By Bruce Geiselman
Manufacturing companies are incorporating collaborative robots into their operations as they look for ways to compensate for a shrinking labor force and rising labor costs.
Plastics Machinery & Manufacturing looked at three companies — Westec Plastics Corp., Delphon and Allied Moulded Products Inc. — that recently have added cobots to their operations.
While Allied purchased its cobot and ActiNav bin-picking kit from cobot giant Universal Robots (UR), Westec and Delphon are customers of newcomer Rapid Robotics and its unique subscription model.
Westec
Custom injection molder Westec has had so much success with its three cobots that it plans to add two more soon. Company President Tammy Barras credits them with helping secure a new contract that will significantly increase production.
The Rapid Machine Operator (RMO) cobots from Rapid Robotics allow the Livermore, Calif., custom injection molder to competitively bid against molders elsewhere in the country where labor costs are lower. The biggest advantage of the cobots is cost reduction, Barras said.
“Labor is expensive and keeping customers satisfied with their pricing structure is always a challenge regardless of whether you’re in Ohio or California,” Barras said. “By operating some of the simpler tasks, we could redeploy our operators on other tasks that a cobot would not be able to handle.
The company, which has 23 presses, added the cobots to its workforce in 2020. The workers have given the cobots names, finding it easier to identify the different machines. Melvin has been programmed to operate a hot stamping machine. It picks up an injection molded part from a conveyor belt, puts it into a hot stamping machine where a logo is applied and then places the part onto another conveyor.
Kim operates a pad printing machine used on a variety of products for different customers.
Nancy is used for packaging. It picks up the assembled final product, weighs it to ensure that all of the components are inside the box, closes the box with tape and puts it into a shipping container.
One of Westec’s customers is AeroPress, for which it manufactures a French press-like coffee maker. It has been a client for over 30 years. Westec recently landed a new contract with AeroPress after it was able to underbid another injection molder based in the Midwest. Automation allowed Westec to keep its labor costs low enough to successfully compete, Barras said.
Consequently, Westec will be adding more automation.
“We are working on bringing in an additional two [cobots],” Barras said. “One of our major customers has actually been seeing significant growth. So, we’re working on building a larger tool, going from a four-cavity to an eight-cavity tool, which will increase our need for cobots to help handle that extra capacity ... Melvin can only keep up with four pieces at a time. When we increase to an eight-cavity tool, we’ll need to have two cobots doing the hot stamping to keep up with the production off of the mold.”
The second new cobot — the fifth overall — will be used for packaging.
Each cobot is leased from Rapid Robotics for about $25,000 per year and can do the work of three employees because it can work 24 hours per day. Each employee Westec hires costs between $35,000 and $45,000 annually. The cobots deliver a quick return on investment, Barras said.
They have proved particularly valuable during the pandemic, she said.
“They absolutely turned out to be more valuable because they don’t call in sick, for one,” Barras said. “No. 2, long-term, we’ve struggled to maintain enough operators to keep our full production floor running. It’s great to know that I’ve got the cobot there every day, and I can rely on that cobot to be there and use the operators that we have to run other jobs.”
Leasing made adding the automation possible, Barras said. The company simply couldn’t afford the costs associated with buying and installing traditional industry robots that require significant safety equipment and lack the flexibility to physically change locations and perform different tasks.
“Historically, when you automate a cell, you automate it for that program only,” she said. “Typically, it would be $100,000 to $200,000 to automate that cell. In the past, we were never able to use automation because it was cost-prohibitive for a custom injection molder. Being able to rent them really opened up a lot of possibilities for us.”
Delphon
Delphon, a San Francisco Bay-area company that specializes in engineered polymer and adhesives solutions for the semiconductor, photonics, medical and electronics industries, in the past two years installed four cobots from Rapid Robotics.
