By Ron Shinn
and Karen Hanna
Blow molding machinery manufacturers are adding new machines and features that are designed to increase production output and at the same time are easier to operate.
Faster color changes and complete product changeovers will boost productivity. New HMI control interfaces are becoming more intuitive and help operators reduce costly errors.
Here are highlights:
Sipa’s ECS SP 25 for small containers in small lots
PET packaging technology specialist Sipa demonstrated its single-stage, injection stretch blow molding (ISBM) system ECS SP 25 for small containers at K 2022. The four-station machine can produce ultraclean bottles, containers that can be pasteurized and warm- and hot-fillable bottles with amorphous necks.
The company said the ECS SP 25, which joins the ECS SP 80 in the series, features an upgraded user interface (HMI), improvements in the injection system, preform conditioning and bottle blowing. It can also accept a wide range of legacy molds, including molds originally designed to run on competitors’ machines.
The ECS SP 25 is also designed for quick product changes, energy efficiency and a compact form factor. Time required for a complete mold change is said to be 2.5 hours. A color change in 15 minutes was demonstrated at K 2022.
The model has from one to 10 injection and blowing cavities. In the one-cavity configuration, maximum thread dimension is 100mm, maximum container weight is 240 grams and maximum body diameter is 150mm. In the 10-cavity configuration, maximum thread diameter is 15mm, container weight is 24 grams and body diameter is 35mm.
Maximum output is up to 4,500 bottles per hour.
The ECS SP machines are best suited for producing smaller lots of containers. Sipa’s ECS FX series single-stage blow molders are favored for larger lots.
The blow molder has a hydraulic clamping unit and servo-electric drives for opening and closing of the blowing unit, melt injection and preform stretching. Only one hydraulic pump is required. An accumulator system provides smooth and fast hydraulic operations.
The hydraulic circuits and components are positioned on the lower side of the machine to help guarantee a clean production environment for food and pharmaceutical applications.
Sipa, based in Italy, said it can accommodate PET, recycled PET, regrind PET, PP and PLA.
Typical products include specialty containers used for cosmetics, personal care products, detergents, motor oil, miniature spirits and pharmaceuticals. It can also make bottles with sharp edges and other challenging shapes, including embossing.
Sipa said in a press release that the ECS SP machines may be able to make inroads into the market for high-quality, small bottles used for prestigious cosmetic and beauty care products. It recently developed prototype cosmetic containers with striking designs ranging from 200 mL to 475 mL in round, oval and rectangular shapes.
Magic focuses on ease of use
Features that automate blow molding equipment and make it easier to use took the spotlight at Magic’s booth at the K Show.
The company’s display included the MTM 170–S, a single-stage, all-electric ISBM , along with an extrusion blow molder (EBM) featuring Magic’s new Self Adjustment Machine (SAM) and quick-changeover features, available on all new all-electrics.
Designed for producing PET bottles, the compact and quiet MTM 170–S is Magic’s largest machine, with 25 tons of clamping force. It boasts a new rotary-table design that provides easy access for mold changes, along with a new three-axis take-out system, which automatically positions the bottles on a conveyor belt. The MTM 170–S consumes only 12 kilowatts of energy per hour when running at full power.
Magic’s SAM has features dealing with eight different characteristics of the machine: automatic head-center-distance adjustment, from 240mm up to 280mm and vice-versa in a two-parison head; automatic features for blow-pin center distance; parison centering; parison cutting vertical adjustment; centering of post-cooling; extruder platform adjustment for head-height setting; and clamping-force adjustment; and mold holding plates with Stäubli magnetic centering system and bayonet couplings for mold cooling.
The convenient features were on display on Magic’s ME T18-800-S EBM. With the quick-change system, the Magic team performed a changeover alternating between 5-liter bottles to 10-liter containers in just 20 minutes, 40 seconds.
In addition to the other innovations, Magic also announced it has begun offering complete accessories for its MTM series, including hot runners, conditioning stations and molds for PET containers.
Wilmington Machinery displays new Series IV rotary blow molder
Wilmington Machinery unveiled a new Series IV, all-electric eight-station rotary blow molding machine for calibrated bottlers ranging from 8 ounces to 4 liters that are used for food, chemicals and other applications.
The new machine, shown at K 2022 for the first time, is available with single, dual and triple parison die heads for monolayer or multilayer bottles. The single-parison head can produce up to 48 bottles per minute, and triple-parison versions can produce up to 144 bottles per minute.
Wilmington Machinery said the Series IV has a small footprint and needs minimal labor and maintenance. The control system is operator friendly and provides for data collection and trending analysis, the company said.
Ron Shinn, editor
Karen Hanna, senior staff reporter
Contact:
Magic North America, Whitmore Lake, Mich., 734-358-7722, www.magicnorthamerica.com
Sipa North America, Atlanta, 404-349-3966, www.sipasolutions.com
Wilmington Machinery Inc., Wilmington, N.C., 910-452-5090, www.wilmingtonmachinery.com
Ron Shinn | Editor
Editor Ron Shinn is a co-founder of Plastics Machinery & Manufacturing and has been covering the plastics industry for more than 35 years. He leads the editorial team, directs coverage and sets the editorial calendar. He also writes features, including the Talking Points column and On the Factory Floor, and covers recycling and sustainability for PMM and Plastics Recycling.
Karen Hanna | Senior Staff Reporter
Senior Staff Reporter Karen Hanna covers injection molding, molds and tooling, processors, workforce and other topics, and writes features including In Other Words and Problem Solved for Plastics Machinery & Manufacturing, Plastics Recycling and The Journal of Blow Molding. She has more than 15 years of experience in daily and magazine journalism.
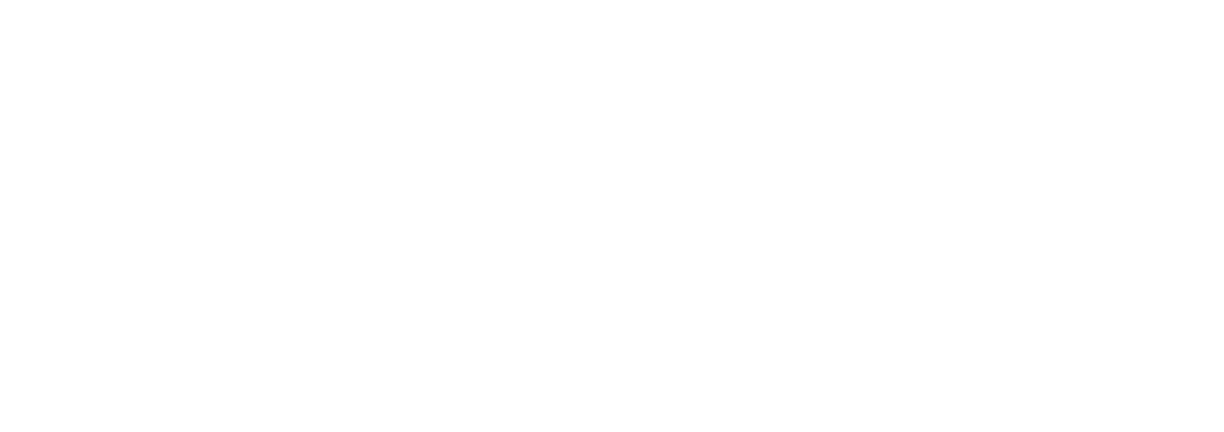