Sidel unveils Super Combi Compact
By Bruce Geiselman
A rise in consumer demand for healthy beverages prompted Sidel to introduce its Super Combi Compact, which blow molds bottles and fills them with drinking water.
The line is similar to its Super Combi introduced two years ago in that both integrate five process steps – preform feeder, blow molding machine, labeler, filler/capper and cap feeder – into an all-in-one automated system. However, as the name of the new system implies, its footprint is 30 percent smaller than the earlier model.
In addition to its smaller size, the Super Combi Compact includes new filling technology the company has named Sidel EvoFILL HS Still that produces and fills noncarbonated water bottles 30 percent faster than a standard filler.
Sidel says it developed the blow molding, bottling, labeling and capping system to occupy limited space and offer low per-foot production costs and reduced cost of ownership.
“We see that the water category has been seeing an unprecedented growth fueled by a worldwide increase in demand,” said Stefano Baini, product manager for filling and the Super Combi portfolio. “Due to consumers’ rising health consciousness paired with the trend toward so-called ‘better-for-you drinks,’ the packaged water category has remained at the forefront of consumer purchasing decisions since 2018.”
Super Combi Compact’s labeling technology features faster changeovers and easy replacement of parts. In addition, the line can accommodate different types of labels including roll-fed and pressure-sensitive labels.
The EvoFILL HS Still filling technology employs proportional filling valves controlled by electromagnetic actuators that ensure accurate filling of water into the bottles. The technology requires little maintenance costs, according to the company.
A new hygienic valve design assures beverage quality with no flavor transfer, according to the company.
“Its new compact design and innovative filling technology makes it an ideal solution for maximizing production and increasing line efficiency at the best TCO [total cost of ownership] per square foot, allowing producers to make the most of their existing space or new greenfield projects,” Baini said.
Bruce Geiselman, senior staff reporter
bgeiselman@plasticsmachinerymagazine.com
Contact:
Sidel Inc., Norcross, Ga., 678-906-8840, www.sidel.com
Bruce Geiselman | Senior Staff Reporter
Senior Staff Reporter Bruce Geiselman covers extrusion, blow molding, additive manufacturing, automation and end markets including automotive and packaging. He also writes features, including In Other Words and Problem Solved, for Plastics Machinery & Manufacturing, Plastics Recycling and The Journal of Blow Molding. He has extensive experience in daily and magazine journalism.
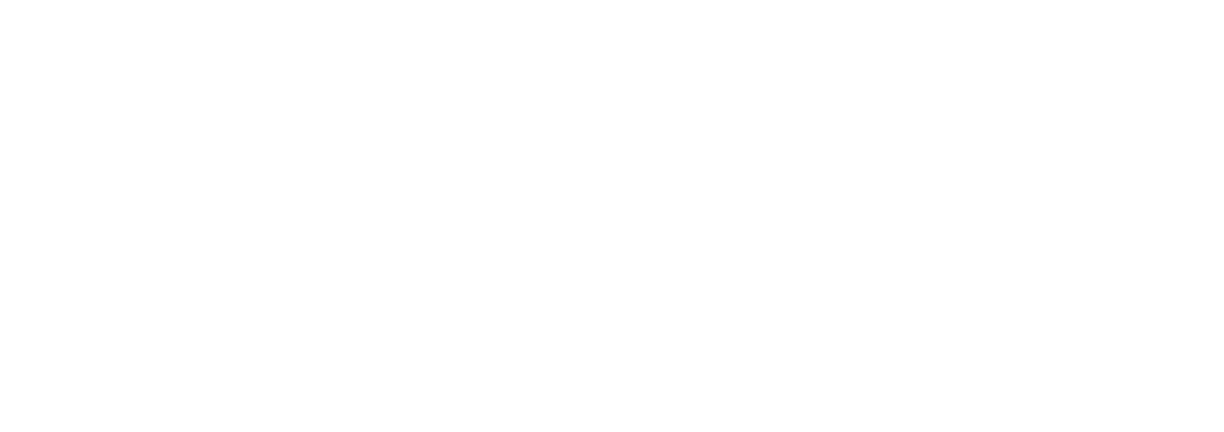