By Karen Hanna
Display screens throughout NPE showed the status of injection molding machines (IMMs), alongside, at times, pictures of the parts they were creating.
Cavitation, pressure, temperature, information from auxiliaries — all the endless streams of data were set off by three colors: red, yellow and green, with drop-down boxes offering the opportunity to further explore any of seemingly hundreds of parameters.
Welcome to “nerdy territory,” as Dana Ford, controls engineer for Wittmann’s auxiliary equipment, calls it. When it comes to injection molding machine operation, Industry 4.0 has gone mainstream.
“All this data is improving the quality of the product, the cycle time it takes to produce a product,” Ford said. “If all these people are able to make twice as many parts at half the cost, they’re going to be able to out-compete the guy that can’t use all the data.”
From trimming cycle times to optimizing the use of recycled materials, the ability to collect data and tweak production based on it offers molders many benefits, said representatives of injection molding machine makers — and molders are beginning to embrace Industry 4.0.
“I would tell you that last NPE, it was more of a buzzword, but now, it’s really taking off,” said David Sharp, divisional manager for Wittmann’s IMMs.
Overcoming fear
Reflecting their company’s motto, “It’s all Wittmann," the five injection molding work cells in the Wittmann booth exhibited a sophisticated choreography of primary machines and auxiliary equipment.
But in actual molding shops, anxiety about all that connectivity persists, said Giorgio Pigozzo, CEO of Wittmann’s digital division.
“There is a fear the cloud isn’t a safe place,” he said. Change is a hard sell and, he said, “always a painful task.”
About half of machines aren’t leveraging data, said Hannes Zach, sales director of digital solutions at Engel. He sees a lot of promise in artificial intelligence (AI) — but getting everyone on board still is a challenge, with bigger companies especially wary of the possibility of security hacks.
"From my point of view it is the complexity and huge investment of IT projects, which are the biggest challenges," he said.
Buy-in across the company is important, IMM maker representatives said.
But the systems are safe.
“You need a champion in the company for all this connectivity, and have to have your IT department involved,” Sharp said.
In the Shibaura booth, the company touted the medical molding capabilities of its new EC110SXIII IMM. The market demands a high degree of traceability, and molders can have confidence in Shibaura’s ability to protect the data, said Hemantha Wansekera, chief information officer for the company and GM for its digital services division.
Wansekera said Shibaura’s system uses three levels of security, with firewalls isolating one cell from the next. Rather than being on the World Wide Web — which seems to be the fear of skeptics — the data resides on a private cloud managed by Shibaura.
He reiterated a message many IMM makers expressed: Your data is safe with us.
“Nine out of 10 times, we can actually win the argument because we can prove our system is secure,” he said.
Tackling complexity
One possible reason some molders are reluctant to dive into Industry 4.0 is its complexity. But IMM maker representatives say they’re prioritizing ease of use. Throughout NPE, manufacturers — such as Boy, Chen Hsong, Haitian, LS MTron, Nissei, Sodick and Wittmann — touted new or optimized controls, and talked about how users of their machines can access their expertise.
Like many other IMM representatives, Steven Ross, senior manager of strategic sales and marketing sales for Sumitomo, stressed his company’s partnerships with its customers and other suppliers. Rather than defining Industry 4.0 for its customers, he said, Sumitomo is listening to molders about what they want and need.
“Ultimately, the goal is we can't make it more difficult for customers to buy our equipment,” he said. “We want to make it as easy as possible.”
To that end, many companies continue to upgrade their controllers.
For example, Boy is updating its Procan Alpha 4 control system to the Procan Alpha 6. Its Operational Data Acquisition software assesses data from the control, allowing the system to cover three areas: production planning and control, quality control and operating cost control.
Users can access the system through personal devices, such as cell phones and tablets.
“The ability to access a Boy injection molding machine from anywhere, around the clock, during ongoing production, is particularly advantageous for employees in a two- or three-shift operation,” said Thomas Kühr, head of electrical design for Boy. “However, this access is not limited to machine operators alone. Other departments such as production planning, purchasing, costing, etc., directly benefit from the data of the ODA system.”
