By Bruce Geiselman
From banana peels to used diapers, the materials people throw away still have value for at least one company that is turning trash into treasure, with biobased composite materials that can serve as an alternative to fossil-based plastics.
UBQ Materials, headquartered in Israel, is eyeing opportunities to bring the process to the U.S.
The company has been working with the U.S. Department of Energy to examine possible grants, and looking at potential sites for a plant. Before selecting a site, UBQ wants to ensure it has sufficient access to waste streams that meet its specifications.
The U.S. plant project has advanced considerably over the last year, Albert Douer, chairman and CEO, UBQ Materials, told Plastics Machinery & Manufacturing (PMM) in an emailed statement. Site selection is almost finished. The company has identified the waste partners it will be working with, and it has obtained tax credits that will facilitate financing needs.
Douer explained how the company converts organic waste into biobased composite materials.
“What we do is take the garbage of the garbage,” Douer said. “We take the chicken bones, the dirty diapers, the pizza box with grease, banana peels, unrecyclable plastic, the black bag that is left over that no one wants. We take out the minerals, the metals and the glass. We remove them because they are abrasive and could affect our customers.”
The minerals, metals and glass are then recycled, he said.
The household waste, consisting mostly of organic matter, is dried, chopped, fluffed and sent to reactors where UBQ’s patented conversion process reduces the organic elements into their most basic natural components — lignin, cellulose, sugars and other natural fibers. These building blocks are then bonded together with mixed plastics into “a robust matrix,” according to the company.
The result is materials that are compatible with most resins on the market including PP, PE, HDPE, polylactic acid, PVC, acrylonitrile butadiene styrene, high-impact PS, ethylene vinyl acetate and thermoplastic polyolefins.
The “fluffy material” is compressed into a pellet form for easy transportation, and distributed to compounders and product manufacturers worldwide, including in the United States.
UBQ continues to develop new products.
In 2019, UBQ opened its pilot production facility in southern Israel next to a landfill that provided municipal solid waste as feedstock. The company has worked with early adopters, including a McDonald’s franchise that uses UBQ materials in food trays and building materials in Brazil and the Caribbean; PepsiCo, which uses them in pallets and product stands; and Mercedes-Benz, which uses them in automobile parts.
Today, with an annual capacity of about 7,700 tons, the pilot production facility continues to operate as UBQ’s research and development facility.
In November 2023, UBQ opened its first large-scale facility in Bergen op Zoom, Netherlands, with an annual capacity of 88,185 tons. As a feedstock, it uses municipal solid waste that otherwise would be headed for incineration or a landfill.
The production plant envisioned for the U.S. would initially produce about 110,200 tons of material, but UBQ wants to secure a site with adequate room to produce over 330,693 tons, according to the company.
UBQ calls its materials “the most climate-positive thermoplastic on the market.”
Production of UBQ material is carbon-negative (i.e. climate-positive), according to information on the company’s website.
The company uses only electricity from renewable energy sources, and waste heat from one part of the process is reused in drying the waste material during production to reduce carbon emissions. That allows the company to avoid using natural gas, for example, in the drying process.
In addition, since the UBQ material is manufactured from mostly biobased material, it stores carbon atoms that were removed from the atmosphere, said Kurt Kronawittleithner, UBQ’s applications director. It’s considered biobased carbon dioxide removal, he said.
While UBQ can substitute up to 100 percent of the plastic content in a product, most customers blend the material with traditional plastics to reduce the carbon footprint of their products. The amount blended depends on users’ goals and application. In some cases, particularly if UBQ materials are blended with post-consumer recycled plastics, users can achieve a carbon-negative number, Douer said.
UBQ materials can be compounded with additives commonly used in the industry to meet requirements involving characteristics such as impact- or ultraviolet-light- resistance, or coloration.
UBQ’s website says the materials have been tested for recyclability. They can be recycled in conventional streams without disrupting the recycling system, and users are still able to get the same properties, according to the company.
“Any scrap UBQ produced in our plant is reground and used to create new UBQ material. To ensure the recyclability of UBQ in conventional recycling streams, we have enlisted the expertise of Axion Group for thorough assessment and verification,” according to the website.
UBQ describes its material pricing as “competitive to existing resins.”
UBQ materials are appropriate for a variety of plastic processes including injection molding, compression molding, rotomolding, extrusion and 3D printing.
They are used across a variety of industries including the retail, furniture, construction and automotive segments. They have been used in producing food trays, hangers, shopping carts, pipes, panels, furniture, auto parts and 3D printing filaments.
Contact:
UBQ Materials, Bergen op Zoom, The Netherlands, 31-16-444-4800, www.ubqmaterials.com
Bruce Geiselman
Senior Staff Reporter Bruce Geiselman covers extrusion, blow molding, additive manufacturing, automation and end markets including automotive and packaging. He also writes features, including In Other Words and Problem Solved, for Plastics Machinery & Manufacturing, Plastics Recycling and The Journal of Blow Molding. He has extensive experience in daily and magazine journalism.
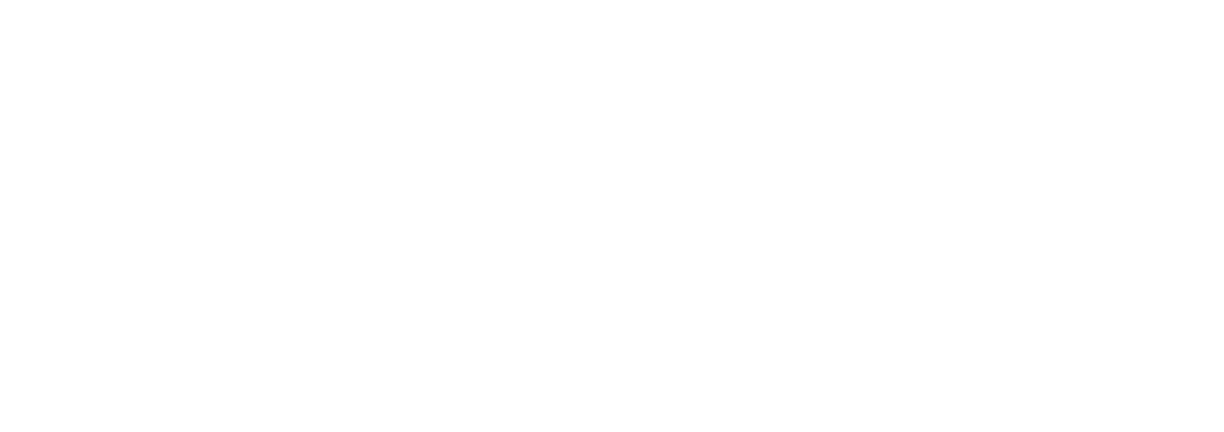