As the president and GM of a company that makes end-of-arm tooling (EOAT), Robert Little has his hands in a lot of industries — and his eyes on the future. Over the years, he has borne witness as companies exported jobs, but now believes, with the help of automation, work is coming back — especially in the plastics industry, which was particularly affected by the offshoring trend.
Nearly 40 years after he and others founded ATI Industrial Automation, Little is encouraging companies that haven’t yet made a major move into the automation realm to invest now. The technologies have become easier to use and labor shortages have made them indispensable, said Little, who discussed his outlook on robots and automation with Plastics Machinery & Manufacturing Senior Staff Reporter Karen Hanna.
How important is the plastics industry to ATI?
Little: Injection molding has been a huge part of our business and has been for decades. It is one of the early adopters of robotics.
Collaborative [robot technology] opens up better potential for the plastics industry, because now the robots can be placed in areas [where] before there wasn’t space for them, or people can buy them and program them, so they don’t have to pay for a high-performance programmer. It’s actually reduced the cost of integration, and it’s allowed robots to work closer with people.
What advice would you give to company leaders who might feel behind the curve in automation adoption?
Little: The companies that are creating these systems have gotten better at what they’re doing. So, it’s like this: Somebody says, “I don’t use smartphones.” And then one day, they say, “You know, I think about using a smartphone.” Well, they don’t have to be one of those people using an iPhone 4; they can use the new iPhone 13. All of a sudden, all those applications and ease-of-use [advancements], all of that has been designed for them. So, the best thing I can say is that not being an early adopter, you’re not going to be really behind the curve; the curve is catching up to you. The robotics industry is designing systems for people who are not early adopters.
If ... you don’t have any robots in your line, and it’s clear to you that automation has started to make sense … [in] simple conversations with a robot manufacturer or robotic integrator … they can say, “Hey, based on our experience of the current technology, here’s where we think you’ll have the ability to be more productive, save money, save time, make a better product.”
It’s not ever too late to jump on the bandwagon.
Little: I came out of the University of Pittsburgh with a mechanical engineering degree, back in the ’80s. And when I was interviewing for a position, I saw there was a robot lab at, of all places, Kodak. And I was just enamored by it. I asked the people who were hiring at Kodak, “Would I be able to work in the robot lab?” They said, “No.” I was really disappointed by that, so I didn’t take the job, and I ended up taking a job with Lord Corp. We built robotic end-effectors. But then, in the late ’80s, there was a downturn in the robotics market. Our corporation sold the division to a handful of employees, and I was one of them, and ATI Industrial Automation was formed. Our focus was the development of robotic end-effectors, to make robots better.
The company recently has a new owner, Novanta.
Because of our company’s position and robotics network, we actually get to see all of the various robot applications that are occurring throughout the world. Because of that, we have a really good vision of what’s going on in the robotics field.
What trends are you seeing in terms of the industries using automation?
Little: The robot market has been moving in lockstep with the automotive market. If the automotive market has a cold, the robot market has the flu. And if the automotive market is surging, the robot market is surging even higher.
We are changing the way we make cars. The electrification of vehicles is going to be an enormous disruption to the entire manufacturing world. We are not going to make engines, but we’re going to make batteries. We’re not going to make transmissions, but we’re going to make electric motors. There is going to be a huge change. We’re just at the beginning of that.
That is an absolutely huge market in general, not just for robots, but for all of manufacturing.
The automotive market still needs robots more than ever, but the rest of the market that’s outside the automotive area is growing. An example of that is warehouse automation. There's been this huge trend to automate warehouses, and robots are part of that. They're not the only solution, believe me. But robots, obviously because of their flexibility, have a fantastic role in the future of automation. So, logistics is a huge, but not the only, growth area that's really starting to expand rapidly.
The other thing is [using automation in] old industries like arc welding. That arc welding has become very disruptive right now, with the advancements in ease of use or potentially artificial intelligence.
The other one that’s not big, but it’s disruptive, is robotic surgery. It’s a safer way to have surgery done. It’s more repetitive, and you want repetitive when it comes to how the surgery’s done. It gives the surgeons an ability to do a surgery safer, faster and less expensive.
How are the technologies themselves evolving?
Little: There’s been a big push in what I call simplification, making the robot applications easier to use, and that trend has [made] a major difference. It’s allowed smaller companies to get into robotics, where before there was kind of a barrier. Because it wasn't just the price of the robot to get the application; it was the programming of that robot that was difficult to do.
