This story appeared in the Summer 2020 edition of Plastics Recycling magazine.
New additives are designed to take on haze and other challenges associated with recycling difficult materials, including black products and multimaterial film.
BASF Colors & Effects USA
BASF Colors & Effects USA LLC, Southfield, Mich., designed its Sicopal Black K 0098 FK to assist in recycling black plastics.
Because carbon black pigment absorbs near-infrared (NIR) light waves, even trace amounts of carbon black can escape the notice of optical sorters that use NIR technology. As a result, black plastic recyclables cannot be recovered in the optical sorting process and, therefore, are either landfilled or incinerated.
However, Sicopal Black K 0098 FK is designed to reflect rather than absorb NIR light waves, which allows for the identification of recyclable plastics — even those with high pigment content.
“The Colors & Effects research and development team has proactively taken on the industry need for recyclable black plastics that can pass through infrared sorting at materials recycling facilities,” says Christof Kujat, head of global technical industry management for plastics at BASF Colors & Effects GmbH. “We have developed a new member of the pigment family with the aim to optimize it for use in packaging. In the end, our team has succeeded in creating a new pigment for recycling of black plastics with improved value in use.”
The new food-compliant pigment is opaque and can be used in sensitive applications.
Sicopal Black K 0098 FK is stable and safe even after multiple recycling processes, Kujat says. The pigment is compatible with all types of plastics, including
polyethylene terephthalate (PET), which requires processing at higher temperatures that can degrade other pigments.
BASF first unveiled samples of plastics that used the new pigment last fall at K 2019 in Düsseldorf, Germany. However, the company announced the product name and launched sales early this year.
PolyOne
In late April, Avon Lake, Ohio-based PolyOne Corp. introduced ColorMatrix Amosorb 4020G, which is a non-nylon-based oxygen scavenger for rigid PET packaging.
ColorMatrix Amosorb 4020G reduces the yellowing of clear PET during recycling. It also produces about half as much haze as other oxygen scavengers, the company says. Like other oxygen scavengers, when added to PET packaging, it can extend the shelf life of products like juices, teas and flavored waters by protecting them from exposure to oxygen.
PolyOne says its testing indicates that ColorMatrix Amosorb 4020G is one of the most robust oxygen scavengers for rigid PET containers. Unlike other competitive materials, which are ineffective oxygen scavengers when used with recycled PET (rPET), the additive lost little effectiveness when tested with rPET grades. Other competitive materials lost almost all oxygen scavenging ability with rPET content as low as 20 percent, according to PolyOne.
The company says it can provide the additive to meet applicable regulatory approvals.
Ampacet
Ampacet Corp., Tarrytown, N.Y., recently introduced ReVive 962, a compatibilizer masterbatch that allows multi-material packaging films to be recycled back into high-quality film.
The compatibilizer is an addition to the Ampacet ReVive portfolio of additives. ReVive 962 is designed exclusively for recycling polyolefin barrier films that have ethylene-vinyl alcohol (EVOH) as the exclusive co-extruded barrier layer. Other ReVive formulations can be used with nylon barrier films or films with a combination of nylon and EVOH barriers.
While monomaterial packaging films, such as polyethylene or polypropylene, can be recycled easily, multi-material packaging films present challenges because the materials often are incompatible. For example, food products frequently require multimaterial packaging that includes an oxygen barrier. However, introducing non-polyolefin components, like EVOH, into a polyolefin recycling stream could prevent polyolefins from being recycled into high-quality packaging material.
Ampacet ReVive 962 allows for the use of reclaimed multimaterial polyolefin barrier packaging in producing quality film and reduces the need to send scrap material to landfills, according to the company. Increasing the use of recycled material also reduces the use of virgin resin.
Ampacet ReVive 962 is designed for in-house recycling of scrap industrial polyolefin film with an EVOH barrier into the original film structure. Using the additive improves the transparency and mechanical properties of the reprocessed film, according to Ampacet.
“ReVive 962 offers a circular economy solution for EVOH-based barrier polyolefin packaging, providing an alternate end of life to landfill disposal,” says François Thibeau, Ampacet’s strategic business manager of film additives in Europe. “ReVive 962 improves considerably optical and mechanical properties of your reclaim[ed] material, enabling upcycling into quality film applications. This innovative additive masterbatch allows higher usage of recycled plastics while preserving packaging clarity, thus helping to reduce consumption of virgin material and valorizing the multimaterial packaging waste.”
Bruce Geiselman, senior staff reporter
For more information:
Ampacet Corp., 914-631-6600, www.ampacet.com
BASF Colors & Effects USA LLC, 973-245-6000, www.colors-effects.basf.com
PolyOne Corp., 440-930-1000, www.polyone.com
Bruce Geiselman | Senior Staff Reporter
Senior Staff Reporter Bruce Geiselman covers extrusion, blow molding, additive manufacturing, automation and end markets including automotive and packaging. He also writes features, including In Other Words and Problem Solved, for Plastics Machinery & Manufacturing, Plastics Recycling and The Journal of Blow Molding. He has extensive experience in daily and magazine journalism.
Farrel Pomini earns EcoVadis gold medal
PLASTICS: NPE2024 achieves recycling goal
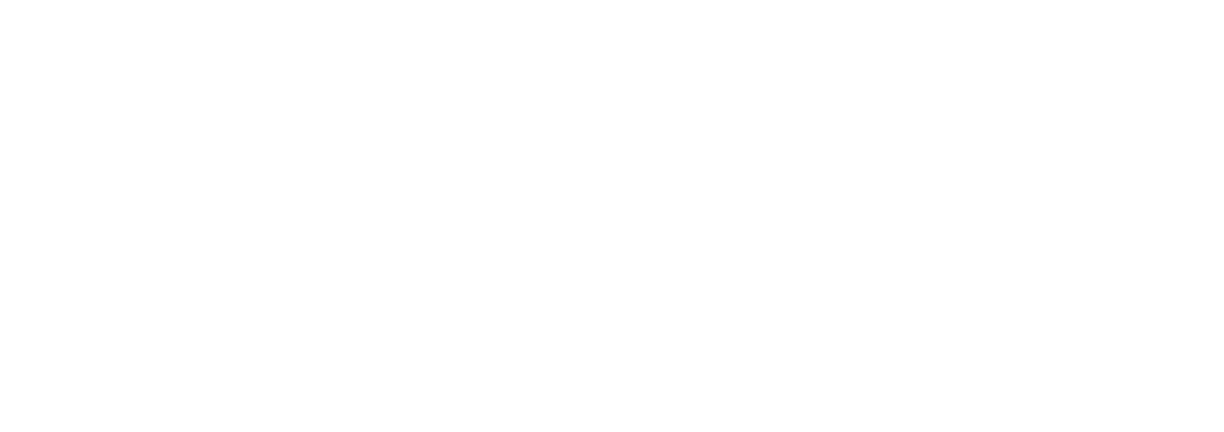