This story appeared in the Summer 2020 edition of Plastics Recycling magazine.
A growing number of hard-to-remove bottle labels coming into the Clear Path Recycling LLC plant in Fayetteville, N.C., over the years prompted a $1 million investment in a new prewash system that has boosted output and improved the quality of its recycled polyethylene terephthalate (PET) flake.
Clear Path, a joint venture between virgin resin producer Dak Americas LLC, Charlotte, N.C., and carpet manufacturer Shaw Industries Group Inc., Dalton, Ga., was launched in 2010 to recycle postconsumer PET bottles using equipment primarily from Italian manufacturer Sorema Plastics Recycling Systems. But as collection systems for recyclables changed, labels posed a processing challenge.
Clear Path’s solution was to replace two slow-spinning wash trommels with a custom-designed trommel system from Sorema that was installed in 2019. The new system is faster, more efficient and uses less energy and water. It is designed to meet the changing characteristics of the postconsumer bottle stream.
“We have seen efficiencies with the trommel because it does a better job of eliminating labels,” says Antonio Garza, global vice president of recycling technologies at Dak. “We did have a lot of rejects due to label contamination where the label was not coming off the bottles, especially the full-sleeve bottles. The pin structure in the new equipment does a better job of shredding the labels, which helps us get them off the base PET bottle. That helps reduce rejects and improves yields.”
Garza says the new trommel also is better at removing aluminum caps. “We do a lot less rework [reprocessing] with the new system,” he says.
Reducing the amount of water used also extends the life of other processing equipment by reducing the humidity in the building.
The location and configuration of the new trommel system had to be re-engineered. Stadler Anlagenbau GmbH of Altshausen, Germany, built the new conveying system.
Total output has gone from about 90 million pounds per year to about 95 million pounds, and Garza says it may improve as Clear Path becomes more familiar with the equipment.
Shaw uses the recycled PET for its carpet, while Dak uses it in products that require recycled content. About 25 percent — mostly mixed colors and green flake — is sold through merchant sales. Postconsumer material is sourced primarily from the Southeast U.S.
The plant employs about 100 people, which did not change with the addition of the new equipment.
With more efficient prewashing in place, what’s next for the North Carolina facility? Garza says its byproducts, bales of mixed material it sells to customers, still contain PET.
“It is one of our next areas of focus,” he says. “How can we deal with every PET bottle in-house rather than letting some material escape and go out with our byproduct sales? There are opportunities to work on material recovery and make our sortation more efficient.”
Ron Shinn, editor
For more information:
Clear Path Recycling LLC, 877-387-3738, www.clearpathrecycling.com
Dak Americas LLC, 910-433-8200, www.dakamericas.com
Shaw Industries Group Inc., 800-720-7429, www.shawinc.com
Sorema Plastics Recycling Systems, 39-031-6349-1250, www.sorema.it
Ron Shinn | Editor
Editor Ron Shinn is a co-founder of Plastics Machinery & Manufacturing and has been covering the plastics industry for more than 35 years. He leads the editorial team, directs coverage and sets the editorial calendar. He also writes features, including the Talking Points column and On the Factory Floor, and covers recycling and sustainability for PMM and Plastics Recycling.
Farrel Pomini earns EcoVadis gold medal
PLASTICS: NPE2024 achieves recycling goal
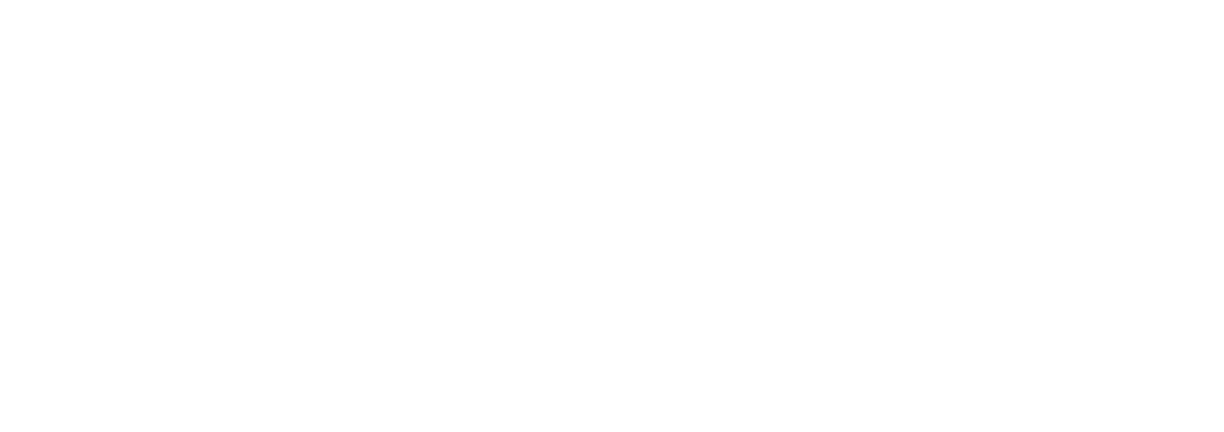