By Lynne Sherwin
Crumpled single-use bottles littering roadsides and waterways are potent symbols of the plastics industry’s environmental problems. So it's no surprise that sustainability is top of mind for blow molding machinery makers — energy efficiency, boosting use of recycled and bio-based materials, improving process quality, even the types of containers customers are seeking to make.
After years of pushing back against green efforts, the industry is now leaning in.
“Whatever changes come for the environment and recycling will come from within the plastics industry. That’s a positive for us,” said Ron Gabriele, global sales and marketing manager for Jomar. “I’ve been in the industry for 12 years. My first couple of years, nobody talked about sustainability. Now that’s all the time.”
At NPE2024, blow molding machinery OEMs discussed these issues, along with ways they can help processors compensate for the lack of skilled workers, and whether Industry 4.0 is a useful tool. (Spoiler alert: It depends).
Making more sustainable containers
Blow molding OEMs said the sustainability push presents sales opportunities for new machines, upgrades, retrofits and heads.
“Our whole booth is centered around recycling, sustainability of plastic. It’s something that we have to have: the capability to handle different materials, different levels [of recyclate],” said Steven London, president and COO of Bekum America Corp., who also served as chairman of NPE2024. “Everything we’re doing is making sure our customers have access to the technologies they need to satisfy their customers.”
Bekum had its new tri-layer extrusion head on display, which is retrofittable onto the company’s smaller machines and allows processors to incorporate an inner layer of PCR.
“I am really looking forward to finding a way to contribute to the market for a more sustainable model,” said Pietro Spiga, North America sales and marketing manager for Magic. “We don’t run the bottle; we manufacture the machine. We have customers that on the same machine run 100 percent virgin HDPE, others run 100 percent PCR material. But in any case, we need to have a solution for the customer.”
He said he is seeing demand for multilayer capabilities, especially for cosmetic, automotive and chemical applications, as well as bioresins.
At NPE, Spiga detailed how Magic worked with a California processor to modify a Model ME T14-600-D all-electric extrusion blow molding (EBM) machine so it could handle polyhydroxyalkanoate (PHA), a demanding bioresin that is 100 percent biodegradable.
"Ninety to 95 percent of the machine is standard, so it's the same machine that runs HDPE or extrusion PET. What was changed was on the components where we run the material,” Spiga said, including the extruder barrel and screw, some inside parts of the head and parts of the mold plate.
“The mold that they have to run, they’re not cool, but they are warm, because this is a material that if you run with a cold mold like HDPE, you will not be able to remove [the part] from the mold ... It crystallizes, so the material will stick on the mold,” he said.
Tetiana Pronikova, head of marketing for PET Technologies, said the company’s new APF-Max 3U stretch blow molder is capable of running 100 percent recycled PET (rPET). She pointed out the blow molder’s near-infrared heating system, which helps ensure the quality of a bottle made from PCR, “because always recycled PET requires a high temperature to be processed in comparison with a virgin one.”
R&B Plastics Machinery’s new RBS-E550D EBM machine has tri-layer capabilities, allowing processors to sandwich recycled material between layers of virgin resin, said President and GM Fred Piercy: “We believe that’s important, with a lot more of a sustainability push these days.”
“With our three-layer [accumulator] heads, you can have two extruders, where you have an A, B and A layer structure, or you have three extruders, A, B and C, three distinct layers,” said Andrew Hobson, director of sales for BBM America, which builds tri-layer heads for accumulator and continuous extrusion applications, along with other blow molding equipment.
The company’s patented accumulator heads allow processors to use more PCR, he said, as they produce distinct layers with no mixing of the PCR with the virgin layers on the interior and exterior of the container.
Uniloy is developing new technologies to handle both post-consumer and post-industrial resin, said CEO Gary Riley, but collection of waste plastic to feed the market remains a problem.
“In the United States, we just do not capture as a country enough of the waste stream to make that a viable business. We have the technology to use it. But when you’re capturing 10 percent of your waste stream, it’s kind of hard to build a business around reprocessed resin. And I think a lot of the players are kind of losing confidence in the market,” he said.
