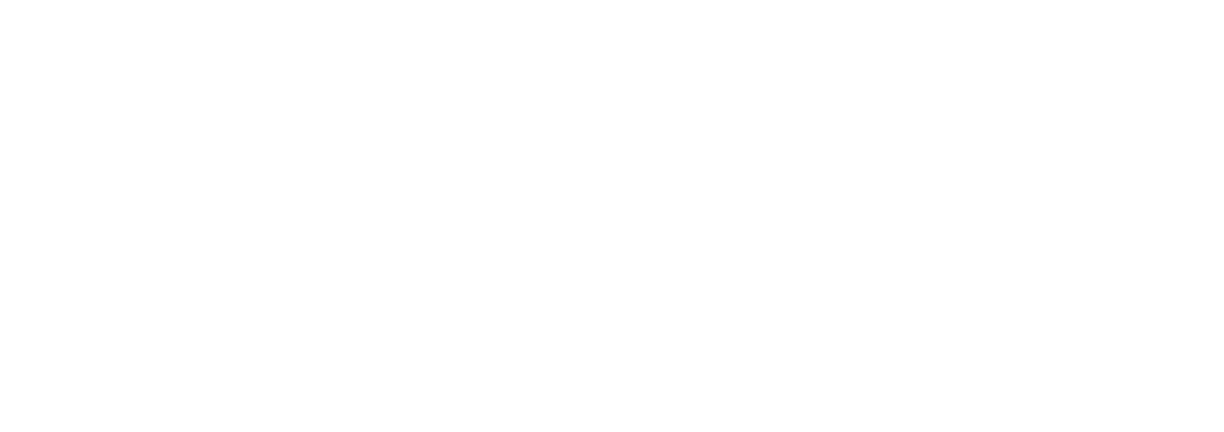