MK 825 Pro This Henkel mixing head can dynamically mix and dispense beads of multiple components, including medium- and high-viscosity materials, such as polyurethanes, silicones, epoxy resins or other polymeric reactive materials. Beads applied in this way foam up and cure in a matter of minutes at room temperature in a process manufacturers of plastic enclosures, and automotive, electronics, lighting, filter and packaging components can use to make foam gaskets. The mixing head also can be used to dispense adhesives and potting materials.
What's new? Improved valve technology, and a host of new features, including continuous pressure control and automatic adjustment, temperature control, a “click-and-drop" quick-mounting system and an integrated, optional cooling system.
Benefits Precision mixing and dispensing, and a maintenance-friendly design, thanks to recent improvements. The MK 825 Pro is designed to provide process stability. Together with the dosing machine, the MK 825 Pro features sensors that collect a wide range of data for monitoring and compliance with critical process parameters of the formed-in-place foam gasket application process, such as the degree of air loading, axial position of the agitator shaft in the mixing chamber, material pressure at the valve and the temperature in the mixing chamber, as well as the positioning of the dosing needle. This information can help with predictive maintenance.
Henkel Corp., Elgin, Ill., 847-888-1110, www.sonderhoff.com
Karen Hanna | Senior Staff Reporter
Senior Staff Reporter Karen Hanna covers injection molding, molds and tooling, processors, workforce and other topics, and writes features including In Other Words and Problem Solved for Plastics Machinery & Manufacturing, Plastics Recycling and The Journal of Blow Molding. She has more than 15 years of experience in daily and magazine journalism.
Censco acquiring MuCell Extrusion Technology
KraussMaffei now building extruders in U.S.
Nordson names regional sales manager
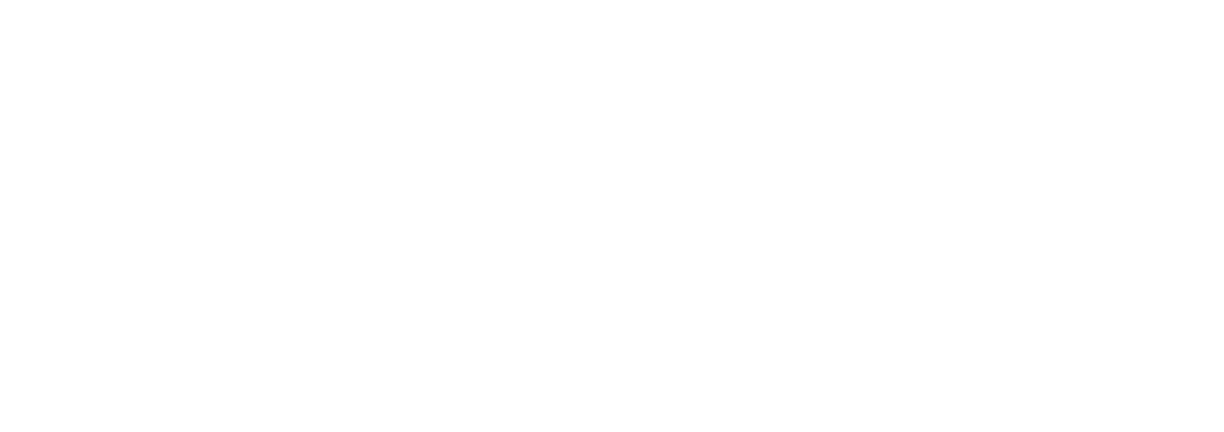