Steven Rocheleau, president of Rocheleau Tool & Die, said sustainability efforts in the dairy business, which makes up a large part of his company’s customer base, are focused on lightweighting and bottle design.
“A lot of people now are looking to move to the lightweight designs for sustainability. That really puts a focus on some of the 30- or 40-year-old equipment. Sometimes it’s hard to take that new bottle design and make it work really well on really old equipment,” he said.
“Those are the people that are more inclined now to say, ‘We’re going to move to a lightweight bottle design for sustainability, [so] we want to look at it on a new machine platform that has a higher efficiency level,’ ” he said. There’s “probably 25 percent less energy consumption than the installed machines that they’re replacing. So there’s an energy savings and a weight savings from the bottle itself.”
Cleaner and greener with electricity
Rocheleau isn’t the only company seeing interest in more-efficient machines. Even though energy costs and regulations are a bigger source of concern in Europe and other parts of the world than in the U.S., anything that can help the bottom line is attractive. As London said, “if a manufacturer can save money on the cost of the production, then it’s better for them.”
In most cases, that means all-electric machines, or models with fewer hydraulic components.
London said Bekum’s all-electric EBlow 407D machine, which it showed at NPE, is its most efficient, with its e-Twin-Toggle mold closing system: “There’s no energy used when there’s no motion because of our clamping system. We have a special design that allows it to stay locked in full tonnage, without holding motor torque on it.”
He added, “Even with our hydraulic machines, we’ve used premium efficiency motors for years, and really done a good job of managing the energy.”
Uniloy announced at the show that it had signed an agreement to integrate Baumüller’s digital technologies into its machinery to enhance energy efficiency, control and integration with Industry 4.0 standards, beginning with its new high-cavitation reciprocating machine.
“We’re partnering with them on drives and motors that are high efficiency, so our new machine uses less energy than the old one. And we get about 25 to 40 percent more bottles out, so energy savings per bottle is great,” Riley said.
Jomar has developed a hybrid solution for its 85-S injection blow molding machine, which Gabriele said is the company’s most popular size.
“The clamp is still hydraulic on the machine, but the plastifier is now fully electric. We see that as our transition towards, or our evolution towards an all-electric machine that we hope to unveil sometime next year,” Gabriele said.
The benefits for the new model are mostly hygienic, as the company’s machines of that size are already servo-hydraulic, and 40 percent more efficient than a fully hydraulic machine, he said.
“For the domestic market, frankly, that kind of energy savings has been satisfactory, and it’s been well-received. Overseas, there’s still a little bit more of a demand on efficiency and ... a move away from hydraulics. The demand for all-electric comes from overseas,” he said.
Hobson said BBM’s machines are all-electric except for its largest models, which are hybrids with hydraulics “just for the tonnage.”
Rocheleau’s RS-90 reciprocating screw machine, with new features that debuted at NPE, is also a hybrid.
“It’s not fully electric, but we have a [variable-frequency drive] on the extruder through a hydraulic motor. So the efficiency is very close to a full-electric machine, but with much more simplicity and less maintenance, less cost to maintain and operate,” Steven Rocheleau said.
“We are focused, as many other companies are, on sustainability and the green economy. We have a lot of solutions in our machines to reduce the carbon footprint,” said Giorgio Longoni, sales director for ST Blowmoulding.
The company introduced its AH series of dual-head extrusion blow molders at NPE, which reduces energy consumption by 40 to 60 percent by using hydraulics only for the final locking stage, according to the company.
Tentative steps toward Industry 4.0
While injection molding machinery makers put their artificial intelligence and smart factory technologies front and center at NPE, some blow molding machine makers are dipping a toe into smart applications, while others are diving in headfirst. Most said they want to use technology to help less-skilled operators.
“I’m a very technological guy, and I think extrusion blow molding is the most outdated commodity. I mean, honestly, I see in injection [molding] and everywhere else, I see futuristic HMIs and all this stuff. There’s a lot of homework to be done in blow molding,” said Mario Jardin, director of aftermarket and service for tooling maker W. Müller.
He sees many processors as reluctant to invest in technology, not realizing it can boost their bottom line.
