By Bruce Geiselman
Lanxess, a specialty chemical company based in Cologne, Germany, looked to go green at the K Show as it introduced new Tepex thermoplastic composites using recycled or bio-based raw materials.
“With these construction materials, we want to help our customers to make more-sustainable products, have a smaller carbon footprint, conserve resources and protect the climate,” Dirk Bonefeld, head of global product management and marketing for Tepex at Lanxess, said in a press statement.
Tepex is Lanxess’ family of fiber composites based on engineering thermoplastics.
One of the new product lines is Tepex Dynalite Scopeblue 813, which is made from bio-based raw materials — flax fibers and polylactic acid. Flax fibers are significantly less dense than glass fibers. Composites made with these fibers are noticeably lighter than their glass-fiber (GF)- or carbon-fiber (CF)-reinforced counterparts, but the flax fibers contribute to mechanical performance, according to the company’s website.
“Stiffness and strength of flax fibers are significantly lower compared to GF/CF,” a Lanxess spokesman wrote in an email to Plastics Machinery and Manufacturing. “On the other hand, also the density is significantly lower; thus, flax offers a comparable weight-specific stiffness to glass fiber.”
Products made from the material include sports equipment and luggage, Lanxess said.
“Due to the lower mechanical performance compared to other Tepex products, we don’t target for high-performance structural applications, wherefore we prefer ‘conventional’ Tepex grades like glass- or carbon-continuous-fiber-reinforced polyamides, polycarbonate or polypropylene,” Lanxess wrote.
Also at the show will be a new Tepex Dynalite with a PA 6 matrix that is produced from “green” cyclohexane. It consists of more than 80 percent sustainable raw materials, according to the company. To qualify as“green,” according to Lanxess, at least 50 percent of a material must be recycled or capable of growing, or the material must reduce greenhouse gas emissions by 50 percent or more compared to the conventionally produced product.
The company also is developing new Tepex bio-based alternatives to PA 12, including bio-based PA 10.10, which is derived from castor oil. The PA 10.10 is available in production scale, according to the company.
“The composite materials made with it are a sustainable alternative to polyamide 12 composites because they have similar mechanical characteristics and a comparable density,” Bonefield said.
It can be used for sporting goods, like bicycle saddles, according to the company.
Bruce Geiselman, senior staff reporter
Contact:
Lanxess AG, Cologne, Germany, 49 221 88850, www.lanxess.com
Bruce Geiselman | Senior Staff Reporter
Senior Staff Reporter Bruce Geiselman covers extrusion, blow molding, additive manufacturing, automation and end markets including automotive and packaging. He also writes features, including In Other Words and Problem Solved, for Plastics Machinery & Manufacturing, Plastics Recycling and The Journal of Blow Molding. He has extensive experience in daily and magazine journalism.
Rapid Granulator names new sales agents
PLASTICS adds to leadership team
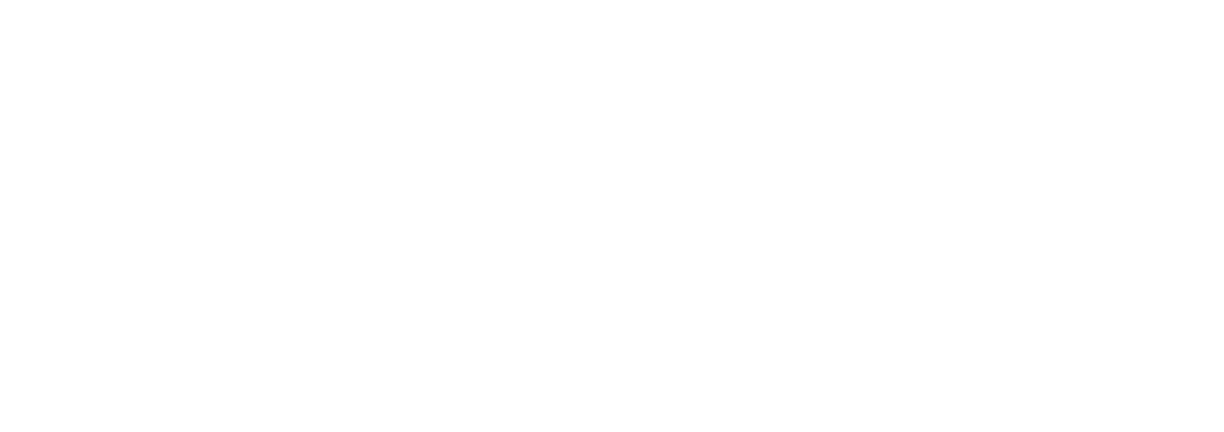