Mini Mills Haas’ Mini Mills are compact CNC machining centers that have long been an option for shops that are looking to add machining capacity or a “second-op” machine where space is limited. They offer three-, four- and five-axis capabilities and provide many features found on full-size machines, while offering a small footprint.
What’s new? A complete redesign, with new castings that are 30 percent heavier for increased machine rigidity and stability. Other improvements include an increased work envelope, larger travels and faster spindle speeds.
Benefits Increased output production. The Super Mini Mill version, which offers higher spindle speeds, now comes standard with Haas’ 30+1 side-mount tool changer to offer more tools and faster tool changes, while freeing space for larger fixtures and rotary tables. The new Y-axis wash-down nozzle prevents chip buildup behind the table during extended machining operations, and an external 45-gallon coolant tank now is standard on all Mini Mills, boosting capacity and simplifying coolant maintenance and tank cleanout.
Haas Automation Inc., Oxnard, Calif., 805-278-1800, www.haascnc.com
Vital Statistics
New mini mill |
Original version |
|
X, Y and Z travels |
16 inches by 14 inches by 15 inches |
16 inches by 12 inches by 10 inches |
Maximum distance, spindle nose to table |
19 inches |
14 inches |
Maximum cutting speed |
54.2 feet per minute |
41.7 feet per minute |
Spindle speed |
8,000 rpm |
6,000 rpm |
Maximum torque |
45 foot pounds |
33 foot pounds |
Coolant tank |
45 gallons (external) |
40 gallons (internal) |
David Tillett | Associate Editor
Associate Editor David Tillett writes and edits for Plastics Machinery & Manufacturing, Plastics Recycling and The Journal of Blow Molding. He covers new products, industry news, patents and consumer and business equipment. He has more than 20 years of experience in daily newspaper, online and magazine journalism.
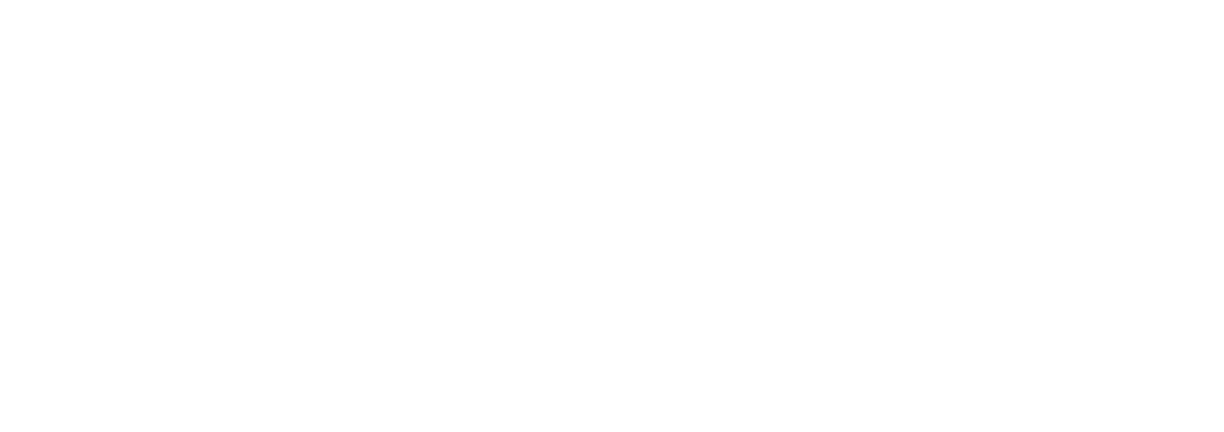