Ease of integration was a central theme for Wittmann.
To simplify programming and robot use, the company introduced its Control Room technology, which comes in two versions: the Control Room TeachBox, which provides connectivity with an injection molding machine through the controller of the Wittmann robot that tends to it; and a PC-based version that allows all Wittmann-compatible equipment to be networked within a plant. The PC-based Control Room TeachBox provides connectivity across the plant, according to Jason Long, VP of sales for Wittmann USA.
“This allows the customer access to all their Wittmann-connected equipment through the customer’s PC,” Long said. “They could even get remote access, if the customer has the remote access to their plant network. The Control Room PC application also has an option to allow remote access for Wittmann service to help troubleshoot any Wittmann equipment connected to the Control Room software, through industry standard web access tools, like WebEx.”
Tools available from Wittmann reduce the need for programming that once would have taken hours. Now, preparing a robot can take just minutes, Long said.
As Pigozzo quipped, users aren’t “rocket scientists.” But they are familiar with social media like Facebook and Instagram — and the usabilty of those interfaces is something Wittmann is trying to emulate.
Meanwhile, in LS Mtron’s booth, company leaders spoke with optimism about the company’s prospects — they're looking to see their share of the American market explode to 20 percent over the next few years.
LS Mtron’s 1,400-ton One-series IMM made a piece of rear door side trim for a Hyundai vehicle in the company’s booth, the biggest at the show with an injection molding focus. According to the company, the IMM’s controller allows users to customize their system and collect data on injection actions, and provides increased transparency. It offers easy cycle analysis and unit conversion, as well as a memo function that lets users associate that data to a specific mold.
“What we’re able to do is to be able to be on the front end of Industry 4.0,” said Paul Caprio, president of sales of LS Mtron Injection Molding Machine USA.
Maintenance by remote
At a time when many molders have struggled to find workers, IMM maker representatives stressed that with Industry 4.0 capabilities, access to expert help always is at the ready.
“One of the biggest things that we feel that is on every customer's mind, every time we visit a customer, anytime they visit us, is the labor shortage,” said Vanessa Malena, who was attending NPE for the first time in her new role as president of Engel North America. “And, so, we really want to tell our customers the story here in NPE, and really show them what Engel has done to support them, because they can’t always support themselves. ... It’s really the training, the service team, the digitalization and the automation to support our customers.”
The company’s portfolio of digital solutions spans the gamut, she said, from part design all the way to the recapture of value from products at the end of their life, along with access to maintenance assistance.
Access to support was a selling point for Milacron, too, as it demonstrated its M-Powered technology, a portfolio of observational, analytical and support services, available for free with new machines for the first 12 months of ownership. Leveraging real-time machine data, it connects users with support regarding parts, service, rebuilds, retrofit and preventative maintenance.
To help its users, Arburg is looking to further incorporate AI for monitoring variables such as viscosity.
It touted its digital tools at a booth that drew constant crowds, thanks to its giveaway — a molded box for tools of a more traditional variety. Its arburgXworld customer portal features its new Ask Arburg app, which can answer specific questions about machines and processes as well as identify and rectify problems — with no need for on-site service.
According to Martin Baumann, who like Malena was attending NPE for the first time in a new role — as president and CEO of Arburg Inc. — a company survey revealed an average increase in overall equipment effectiveness of over 26 percent among 200 users of ALS, Arburg’s hos computer system MES. The company released the newest version, ALS 8.0, in March.
Going green
While video displayed molding operations in real time, it was men and women in bright yellow shirts charged with collecting waste recycling who brought home one of the most important messages at NPE — that plastics can be sustainable.
For Wittmann’s Sharp, who acknowledged sensitivity to the criticisms levied against the plastics industry, it’s where “nerdy territory” offers a beachhead to do better.