If you could buy a robot, and a high school student can go in there and start programming it, you have opened up a Pandora’s box of potential.
If you have a robot working with no fences, minimal safety devices, because the safety devices are built into the robot, that’s a cost savings and it’s a space savings. And that’s another thing reducing the entry barrier, which is why the smaller companies are starting to purchase [collaborative] robots.
What is ATI working on?
Little: We have two product lines that we’re seeing huge growth in right now. One is our six-axis force-torque sensor. It gives a robot the ability to touch and feel something. It’s starting to give robots the ability, through sensors, to make decisions, just by touch.
[There] is excellent data that robots are starting to use to be able to do more advanced applications.
The force-torque sensor is part of a bigger plan. There’s been a lot of discussion about the future of artificial intelligence and its implementation into the robotics field. If the robot has sensorial feedback, what can we do with that? Can the robot learn its application and apply, through the sensor-feedback mechanism, can it make decisions on what it should do next, and learn from it?
We’re all used to having to make 100,000 widgets. Well, what if we only had to make 1,000 widgets of Type A; 1,000 of Type B; 1,000 of Type C? How can a robot handle all this change? There’s a lot the robot has to know and learn; there’s only so much you can program. But if the robot had the ability to scan its environment and make a decision without a person having to come in and program, that [allows] so much more variety, and [you don’t have to] purchase robots for the 100,000 widgets, which is kind of a 1920s-assembly-line approach.
We are seeing some of that. There’s a lot of companies who are doing it, but the success rate is going to be slow.
I was talking to a vision company, and they said that they got their vision systems such that they could [recognize] defects in a car paint system. The vision system would look at the car, identify the paint defects and then categorize them from a list of 500 types of defects. From the 500 defects, it would take that information and have a plan how to fix it.
[Our] other product line is a material-removal product line. In the plastics industry, we have tools that will go on the arm of the robot that will allow you to trim off the plastic edge from [parts].
If you’re trimming, and you have enough sensorial feedback, and the robot can learn, they can maybe trim more exactly, faster.
The people who are doing these finishing jobs, either they have to have it done in a very low-cost area like Southeast Asia, or they have to figure out, “How do I automate it so that I minimize the amount of time people have to spend trimming?”
We’re seeing a lot of adoption of our tooling to do more trimming. There’s sanding and deburring and grinding. People don’t want those jobs. I mean, they’re tedious, they’re hard, and actually, they’re not always that safe.
How does the shortage of people skilled with robotics influence their evolution and adoption?
Little: Getting skilled labor has become more and more difficult as time has gone on. But the key that robots give us is the ability to free up jobs, so that the people we free up can go to a higher skill level. [The industry can] train the labor force to take on a more advanced role, not to be the person at the end of the line, cutting and trimming, but [to] be the person who’s a technician, who’s monitoring the machinery and doing repairs of the machinery, or writing the code, or teaching the machinery how to get the problem solved.
What effect does the increasing integration of automation have on workers?
Little: There is a trend that’s been going on since COVID, where it’s a reshoring effort, where we’re starting to bring some manufacturing back to North America, from Southeast Asia or China because a lot of manufacturers are finding that they need to be more local.
[Automation] has the ability to bring work that was overseas back to the U.S.A., back to Europe, back to a local environment. And the robots are succeeding in that. A strong robot market means a strong manufacturing [market]. And a strong manufacturing [market] means more labor. That labor is tending to be higher-paid and more skilled than the labor from 20 years ago. This is a huge benefit for all of us. It brings jobs back to the local environment. It brings higher-paid positions potentially.
It gives you back more of a local manufacturing base; it gives you more security for the future. It’s a huge win.
Before working with robots, you were an active-duty soldier from 1977 to 1981, serving as a paratrooper in the U.S. Army’s 82nd Airborne. How did that experience shape you?
Little: It had a huge effect on how I look at the world.
When we set up a defensive position, we would dig in; we would place these barriers directly in front of us. The only way we could fire out from our dugout was we fired in front of our neighbor’s dugout; we were covering our neighbors, but not covering ourselves.
Once you realize your success is totally built on somebody else succeeding, you’ll realize, “Hey, I better start caring about the other person.” And that is the key in a corporation, a team.
It’s all about caring. Do you care about your customer? Do you care about your fellow employee who’s working in a different department?
How would you like to be remembered?