Pradeep Mishra, director of manufacturing engineering at Delphon, told Plastics Machinery & Manufacturing that the Rapid Machine Operators (RMOs) helped the company reduce expenses, cope with a labor shortage in the Bay Area, and improve worker safety during the pandemic by allowing employees to remain socially distanced.
Delphon’s TouchMark pad printing division was the first to install a pair of RMOs to operate two pad printing machines. TouchMark’s automation project was so successful that a short time later, its sister division, Gel-Pak, started using them to clean injection molded parts with ionized air knives prior to assembly.
Delphon estimates that each of the RMOs achieves greater than a $70,000 return on investment per year, Mishra said.
TouchMark had been considering robotic automation for some time, but the economics never made sense because the robots came with a huge upfront cost. However, the subscription business model from Rapid Robotics, which costs $2,100 per month, made for an attractive return on investment, Mishra said.
“One of the challenges we always have, as a mid-cap manufacturing company, is we don’t have a lot of resources to develop an automation solution,” Mishra said.
Acquiring robots under a monthly subscription plan eliminated the need for a large upfront capital expenditure, he said. In addition, the cobots could be installed faster than traditional industrial robots. The first was installed and running in less than one week.
The Rapid Robotics cobots arrived ready to work with built-in vision systems and artificial intelligence trained to operate the kinds of machines TouchMark uses. They need only light supervision from an operator.
TouchMark, which initially leased one RMO and quickly added a second, put the cobots to work operating pad printers that apply a pressure-sensitive adhesive to injection molded plastic trays designed for semiconductor packaging. They grab trays stacked by a human and place them one-by-one into a pad printing machine. The RMO then activates the pad printer, which applies the pressure-sensitive adhesive. Once the adhesive is applied, the RMO removes the tray from the machine and starts the process over again.
TouchMark previously assigned an operator to each pad printing machine. Now it needs only one employee to supervise both RMOs while operating a third pad printing machine at the same time. The other two operators were reassigned to different duties.
With the two RMOs in place, TouchMark quickly began saving $15,640 per month as compared to using human workers, Mishra said. The RMOs worked at the same rate, hour by hour, day by day, unaffected by breaks, sick days and paid time off.
Gel-Pak's use of RMOs to clean molded plastic trays saves the company about $20,400 per month, Mishra said.
While the company currently uses four RMOs, it’s considering installing more, Mishra said.
“We see there are lots of opportunities down the line where we see this RMO can be further applied,” Mishra said.
He said the company might apply the RMOs to the same product line or to different product lines.
“The reason is the fast integration, the low upfront cost and the subscription model,” he said.
Allied Moulded Products
Allied Moulded Products, a full-service injection molding operation manufacturing non-metallic electrical boxes and enclosures, struggled with a labor shortage about two years ago.
The Bryan, Ohio, company, which also performs compression molding and resin transfer molding, installed the ActiNav system from UR to automate the picking of parts out of deep bins. The installation allowed Allied to reduce overtime expenses, move existing workers to more ergonomic tasks and improve consistency, according to a white paper from UR.
Allied also found that manual labor produced inconsistent results. Toward the end of the day, production would decline as workers got tired, UR said.
In addition, with the arrival of the pandemic in 2020, the company knew that its employees at any time might not be at work for reasons beyond their control.
Allied wanted a bin-picking system with a small footprint. The company had been looking into bin-picking systems for some time, but other systems were either too slow or required intrusive guarding.
“Floor space here at Allied is pretty limited already, and the thought of having to put up more guarding to accommodate a robot was one of the things that held us back initially,” Nate Gilbert, Allied’s manufacturing engineer technician, said in the paper. “But with collaborative robots being safe around employees, we felt that was a great way to go.”
The ActiNav system incorporates a UR5e or UR10e cobot with an Autonomous Motion Module, ActiNav user-interface software and a choice of 3D sensors.
The process begins with workers unloading a crate of parts into a dumpster that then dumps them into the ActiNav bin. The cobot picks up the parts — extruded fiberglass electric junction box housings — and places them in proper orientation onto a narrow, railed conveyor.
