A regular injection molding production run at The Specialty Mfg. Co. is relatively small, producing just 10,000 to 20,000 parts, but that has not stopped the custom valve manufacturer from operating one lights-out shift and another with very few press operators.
A thoughtful combination of molding machines and auxiliary and automation equipment in the plant, plus a willingness to try new procedures, make it possible.
“We specialize in specialized products,” said John Ray, molding production manager at the White Bear Lake, Minn., company near St. Paul. “Some of our production runs may be as short as 30 minutes. A lot of people won’t do that.”
The Specialty Mfg. Co. is a family-owned business established in 1900. It is organized into seven divisions, with the valve products division being one of the company’s largest. The division produces a wide array of valves and check valves in brass, stainless steel and plastics used in many end markets. In an industry in which most companies specialize in either metal or plastic valves, Specialty Mfg. is among the largest companies making both.
Every valve is a custom product, and no single customer accounts for more than 3 percent of Specialty Mfg.’s total plastics business.
“There is no standard valve,” marketing manager Bruce Boe said. “Our customers can go online with their specs, use our valve-design tool to see the exact valve they need. Our valve configurator provides an animated CAD model and a detailed bill of materials that we manufacture to and deliver in three weeks or less.”
Some valves are made entirely from plastic and some metal valves have plastic parts such as handles, seats and retainers. The company has more than 100 machining centers to manufacture metal valves.
Miniature plastic valves can be as small as 1 inch long.
Specialty Mfg. gets as many as 1,000 orders a day for valves. Seventy percent of the business comes from companies that have been customers of Specialty Mfg. since 2003.
“Every hour, we are responding to customers,” President and CEO Dan McKeown said. “There is no production schedule for the week. With a three-week lead time and no inventory, we have to change every day. There is also an underlying culture of the people pulling together to make it happen.”
The valve division has 18 injection molding presses with clamping forces of up to 500 tons. The smallest is a 60-ton rotary shuttle press.
Ray said the flexibility his plant needs to juggle so many different products starts with Haitian presses. The move to Haitians began about eight years ago when the company started replacing its aging Van Dorn presses.
“We like the general-purpose machines because we mold such a wide array of things,” Ray said. “We run a lot of PVC, and it rusts everything. We shift a lot of other materials in and out. The Haitian machines fit our niche.”
He said Specialty Mfg. evaluated all the top machine brands before purchasing its first Haitian. “We saw a lot of similarities with the Van Dorn presses we were familiar with,” Ray said. “That made our learning curve fast.
“The price point was incredible. That was a big selling point for us.”
Specialty Mfg. installed three new Mars series Haitians last spring and is negotiating with Absolute Haitian, the U.S. sales operation for the Chinese press manufacturer, for three more this year to support replacement and growth requirements.
New presses are specified with a specific barrel twist rate and shot size. Specialty Mfg. also orders presses with a second pump to facilitate part ejection. “We have had good luck in not having to change the barrels,” Ray said.
“We also use their service department because we get great service,” he said.
One feature that Specialty Mfg. relies on is the Haitian control system’s automatic shut-down function. That enables the lights-out third shift, as well as a second shift that runs with minimal operators on duty.
“The Haitians are so good about shutting down,” Ray said. “You set your parameters, and the machine shuts itself down if anything goes out of those parameters.”
Ray said the move to a lights-out third shift took a lot of trial and error. “When we first started, we had a lot of problems with machines shutting down because we had not programmed everything correctly,” he said.
“In the beginning, we might get only two to three hours of production out of a machine before it shut down,” he said. “Some of our longtime employees said it was a waste of time to try to run lights-out. But I looked at it as gaining production time every night.
“They are believers now,” Ray said. “This was a change in philosophy that we had to go through with our people.”
Ray now requires operators to keep the automatic shut-down function on even during the first shift. He said that if something is going to go out of tolerance, it is likely to happen during the day. “If it runs all day long with the automatic shutdown engaged, it will probably run all night long,” he said.
Another big step in running lights-out was the move to Wittmann Battenfeld chillers and temperature control units. “It helped us minimize our risk,” Ray said. “They have turned out to be very reliable.”
Ray said the company had to “engineer our way out of the objections our people had” to lights-out molding and short production runs. Choosing the right equipment was part of that process.
The control system on Specialty Mfg.’s current Haitian presses does not include a remote alarm function when a press shuts down, but Ray said the next presses with Haitian’s next-generation control units will. “I will be able to use that feature,” he said.
Currently, he relies on a rotating camera system he can activate from home when he wants to check on third-shift operations. “I look forward to having the alarm because there may be a time when something goes wrong 20 minutes after the second shift walks out the door.”
While the third shift is a lights-out shift, the second shift runs with just two machine operators in the plant. Previously, it had about 10. The two are needed because a small number of molds require manual operations.
