Problem: There’s been no way to manufacture caps that can be easily recycled in the PET stream.
Solution: A new thermoforming technology from Origin Materials produces PET and recycled PET caps at a speed that’s competitive with caps that have been injection or compression molded from other materials.
By Karen Hanna
Take a look at the lid of an average soda bottle, and you’ll probably see the words, “Recycle bottle with cap on.”
But don’t take that as a guarantee it will be recycled. Very likely, its life is over when you finish your drink.
The problem is that the cap is HDPE, the bottle, PET. There’s a 50 percent difference between recycling rates for the two materials; according to a 2019 estimate from the U.S. Department of Energy, 15 percent of PET is recycled, compared to 10 percent of HDPE. That HDPE might be swept up as so much flotsam when it falls away from the PET of your bottle in a recycler’s sink-float tank.
For a company that began with the goal of addressing sustainability issues through materials R&D, the answer seemed simple enough: Just use PET for caps, too. But it’s harder than it sounds.
Where others have failed, Origin Materials stands on the precipice of success, with the insight that compression and injection molding — currently used to make caps from materials other than PET, like HDPE — aren’t the way to go. Instead, it’s designed a novel technology, called the CapFormer, that could ensure the entire bottle — cap and all — can be recycled again and again. The first machine began commercial-scale production Feb. 20 at the Reed City Group, a Michigan molding shop with which Origin Materials has partnered.
“Our system is a game-changer for packaging circularity and performance by enabling the first-ever commercial production of PET caps — including caps made from recycled PET” (rPET), even 100-percent recycled material, according to John Bissell, a founder and the CEO of Origin Materials.
At stake could be hundreds of millions of dollars in contracts — or more — and the manufacture of billions of caps.
Rethinking how caps are made
Established with a materials and chemistry focus, Origin Materials has been working on ways to make PE furanoate — a recyclable biobased material — cost-competitive with the ubiquitous, versatile and far-less-expensive PET. Then, the company started looking at PET itself. At first, like injection molders before them, the company’s team of 100-plus scientists and chemists thought they might be able to bend PET’s properties to the requirements of injection molding.
But as they have found out, PET just isn’t compatible with the process.
“The problem is the PET doesn’t behave similarly enough to the polyethylene to get rapid production of the caps and to get the minute features that are required for the caps to perform well. ... The threads, for example, have to be pretty precise to make it work the way you want,” Bissell said.
The company then turned to stamping, with some re-engineering to accommodate the undercuts involved with those tricky threads.
Leveraging slit-and-fold technology, the company designed a machine that’s just a bit different from other thermoformers. Currently, it’s working with manufacturing partners in Europe to bring its CapFormer design to life.
“The problem is, how do you get something that bends under when you’re flipping it out of a two-dimensional sheet?” Bissell asked. “Thermoforming PET is not new, but thermoforming PET in a highly precise way where you can get that undercut, that three-dimensionality, is the key to what we did.”
The design of the molds for the caps was the essential breakthrough, according to Bissell.
“The machines are not so different than what’s out there for thermoforming right now, but there’s slight tweaks to the machines, and then the molds are completely different, and there’s some tricky elements around the molds, and then the integration of which machines [are] together is also novel. That’s new.”
Putting CapFormer to work
Origin Materials announced in an August press release it had secured a two-year, $100 million-plus memorandum of understanding to supply billions of caps to its first customer; by the February startup of the first line, Bissell said the company had inked additional agreements with customers.
On Feb. 27, it announced it planned to have eight CapFormer lines in operation by the end of the year.
But as a chemicals company, Origin Materials doesn’t have bandwidth for large-scale, long-term manufacturing. So, it turned to someone who does.
Enter Reed City. With around 200 workers, it serves four major sectors — the consumer goods, life sciences, automotive and heavy truck industries — and builds molds in-house.
“Bringing on new technology, that’s kind of what we do. Here’s a need in the marketplace, here’s how we can fulfill it, and let’s bring it in and make it in our clean rooms,” said Trevor Mund, VP of finance and commercial management for Reed City.
Automation equipment for garage doors is the company’s bread and butter.
“We build injection molds, so we have a really technical group that could build a high-speed line to make a garage door, or we could build you an injection mold and run it to make a precision part with a ton of different resins today. ... Not PET, because you can’t injection mold that,” Mund said.
So far, Origin Materials has supplied its technology to Reed City, which plans to use it while Origin Materials retains ownership of all its CapFormers and purchases back the caps they make.
The first CapFormer arrived in January, just weeks before Plastics Machinery & Manufacturing spoke to both men.
Prior to partnering with Reed City, Origin Materials put its CapFormer technology through beta testing, Bissell said.
“We wanted to go to somebody who, 1, knows a lot of different processes, so that we can bring in as much knowledge as we can around this to both effectively operate and then, if there are ways to beneficially change it, great,” he said. “And then, 2, [we chose] somebody who knows how to start up new processes, because even if you have experience in thermoforming, for example, bringing online any new process is quite different than just running one that everybody knows.”
Trained for change
During the late January conversation, Mund acknowledged that Reed City hadn’t thermoformed in many years. But it’s not daunted by a challenge.
As other companies have struggled to maintain and upskill their workforce, the company has embraced apprenticeships, community partnerships and cross-training to build out its employees’ repertoire.
“Our company’s not really segmented in a way where, ‘You work in this group, you can’t go work in this group.’ If you need to pull resources, we have it available,” Mund said.
He said in its partnership with Origin Materials, Reed City will be working to quickly scale up CapFormer production.
While one machine line officially started production Feb. 20, Bissell said, “We expect to ramp the production volume of Line 1 over time and with additional CapFormer systems being manufactured and tested concurrently with the startup of Line 1. ... We’ll be bringing additional CapFormer systems online throughout 2025.”