“We work in the plastics industry. The name for plastics is terrible, and we really want to be in the forefront of changing the name for plastics,” he said, as he discussed how his company’s HiQ-Flow software can help machines compensate for variances in material characteristics — a feature that allows them to use more recycled material.
On every machine in its booth, Wittmann’s ImagoXt software provided energy measurements.
Meanwhile, Shibaura’s Wansekera touted one of his company’s new features — an app to track the carbon footprint of each part users make.
An automotive-supply-chain customer told him that energy costs and government regulations amplify the need for the app.
“Most customers struggle with it. There’s no system for measuring your CO2,” Wansekera said.
Hundreds of data points once out of reach from molders now are a click away, he and other IMM maker representatives showed as they swiped left and right on screens throughout the NPE.
That visibility of data gives users an edge, they said.
“As long as I’ve been in the business, they’ve always talked about, but never used it,” LS Mtron’s Caprio said. But things are changing now, as molders realize they’ll need to embrace Industry 4.0 to compete. “The only thing I know is if you don’t have it, you’re going to get passed by on an order.”
Contact:
Arburg, Rocky Hill, Conn., 860-667-6500, www.arburg.com/en/us
Boy Machines Inc., Exton, Pa., 610-363-9121, www.boymachines.com
Engel Machinery Inc., York, Pa., 717-764-6818, www.engelglobal.com
LS Mtron Injection Molding Machine USA, Duluth, Ga., 470-724-2263, www.lsinjection.com/us
Milacron LLC, Batavia, Ohio, 513-536-2000, www.milacron.com
Shibaura Machine Co. America, Elk Grove Village, Ill., 844-905-3981, www.shibaura-machine.com
Sumitomo (SHI) Demag, Suwanee, Ga., 678-892-7900, www.sumitomo-shi-demag.us
Wittmann USA Inc., Torrington, Conn., 860-496-9603, www.wittmann-group.com/en/usa
Karen Hanna | Senior Staff Reporter
Senior Staff Reporter Karen Hanna covers injection molding, molds and tooling, processors, workforce and other topics, and writes features including In Other Words and Problem Solved for Plastics Machinery & Manufacturing, Plastics Recycling and The Journal of Blow Molding. She has more than 15 years of experience in daily and magazine journalism.
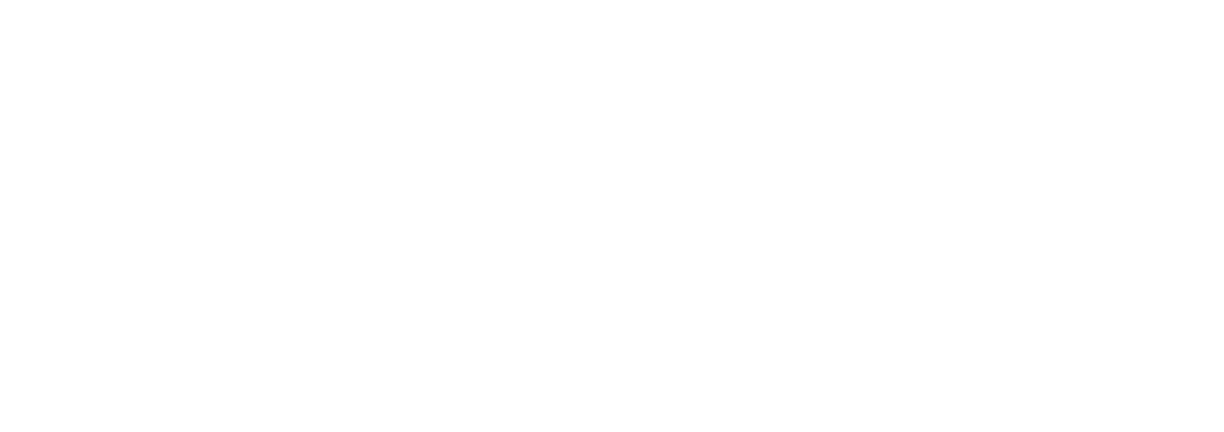