Little: This is going to sound weird, but I don’t want people to remember me. When I leave, what I want them to remember is what they’ve accomplished. he best thing that could happen is that the company and the technology and the customers live on in such a manner that they don’t know Robert Little, nor do they care. They just know what they’re using and that they love it. If one day I were to go back to visit the company or my customers, far after I’ve retired, they wouldn’t know me. But I would recognize the technology, and I’d recognize how they’re using it. And that would make me happy.
WHO IS HE: Robert Little
AGE: 64 (in mid March)
TITLE: President and GM of ATI Industrial Automation Inc.
COMPANY LOCATION: Apex, N.C.
COMPANY’S FOUNDING: 1989
EMPLOYEES: 2,800 at Novanta Inc., which owns ATI; more than 370 at ATI, where Little works
PROFESSIONAL AFFILIATIONS: Elected in 2019 to the board of the Robotic Industries Association, which is now part of the Association for Advancing Automation (A3); elected in January 2022 to A3’s Robotic Technology Strategy Board
More on automation
Automation is on every manufacturer’s mind these days, or it should be. There’s more to our Cover Story:
• Processors hustling to add more robots to their mix. https://plasticsmachinerymanufacturing.com/21258332
• Worker shortage, advancements in technology fuel cobot sales. https://plasticsmachinerymanufacturing.com/21257916
• A project manager or integrator can help make your robot installation a success. https://plasticsmachinerymanufacturing.com/21258310
• The future is automated, according to Jeff Burnstein, president of the Association for Advancing Automation. https://plasticsmachinerymanufacturing.com/21256667
• Robots don’t kill jobs; they free humans to move into better ones, experts say. https://plasticsmachinerymanufacturing.com/21258504
• A cobot industry analyst predicts strong growth will continue. https://plasticsmachinerymanufacturing.com/21258134
• Rapid Robotics’ subscriptions offer an affordable way to start automating your plant. https://plasticsmachinerymanufacturing.com/21258285
• Yaskawa enhances features on two new products. https://plasticsmachinerymanufacturing.com/21256712
• Epson’s easy programming lowers the barrier to entry. https://plasticsmachinerymanufacturing.com/21258503
• Three case studies show cobots’ versatility. https://plasticsmachinerymanufacturing.com/21258453
Karen Hanna | Senior Staff Reporter
Senior Staff Reporter Karen Hanna covers injection molding, molds and tooling, processors, workforce and other topics, and writes features including In Other Words and Problem Solved for Plastics Machinery & Manufacturing, Plastics Recycling and The Journal of Blow Molding. She has more than 15 years of experience in daily and magazine journalism.
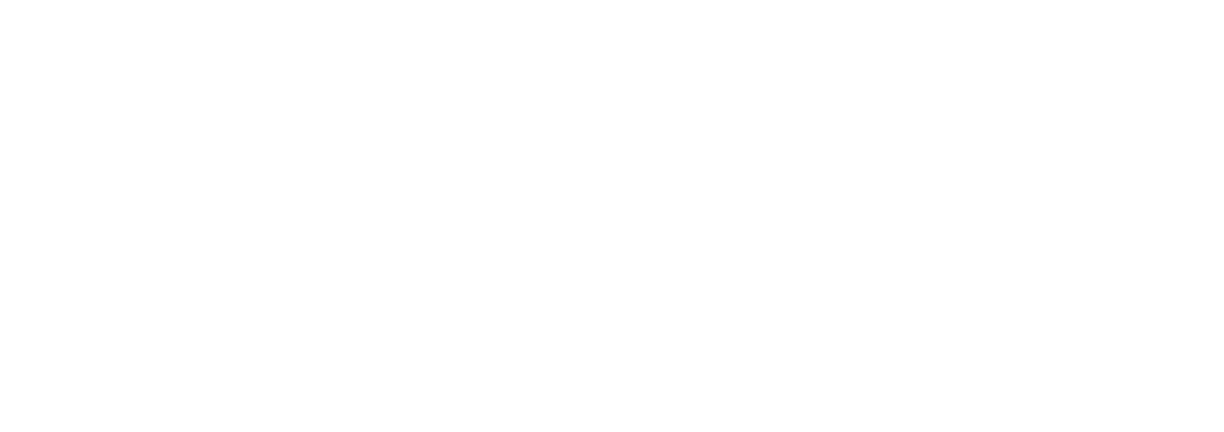