“People, I think, in their ‘we’ve always done it that way’ attitude sometimes don’t see that benefit yet. We have to open eyes on how that will benefit them in the long run,” he said. “Yes, at the beginning, it might be a bigger investment. But in the long run, it will pay off. They will see a return on investment fairly quickly.”
Gabriele voiced a similar sentiment. “I’m always kind of fascinated with plastics industry moves. At some points, it’s so high-tech, and so progressive. And in some points, it’s so conservative and kind of behind the times,” he said.
He said Jomar is beginning to explore an artificial intelligence (AI) solution, starting with tracking process data so machines can develop deviation reports and predictive maintenance functions. “How do we collect that data? And what kind of sense can we make of it? That’s where we are now,” he said.
Piercy said R&B’s new RBS-E550D doesn’t integrate a lot of smart technology, but it does connect to the internet for remote troubleshooting if customers want. He said his company is more concerned with making its machines easy to use, with control systems offering multiple screens and levels of expertise, from an operator to maintenance staff to a “super user.”
“I think people are a little bit reluctant to get into some of it. ... We seem to have a whole shift in the general market with people, operators. Everyone needs good people, right? And operators are hard to come by. ... We do focus a lot on our machines and keeping it simple, to be able to be intuitive to the operators,” he said.
London said Bekum’s machines are OPC-UA compliant, and their control systems, manufactured by Beckhoff, monitor key parameters, as well as energy consumption and other factors. The company has worked with buyers to customize control systems to meet their needs.
“AI should make life simpler. It shouldn’t make life more complicated. It should make the technology work for you,” he said, noting that there’s no hard definition of what AI is.
“We’ve done a lot to make our operating system and everything intuitive, to make it easier. We put the intelligence behind it, and built that into the control system, so it’s easier for the operator to run the machine. AI is not active intervention and control. But there is a lot of intelligence behind it. So, it’s more ‘active intelligence’ than it is artificial intelligence,” he said.
At NPE, Riley showed off Uniloy’s new interactive technical manual and an online parts catalog that resembles any other online shopping portal. He, too, cited the need to employ technology to make machines simpler to use for a less-skilled workforce.
FlexBlow has seen positive customer response to its automated lamp positioning system, which stores recipes based on preform design and makes necessary adjustments during changeovers, said Lauryna Lesinske, head of customer service.
Processors also appreciate the company’s integrated leak detection and wall-thickness inspection systems and its simplified changeover process. “The idea here is to automate as many movements as possible,” Lesinske said.
“With the United States market, I see that technical talent is fading away from the plant, and customers need more and more technical support. So we tend to see that if the machine is easy to use, then anyone can use it, and everyone likes it,” she said.
ST Blowmoulding is working to make “life easier for the ones that use the machines,” said Longoni. ST’s equipment is designed to make big parts, so the company is developing automatic devices to change the heavy tooling.
“This is a specific request from customers coming because they have more and more problems finding people to work on these machines. And so we try to invent a solution that makes the job easier, and that you can attract people that actually want to do the job on the blow molding machines, especially the big machines,” said Martin Graziadei, managing partner of ST Blowmoulding.
The company’s control panels help make the machines easy to operate while enabling them to meet the needs of demanding industries like the automotive industry, Graziadei and Longioni said. Capabilities include preventive and predictive maintenance, machine monitoring and remote access. Virtual manuals are accessible via an iPad-like interface.
Rocheleau has been in business for 85 years, and customers sometimes are unaware of what its newest machines can achieve, said co-owner Cathy Rocheleau. “We were just talking to one of our customers who’s still operating a machine that they bought in 1972. Those machines didn’t have that functionality. So, like when they think of a washing machine, they’re thinking of their 1972 machine, not what we’re building in 2024.”
She and Alex Rocheleau, product development executive, said the company has worked to integrate process control, preventive maintenance, remote access and other smart functions, which improves safety in addition to its other benefits, allowing workers to “check the vitals” of the machine without going into its cabinet and putting themselves in harm’s way.
“What’s really interesting about our market in general is so many different OEMs build and design their machines for different reasons,” Alex Rocheleau said. “The markets that we really try to cater to are in the dairy field or food packaging, where some of those extra bells and whistles might not justify the cost when you’re producing monolayer products. But we’re trying to do as much as we can to make sure that the machinery is staying to a certain level of technology and satisfies the market.”