The system must make some decisions autonomously, such as which part to pick, how to place it in the correct orientation and how to identify incorrect parts, place them aside, and continue with its main task.
As long as its bin is full, the ActiNav system can go all day without operator intervention, according to UR.
Contact
Rapid Robotics, San Francisco, www.rapidrobotics.com
Universal Robots USA Inc., Boston, 844-462-6268, www.universal-robots.com
More on automation
Automation is on every manufacturer’s mind these days, or it should be. There’s more to our Cover Story:
• Processors hustling to add more robots to their mix. https://plasticsmachinerymanufacturing.com/21258332
• Worker shortage, advancements in technology fuel cobot sales. https://plasticsmachinerymanufacturing.com/21257916
• Veteran manufacturer of EAOT says automation is now accessible to anyone. https://plasticsmachinerymanufacturing.com/21256653
• A project manager or integrator can help make your robot installation a success. https://plasticsmachinerymanufacturing.com/21258310
• The future is automated, according to Jeff Burnstein, president of the Association for Advancing Automation. https://plasticsmachinerymanufacturing.com/21256667
• Robots don’t kill jobs; they free humans to move into better ones, experts say. https://plasticsmachinerymanufacturing.com/21258504
• A cobot industry analyst predicts strong growth will continue. https://plasticsmachinerymanufacturing.com/21258134
• Rapid Robotics’ subscriptions offer an affordable way to start automating your plant. https://plasticsmachinerymanufacturing.com/21258285
• Yaskawa enhances features on two new products. https://plasticsmachinerymanufacturing.com/21256712
• Epson’s easy programming lowers the barrier to entry. https://plasticsmachinerymanufacturing.com/21258503
Bruce Geiselman
Senior Staff Reporter Bruce Geiselman covers extrusion, blow molding, additive manufacturing, automation and end markets including automotive and packaging. He also writes features, including In Other Words and Problem Solved, for Plastics Machinery & Manufacturing, Plastics Recycling and The Journal of Blow Molding. He has extensive experience in daily and magazine journalism.
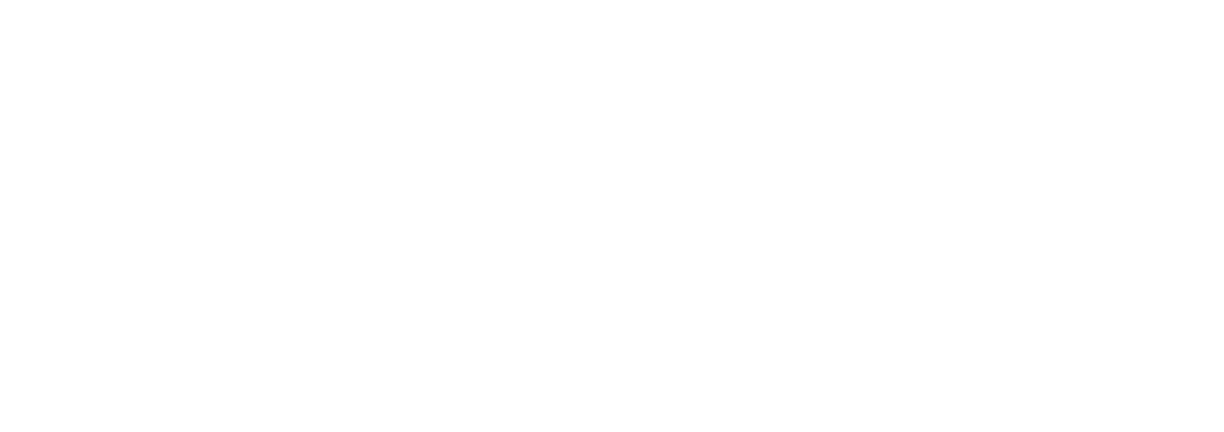