By Bruce Geiselman
Yaskawa in January unveiled two six-axis collaborative robots appropriate for a variety of plastics processing-related tasks, such as assembly, dispensing, machine tending, material handling and packaging.
The HC10DTP and the HC20DTP cobots are the newest additions to Yakawa’s HC series. They are similar to existing HC-series cobots (the HC10XP and HC20XP), but with several enhancements.
“We’ve added some cool features to it that make it, we believe, a little bit more marketable and, perhaps, a little bit more universal in nature,” said Dean Elkins, segment leader for material handling at Yaskawa Motoman. “The first thing that we’ve done is added ISO-standard tooling plates to them.”
The ISO-standard tooling plate, also known as a tool flange, allows for easy and quick end-of-arm-tooling (EOAT) changes because it is compatible with grippers and other end effectors from a variety of manufacturers. Previous HC models have a proprietary bolt-hole pattern for the end-of-arm tooling.
“We’ve gone to a universal bolt-hole pattern, an ISO bolt-hole pattern, that allows for fast interchange, and ease of use in terms of compatibility with third-party grippers from a mounting standpoint,” Elkins said.
The DTP cobots also have a larger range of movement.
“We’ve expanded the motion of the arm itself,” Elkins said. “Some of the internal components have been modified to allow for a wider range of motion of the robot, which is a performance enhancement.”
Another improvement is the incorporation of a better utilities package into the cobot arm, which eliminates the need for running external lines along the arm. A through-the-arm, Category Six Ethernet cable allows for communications connectivity between the EOAT and other equipment.
“It’s an easier package to connect to external devices than ever before,” Elkins said.
The new models also incorporate two 5mm airlines that run through the arm.
The HC10DTP and the HC20DTP are capable of hand-guided programming, which allows users to direct teach points without a pendant, according to Yaskawa. The cobots’ electrical connections simplify plug-and-play operation.
Power and force limiting (PFL) technology helps the HC10DTP and the HC20DTP work safely alongside humans. PFL technology constantly monitors force to quickly and safely detect contact, such as with a person, to stop movement and prevent injury. The design also eliminates pinch points for improved safety.
The cobots’ cast aluminum bodies are IP67-rated and can be used in damp or splash-prone environments, the company said. The bodies are easy to clean and suitable for use in sanitary environments where wiping or washing are required. NSF H1 certified food-grade grease is standard, which allows their use where there is a possibility of incidental food contact, Yaskawa said.
Each robot can shift between collaborative speed in PFL mode or full speed in industrial mode, optimizing cycle times based on risk assessment and process requirements, the company said.
The HC10DTP has a 22-pound payload capacity, a 4.5-foot maximum reach, a 3.9-foot effective reach and repeatability of plus or minus 0.05mm. The HC20DTP has a 44.9-pound payload capacity, a 6.2-foot maximum reach, a 5.6-foot effective reach and repeatability of plus or minus 0.05mm. The HC20DTP cobot, when equipped with an appropriate-sized riser, is capable of loading or unloading a pallet measuring 3.3 feet by 4 feet loaded up to 6.7 feet high, without the need for an elevator.
Both cobots are controlled by a YRC1000 controller, which does not require a transformer for input voltages ranging from 380VAC to 480VAC. The YRC1000 has a compact cabinet measuring about 2 feet wide by 1.6 feet high by 1.4 feet deep and uses a standard lightweight teach pendant with intuitive programming. The Smart Pendant featuring Smart Frame patented technology is available as an option.
Contact
Yaskawa America Inc., Motoman Robotics Division, Miamisburg, Ohio, 937-847-6200, www.motoman.com
Bruce Geiselman
Senior Staff Reporter Bruce Geiselman covers extrusion, blow molding, additive manufacturing, automation and end markets including automotive and packaging. He also writes features, including In Other Words and Problem Solved, for Plastics Machinery & Manufacturing, Plastics Recycling and The Journal of Blow Molding. He has extensive experience in daily and magazine journalism.
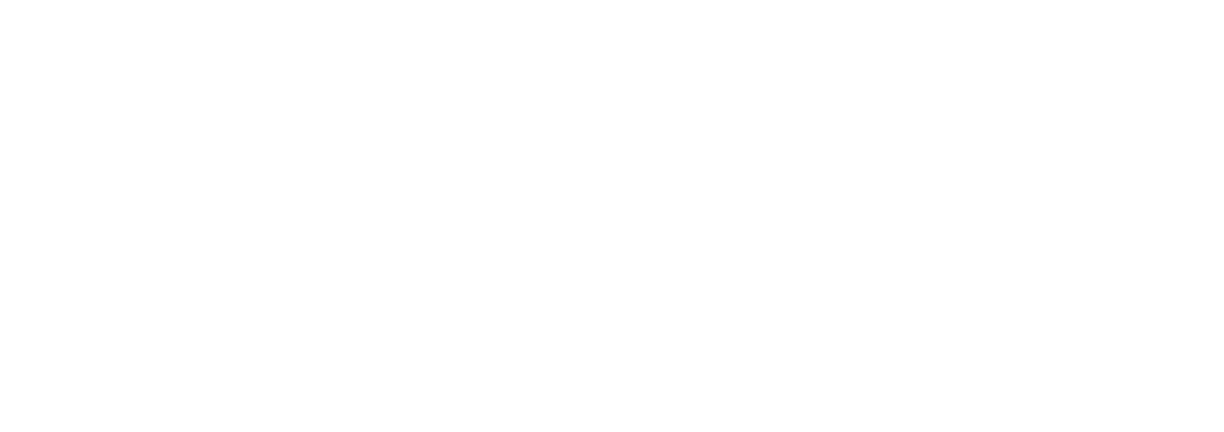