Priority Plastics boosts capacity with ISBM machines
By Bruce Geiselman
Priority Plastics recently spent $5 million to install new injection stretch blow molding (ISBM) machines at its Portland, Ind., plant that can produce containers ranging in size from 1 gallon to 25 gallons.
A European manufacturer supplies the single-stage ISBM machines; in the U.S., the OEM is supplying machines with the ability to make unique neck shapes, handles and larger sizes exclusively to Priority Plastics, company officials said.
Priority Plastics declined to reveal the manufacturer or how many of the blow molding machines it purchased, saying the information is proprietary. However, it said the technology significantly increases the company’s PET container production capacity and its ability to offer unique container shapes and sizes.
Each of the new machines can manufacture PET containers ranging from a 1-gallon jug to a 25-gallon drum — an unusually large size range. The largest PET container Priority Plastics currently produces has a capacity of just over 1 gallon. Each new machine can, depending on container size, produce up to 6 million units annually.
“There’s a fairly large size variation on these machines that a lot of other ISBM equipment does not have,” said Nate Zimmerman, director of business development for Priority Plastics, which also blow molds rigid plastic packaging from HDPE and PVC.
The new machines can manufacture PET containers with a variety of neck shapes, including rectangular.
They also can make PET containers with integrated handles — commonly used for milk, juices and oils — without creating any scrap. Such integrated handles are common with HDPE containers, but are normally difficult to produce on PET bottles, the company said.
The new technology lets Priority Plastics produce PET drums, which have the advantage of weighing less than HDPE drums; containers with wider or rectangular neck openings; and stackable bottles.
PET bottles are lighter than comparable HDPE containers and have a smaller carbon footprint, the company said. The machines also consume as little as 60 percent the amount of electricity of other similarly sized machines.
“It’s a hybrid servo-over-hydraulics machine,” said Ed Cooley, Priority Plastics’ director of engineering. “It helps [flatten] the curve of power usage — you don’t have spikes in power [consumption].”
The machines are equipped with a patented air-regeneration system that recovers two-thirds or more of the high-pressure blowing air used to make the containers. The system captures exhaust air in a receiver tank until it is repurposed for use with low-pressure auxiliary equipment.
“Instead of having two separate compressors … it utilizes the existing air,” Cooley said. “Not having as much auxiliary equipment to operate the machines is a huge savings in energy.”
The energy-efficient machines allow Priority Plastics to help customers meet their sustainability goals.
The ability to produce a wide range of bottle sizes and unusual container and neck shapes, combined with the energy efficiency of the machines, is unique, Zimmerman said.
“We are the only company in North America that is going to have these machines,” Zimmerman said.
Priority Plastics said it initially is targeting a number of bulk packaging markets for its new equipment. Contents could include candies, nuts, pretzels and other snacks; sauces and dressings; nutritional powders and supplements; pet treats and snacks; alcoholic freeze pops; juices; and beverages.
“Those are about five to eight markets that we see a good fit for — it’s more of the larger bottles,” Zimmerman said.
This is the second major investment the company, which has facilities at four locations across the U.S., has announced in the past year and a half.
In August 2019, it invested more than $5 million in equipment, molds, training and technology for a high-speed tight-head machine at its Portland plant. The machine, which the company calls “the Cyclone,” produces UN-rated tight-head containers, which are made of HDPE and are used to safely transport liquids such as chemicals. The Cyclone produces them in 5-gallon and 20-liter sizes.
“This equipment allows us to produce tight heads faster than anybody in North America,” Zimmerman said. “Another thing that is unique about it is it is often multilayer, and there can be a lot of postconsumer regrind in the middle layer.”
Containers with a layer of post-consumer resin sandwiched between two layers of virgin plastic meet food packaging requirements.
Bruce Geiselman, senior staff reporterbgeiselman@endeavorb2b.comContact:
Priority Plastics, Portland, Ind., 720-548-5893, www.priorityplastics.com
(Contact person for Priority Plastics is Stephanie Oliva.)Bruce Geiselman | Senior Staff Reporter
Senior Staff Reporter Bruce Geiselman covers extrusion, blow molding, additive manufacturing, automation and end markets including automotive and packaging. He also writes features, including In Other Words and Problem Solved, for Plastics Machinery & Manufacturing, Plastics Recycling and The Journal of Blow Molding. He has extensive experience in daily and magazine journalism.
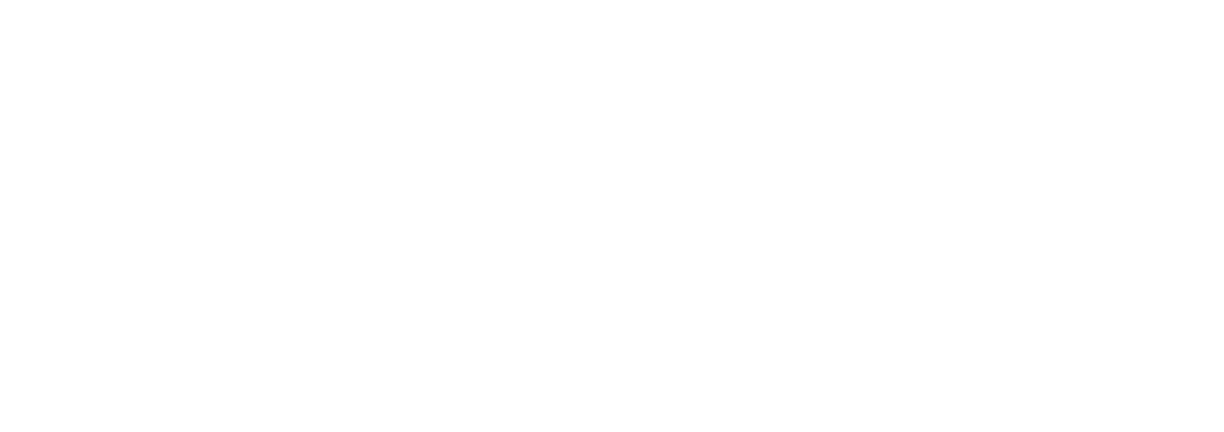