For now, four Reed City employees, including a plastics engineer who’s taking the lead, are overseeing the CapFormer project, but Mund anticipates that number will grow considerably.
“In the next couple of years, we’re going to need at least 30 people that are technical, not like your typical [employee] you think about, like an operator, but technical people to make a successful launch,” Mund said.
The company runs four accredited apprenticeship programs, and it’s hired several graduates of the plastics engineering program at nearby Ferris State University in Big Rapids, Mich.
It’s also looking to the university to help current workers conquer any learning curve associated with its plunge into thermoforming.
Bissell praised the capabilities of Reed City’s workers and the company’s track record of drawing talent from the local area, where the automotive industry has deep roots.
“They go get a bunch of people there from that industry, and then we were really impressed by the internal training programs that they’ve developed,” he said. “There’s accredited programs inside of Reed City where they will train up folks across a variety of quite technical disciplines. It’s really an impressive company.”
Poised for growth
Both Origin Materials and Reed City are champing at the bit to prove out and scale up the CapFormer lines; while so far only in operation at Reed City, the machine technology is available for license by other companies.
Origin Materials and Bissell are expecting big demand, as processors and brand owners see the advantages the CapFormers offer. Overall, the caps and closures market is worth $65 billion annually, according to Origin Materials.
In the August press release, Bissell looked forward to catalyzing a “revolution in recycling circularity” and “explosive growth for our PET caps business.” The next month, he said, “The first Origin CapFormer system has already made several million PET caps using recycled PET plastic, and we’re just getting started. Looking ahead, we expect Origin CapFormer systems to produce caps not only for a diverse array of beverage bottles, but food packaging, medical products — the possibilities are extensive and incredibly exciting.”
Though Origin Materials so far is focused on manufacturing those familiar caps on 20-ounce bottles of carbonated beverages — known as PCO 1881-compatible caps — Bissell has his sights set on many other closures, as well.
The CapFormer technology, he said, can produce caps that perform better than injection molded caps. But the biggest advantage becomes obvious with bigger lids.
Surprisingly, in a race between injection molded caps and thermoformed caps, the thermoformed caps have speed on their side.
“The extreme example,” Bissell said, “would be a peanut butter lid. If you look at those larger caps, the number of injection ports doesn’t scale with the volume of material that the cap requires. You’ve got to be injecting material across a longer radial distance to get to those features, and so the cycle time goes up quite a bit, because your volume of material is going up with the square of the radius of the cap. With thermoforming, you don’t have that problem. The cycle time for a large cap is exactly the same as a cycle time for a small cap.
“So, if we can compete at this scale, we’re much more advantaged for the larger caps.”
With experience in making products for the health-care sector, Reed City has access to a market that also might benefit from the CapFormer technology, Bissell said.
Eventually, he said, Origin Materials might license its technology to thermoforming companies and retrofit their machines.
“We think that would actually be one of the better ways to roll this out over time, is to go back and look at existing, appropriate PET thermoforming machines and install capacity there, as well,” he said.
While he conceded that some companies might stick with non-PET caps, Bissell said he would prefer a future where the lid on your bottle or jar matches the material used to make the container.
The CapFormer’s launch brings that reality one step closer.
“Our view is that from a top-down perspective, everything should be PET,” Bissell said. “Probably, if you could, all of the caps should be PET, if you could do it. From a more practical perspective, we will likely have solutions for the vast majority of different types of closures, eventually.”
Contact:
Origin Materials, West Sacramento, Calif., www.originmaterials.com
Karen Hanna | Senior Staff Reporter
Senior Staff Reporter Karen Hanna covers injection molding, molds and tooling, processors, workforce and other topics, and writes features including In Other Words and Problem Solved for Plastics Machinery & Manufacturing, Plastics Recycling and The Journal of Blow Molding. She has more than 15 years of experience in daily and magazine journalism.
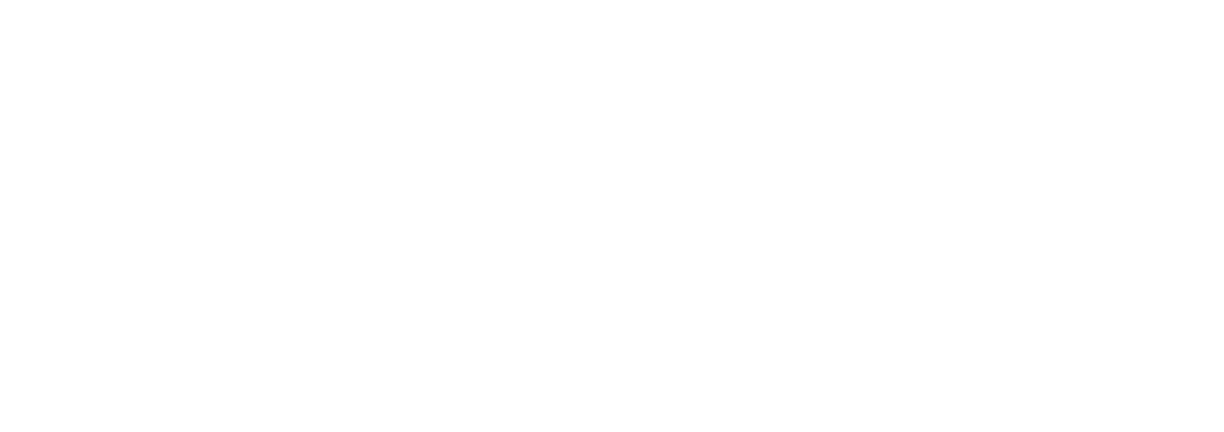