By Brian Taylor
Stadler Anlagenbau GmbH, in collaboration with fellow German technology provider Krones, has designed and installed much of the equipment at the new Republic Services Polymer Center in Las Vegas.
The facility processes plastic bottles, jugs and containers to produce recycled-content plastic materials ready for use in new packaging, according to Stadler, noting the plant is the first of its kind in North America. The new facility has been designed to produce more than 50,000 tons per year of recycled-content resin.
Krones, a packaging production and recycling systems provider, acted as general contractor for the project in Las Vegas. Krones worked hand in hand with Stadler, which was responsible for mechanical sorting on the polyethylene terephthalate (PET) and polyolefins lines.
The new Polymer Center receives plastics collected by Republic Services in the western United States to recover PET, which is converted into recycled PET (rPET) flakes that can be turned into new bottles and polyolefins that are reprocessed for use in the production of new bottles, jugs and containers.
“The Polymer Center is the first facility of its kind in North America,” says Pete Keller, vice president at Phoenix-based Republic Services. “It’s the first time a single U.S. company has managed the entire plastics recycling stream, from curbside collection to production of high-quality recycled resins ready for use in sustainable packaging.”
The Republic Services project in Las Vegas required careful planning and research to select the best partners.
“We started to think about the Polymer Center business model in 2019,” Keller says. “We chose Stadler and Krones because we think we’re going to produce the highest quality and highest-value product in the marketplace. We had familiarity with Stadler’s equipment and people, and we knew we were going to get a solid design.
“We consistently heard that the Krones wash line produced the highest-quality rPET flake in the marketplace. These systems give us the ability to produce both food-grade and color-sorted materials in a way that hasn’t been available to the market in the past, enabling greater material circularity.”
The Polymer Center in Las Vegas sorts and processes materials, which are delivered in bales, on two lines: one for PET and one for mixed plastics. Each line has a capacity of 5 tons per hour.
“This is the largest dual-line plastics recycling plant in the U.S.,” says Mat Everhart, CEO of the Colfax, North Carolina-based Stadler America LLC subsidiary of Stadler Anlagenbau GmbH.
At the plant, the materials fed into the PET line undergo mechanical separation and the identified PET is cleaned of ferrous particles. A Stadler STT2000 ballistic separator sorts the material into rolling, or 3D, flat and fines fractions.
The fractions go through sensor-based sorting with near-infrared (NIR) sorters. Caps, rings and flat fractions go to compactors, while the 3D fractions are directed to a Stadler Label Remover to undergo that process. The clear PET, caps and rings are directed to the Krones washing line, which granulates and cleans the material, while the colored PET is compacted into bales.
On the mixed plastics line, mechanical separation sorts the infeed into fines and sieve overflow—the latter further separated into light and heavy fractions. The heavy mixed plastics fraction is sorted into four polyethylene (PE) products—natural, white, red/orange/yellow and other colors—and two polypropylene (PP) products—natural/white and other/color.
PET is sorted out of the remaining material and sent to the PET line. The products off the mixed plastics line are conveyed to storage bunkers where a semiautomatic feeding program allows materials to be discharged by grade and fed into the baler.
According to Keller, the Polymer Center in Las Vegas is part of Republic Services’ plans for a nationwide network to help customers achieve a true plastics circular economy.
“Republic Services is committed to challenging every truckload we collect from customers and advancing circularity for key materials,” he says.
“The Polymer Center will help enable true bottle-to-bottle and package-to-package circularity for plastics, helping customers achieve their own sustainability goals. Our integrated regional hub-and-spoke model will ensure nationwide coverage. We’ve received an overwhelming response from the industry and potential customers, which has accelerated the development timeline for our second and third Polymer Centers.”
The company plans to build three more Polymer Centers, including one in Indianapolis and another in Buckeye, Arizona, to address the gap between supply and what it calls “fast-rising” demand for recycled plastics driven by regulations and a shift in consumer preferences for sustainable packaging. A report by The Recycling Partnership, Washington, estimates the gap between the current U.S. supply of rPET for use in bottles and the projected demand in 2025 is close to 500,000 tons.
“Our strong partnership with Stadler and Krones, the design and quality of equipment and successful implementation in Las Vegas has given us the confidence to purchase systems two and three for our centers under development,” Keller says.
For more information
Stadler Anlagenbau GmbH, Germany, www.w-stadler.de
Krones, Germany, www.krones.com/en/index.php
Brian Taylor
Brian Taylor is senior editor at the Recycling Today Media Group and can be reached at [email protected]. This story was published in Plastics Recycling, a joint publication of Plastics Machinery & Manufacturing and Recycling Today.
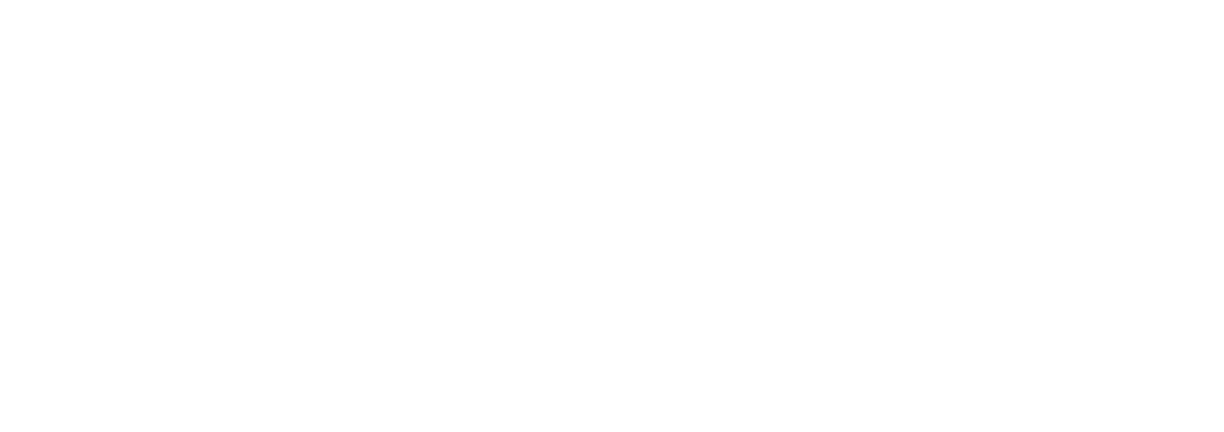