A crew comes in Saturday morning to stop the machines. Another crew comes in Sunday to restart everything but does not stay through the night.
“We are always looking for ways to make things run automatically,” Ray said. “My goal is to have just material handlers and technicians. We just need people to check the jobs and keep the machines full.”
Ray said he expects the Haitian presses to last 12 to 15 years.
In the future, Ray said he hopes OEMs will offer as an option autoloaders already installed on their presses. He also said press makers need to consider how conveyors connect with each machine. Specialty Mfg. uses conveyors in nearly every molding cell.
The company averages about 60 mold changes a week. Typical molds have four cavities, but a few have as many as 16 cavities.
Average cycle times are about 60 seconds.
Specialty Mfg. does not have resin silos. Resin comes into the plant in gaylords and bags. While PVC is often used, the plant also processes a wide range of engineering resins.
Resin is assigned a lot number that is tracked through the manufacturing process.
McKeown said many customers want different colors for handles and other parts. “Color is important for our customers because valves are for input or output. We have done a lot of work with different colors,” he said.
Press utilities such as air, water and electricity drop down from the ceiling and are connected to presses through a cabinet designed and built in-house. This helps reduce clutter on the floor, which Ray said is important even in a lights-out plant. “People come in and don’t always turn on all the lights,” he said. “It can be a safety problem if they are climbing over cables and pipes.”
Specialty Mfg. currently has 357 molds and four interchangeable master unit die sets with more than 250 combination of inserts. Not every part requires a unique mold. “Sometimes we can make a new fitting by putting a new insert into an old tool,” said Dennis Johnson, director of engineering. “It is a lot easier to design the insert than an entirely new tool.”
The company builds all its own testing stations. Typically, valves must be pressure-tested after assembly.
Parts are generally moved by conveyors to gaylords to facilitate lights-out operation. Parts are shipped out of the molding area three times a day either directly to customers or to an in-house area where valves are assembled.
Ray said the company is looking closely at buying its first collaborative robot to use in the plastics molding operation. One is already working in the metal machining plant.
The valve division’s plastics processing is tucked into about 12,000 square feet of space. About 30 full-time employees are involved in the injection molding operation. Valve assembly with another 60 to 70 employees is adjacent to the molding area.
Senior employees run a formal training program for new staff members and employees moving to different jobs. “It has worked well for us,” Ray said, but he admitted that finding employees is a challenge in an area with plenty of manufacturing.
The company has a smaller injection molding operation in Granite Falls, Minn., to support its dental products business. That facility has six molding machines with the largest at 60 tons of clamping force.
Ron Shinn, editor
Contact:
The Specialty Mfg. Co. White Bear Lake, Minn., 651-504-3287,
Ron Shinn | Editor
Editor Ron Shinn is a co-founder of Plastics Machinery & Manufacturing and has been covering the plastics industry for more than 35 years. He leads the editorial team, directs coverage and sets the editorial calendar. He also writes features, including the Talking Points column and On the Factory Floor, and covers recycling and sustainability for PMM and Plastics Recycling.
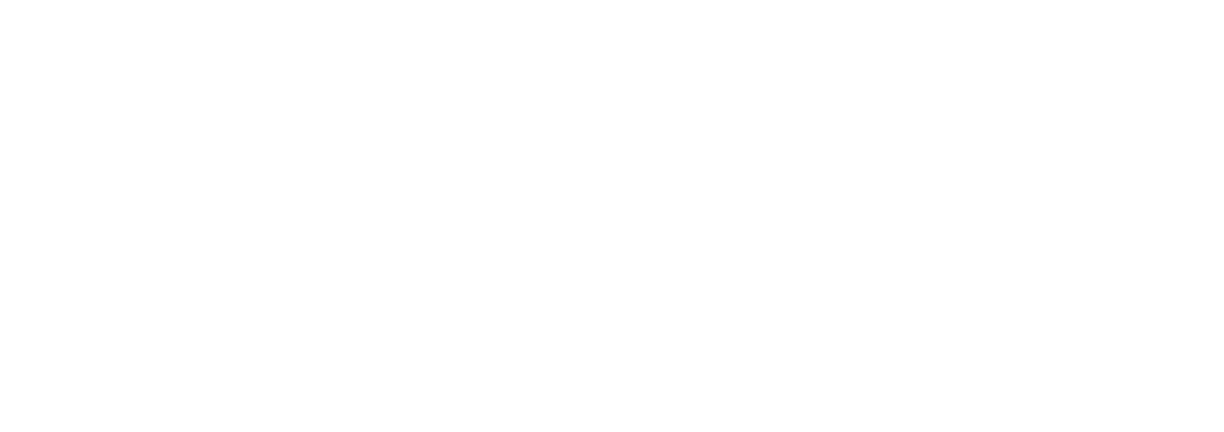