BBM is using advanced technology on its own shop floor. Hobson said BBM has partnered with a German company, Ianus Simulation, to employ AI to optimize its die head designs.
The AI program generates multiple digital twins of die heads with slight variations, and virtually tests them. The best-performing of those digital twins are selected to go through the process again, generating and testing more digital twins, in a sort of virtual survival of the fittest.
“It’ll go through all the iterations to come up with the optimized die head design for whatever material, whatever size it is, how many layers, so you don’t have to do the trial and error with steel. You can do it virtually,” Hobson said.
“It’s unique, because you can really optimize for what the customer needs,” he said, using data points to, for example, show where material would build up in an accumulator head and slow down color changes, or to test how a particular material would perform, all without having to build an actual tool to test.
Retrofitting, service for older equipment
Since blow molding machinery is famously durable, often running for decades, some OEMs touted their service programs and retrofitting capabilities at NPE.
Riley said service was Uniloy’s main focus at the show, as it has 6,000 machines in the field and the aftermarket sector makes up about two-thirds of the company’s business.
“When somebody buys a blow molding machine and our machines last 20, 30 years, you'll spend two and a half times what you spent on the machine on parts and service and upgrades and new tooling over that period. So what we’re doing is wanting to capture a much bigger market share of that,” he said.
“Sometimes a little bit of innovation goes a long way,” he added, noting that Uniloy is developing retrofit packages for its older machines to increase efficiency, cycle time and output, based on the engineering that went into the design of its new high-cavitation reciprocating machine.
W. Müller is refurbishing equipment that’s been in production 30 years or longer, exchanging parts, upgrading with easier-to-operate components like its new screen changers and building new heads “to make it run like brand-new,” Jardin said.
“Most people have a personal car. They don't run that car until it stops somewhere; they bring it to the shop for maintenance,” he said.
The company does a lot of training, Jardin said, and educates customers on the importance of keeping critical parts on the shelf; since blow molding is so highly customized and each head is designed for the article it’s blowing, a breakdown of a key part could lead to significant downtime.
ST Blowmoulding also emphasized its retrofitting packages at NPE, for its own machines and those built by competitors. Potential upgrades include control panels, extruders and other crucial components to improve performance and safety, according to the company.
New markets for blow molders
Retrofits or completely new machines are sometimes necessary to meet changing business and consumer demands. Since the rush to produce COVID-related items has receded, OEMs have noticed a trend toward larger containers for products like cooking oil and water.
Pronikova, of PET Technologies, said demand is “growing drastically” for 5-gallon water containers for dispensers, both for homes and businesses. Reasons include poor tap water quality, the cost-effectiveness of large bottles over single-serve bottles and the recycling potential of the bigger jugs, she said.
“The big ones are returnable — return and refill. They can have up to, some of them, 40 cycles,” she said, and they are made of desirable clear or blue PET that is 100 percent recyclable.
Pronikova said she is also seeing demand for plastic bottles for alcoholic beverages, as well as large containers for making wine or kombucha.
Longoni said ST Blowmoulding’s large-part machines are increasingly used in “new energy” sectors, making things like liners for hydrogen tanks for fuel cell vehicles, coolant pipes for EV batteries and solar energy components.
“For solar panels, we are selling machines to make floating docks for solar installations on the water. We already have customers,” Longoni said.
The dairy and food packaging industry remains one of the largest markets for blow molding processors, but even that market isn’t static.
Riley sees opportunity in southeast Asia, where improvements in temperature-controlled storage and transport are driving interest in fresh milk and other dairy products. “The cold chain 20 years ago didn’t exist,” he said. “If you got milk in Malaysia, it came out of a Tetra Pak box, warm.”
Several OEMs said producers of alternatives to cow’s milks often want bottles that are distinctive from the traditional containers, and in different sizes.
“There’s some dairy now that’s non-traditional, like a lot of 3-quart lactose-intolerant milk, or almond milk, all that kind of stuff that you buy in a 3-liter or a 3-quart bottle instead of a traditional gallon or half-gallon. We’ve done several projects for dairy-related things that are not your traditional standards,” Steven Rocheleau said.
His company also worked on a lot of pandemic-related products like sanitizer containers and eyedroppers for test kits. But one source of new business came as a surprise.
“There’s certainly things in blow molding in plastics that affect your life every day that you don’t think about, that never even touch your thought process,” Steven Rocheleau said.
Rocheleau was asked to develop “this odd-shaped water reservoir” for packing tape dispensers, to wet the glue before the tape is applied to countless shipping boxes for companies like Amazon.
“It’s easier to find people who need 50 million milk jugs; it’s not so easy to find the guy that needs a half a million tape dispenser reservoirs,” Steven Rocheleau said. “Thankfully, we’ve had a long, long presence in the industry, so that people might come in and say, ‘Have you ever seen this?’ Or, ‘Could you ever do this?’ And we’re very thankful to be part of it.”
Company contacts
BBM America, Mason City, Iowa, 319-883-9264, www.bbm-america.com
Bekum America Corp., Williamston, Mich., 517-655-4331, www.bekumamerica.com
FlexBlow, Kretinga, Lithuania, 370 445 51431, https://flexblow.com
Jomar Corp., Egg Harbor Township, N.J., 609-646-8000, www.jomarcorp.com
Magic North America, Whitmore Lake, Mich., 734-358-7722, www.magicnorthamerica.com
PET Technologies GmbH, Neunkirchen, Austria, 347-897-9300, www.pet-eu.com
R&B Plastics Machinery LLC, Saline, Mich., 734-429-9421, www.rbplasticsmachinery.com
Rocheleau Tool & Die Co. Inc., Fitchburg, Mass., 978-345-1723, www.rocheleautool.com
ST BlowMoulding USA LLC, Norwalk, Ohio, 567-203-6000, www.st-blowmoulding.com
Uniloy Inc., Tecumseh, Mich., 517-424-8900, www.uniloy.com
W. Müller USA Inc., Agawam, Mass., 413-787-0664, www.mullerheads.com
Lynne Sherwin | Managing Editor
Managing editor Lynne Sherwin handles day-to-day operations and coordinates production of Plastics Machinery & Manufacturing’s print magazine, website and social media presence, as well as Plastics Recycling and The Journal of Blow Molding. She also writes features, including the annual machinery buying survey. She has more than 30 years of experience in daily and magazine journalism.
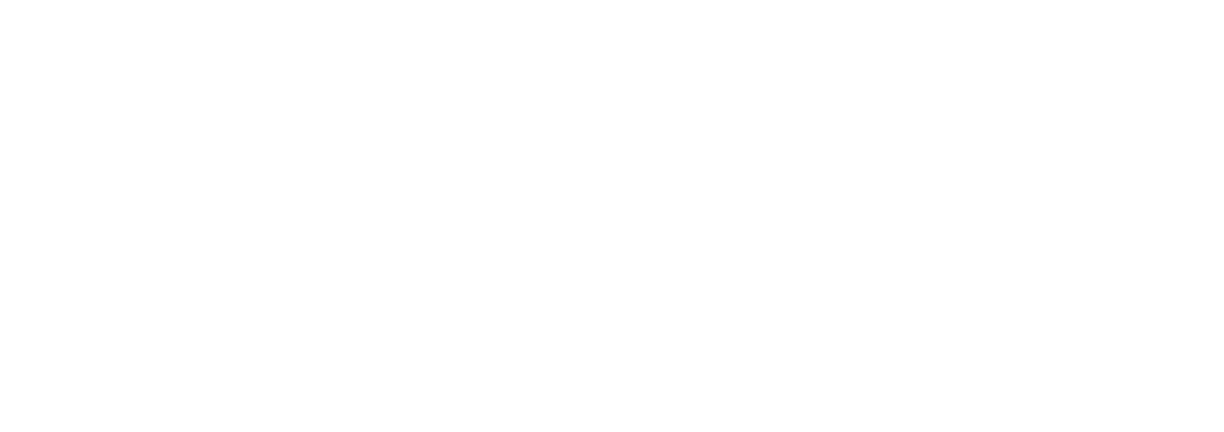