Alan Petrucci — an outgoing man with a sharp-witted sense of humor — has worked in the mold manufacturing business since childhood.
As an octogenarian, he continues working nearly every day on a part-time basis at B A Die Mold in Aurora, Ill., the company he co-founded 54 years ago.
There was little doubt growing up that Petrucci would go into the business. His father started Mir-O-Brite, a mold polishing business in Chicago, where Petrucci began working as a teen in his free time.
His maternal grandfather, Henry P. Bachner, founded Chicago Molded Products about 1900. Henry’s brother, Edward, then led the company with two older brothers beginning in 1918 or 1919 after Henry passed away from pneumonia, according to the family.
Petrucci has worked exclusively in the mold making field his entire life, except for a brief period during high school and shortly thereafter when he was a part-time tow truck driver and mechanic.
Petrucci’s younger daughter, Francine, joined B A Die Mold in 1994 and assumed the title of president in 2005. Another daughter, Cynthia Petrucci Kustush, worked at Imperial Plastics, a former sister company of B A Die Mold, when she was school age. Cynthia also worked at B A, helping in the office while on school breaks. She later was senior editor of MoldMaking Technology magazine for more than four years, and is now a freelance journalist.
Today, in addition to building molds, B A Die Mold provides short-run and low-volume production services.
In a recent interview with PMM Senior Staff Reporter Bruce Geiselman, Petrucci reflected on growing up in a family dedicated to mold building and polishing, changes to the business climate and technology over the years, and his plans for the future.
What was your first job in the plastics industry?
My first job was as an apprentice mold maker, and that was part time while I was in high school.
My original job as an apprentice was with Midland Die and Engraving in Addison, Ill., but they are long gone. They are out of business, but that is where I started my apprenticeship.
However, my father [Henry “Ozzie” Petrucci] had a mold polishing business [Mir-O-Brite] when I was a kid, and I used to work with him on weekends, holidays and summers. That’s where I became interested in becoming a mold maker. I think I was 13 or 14 when I started doing that.
I was learning to polish molds. Also, my father did repair work and hobbing. He had a hobbing press for the old-fashioned method of making cavities by hobbing. Nobody does that anymore. It is the process of pushing a hardened steel hob [a cutting tool] into soft steel to form a cavity. I don’t know how many people remember that.
You must have enjoyed that. What made you decide that mold making, and plastics processing would be your career?
I enjoyed working with my hands, and I enjoyed making things. And my family was all working in plastics, molding and mold making — my whole family.
My mother’s family owned Chicago Molded Products. My [maternal] grandfather pioneered molding. He was one of the first in the world to do molding using a printing press. (Laughter.) He used a converted printing press.
By the way, Chicago Molded Products at one time was the largest molding company in the world. It was international. It was founded in 1900 and by the ‘50s and ‘60s, they were the largest in the world. My grandfather, Henry P. Bachner, died of pneumonia in 1918, long before I was born. His three brothers lived in Canada at the time, and they came to Chicago and took over the company.
It was just a normal transition to go into mold making for me.
What did you do after your apprenticeship and what led to your founding of B A Die Mold?
After my apprenticeship, I was a lead mold maker and I worked at three different shops.
A friend and co-worker, Dennis Macomber, talked me into starting a shop. We started it in 1968, and after a couple of years, I bought him out and continued to grow and run B A Die Mold.
The interesting thing is that after my apprenticeship at Midland Die and Engraving, I worked at three other mold and die companies before starting B A Die Mold. All those earlier companies are out of business. Back in the day, they were all prominent shops in the Chicago area.
What made you decide to open your own company rather than work for someone else? Wasn’t that taking a chance?
It was, but my family — my father, my uncles, my grandpa — they all started their own businesses. It was the normal thing to do. Plus, my original partner, Dennis Macomber, bugged me and bugged me until I agreed to go ahead and start a shop. It was just kind of a family tradition.
How would you describe B A Die Mold? What is the company known for?
We’re obviously a quality mold-making shop. We are known for building molds for clear and optical products. We did a great many molds for Moen faucets. They are still a customer. We designed and built molds for the Chateau faucet handles that have been extremely popular and well known for many, many years. They were the teardrop-shaped faucet handles for bathrooms that were clear and looked like crystal.
We make clear acrylic plastic handles for faucets. We’ve done a lot of that for Moen, Sloan and Delta. We’re also into water filtration, we’re into medical, and we’re into closures with threads — threaded unscrewing products that come from unscrewing molds. We’re very well known for that.
Through the years, we also built a lot of molds for the plastic housings for electrical switches for automotive applications, for electric windows and cruise control and things like that. We built the molds for and molded light housings for ceiling lights, and automotive under-the-hood products in thermoset plastic, and parts for televisions.
At that time, your channel changing knob on your TV was mechanical, and there were electric coils that made up those switches. We molded [components] for Motorola and RCA.
We did that molding with a different company that we founded in 1979 called Imperial Plastics. It operated for about 13 years. One of our customers went out of business. At the auction, we grabbed some of their molding machines and we started molding. We still mold parts now, but it’s here at B A Die Mold. We don’t have the separate company anymore. We do sampling and short-run molding.
We didn’t do tchotchke stuff. We did engineering stuff. Engineered products were, and continue to be, our focus.
You started as president of B A Die Mold; do you still hold that position?
There has been a progression. My younger daughter, Francine Petrucci, is now president. I appointed her president of B A Die Mold in 2005. Now she is my boss. She’s doing a great job. She joined the company full time after graduating from Northern Illinois University, cum laude, with a bachelor’s degree in engineering in 1994.
How have your responsibilities changed as you have transitioned to working part time?
Originally, I was designing molds and doing sales and doing estimating. I did all of that early on when we first started B A. I did that for probably 10 or 12 years, and then eventually we hired designers and I continued with sales and estimating, and eventually we hired people to help with that sort of thing as well. That was primarily what I did for a large part of the time. In addition, I worked in the shop when needed. When we got really busy, I would put on an apron and get out in the shop.
Right now, I’m primarily involved in estimating and providing assistance to our designers.
Do you have any plans to retire?
I don’t have a date in mind. I enjoy what I do. I love estimating and figuring out the best way for making a mold for the parts we are asked to quote. I enjoy that. It’s problem solving. I keep teasing Francine that maybe I’ll retire when I’m 85, God willing.
I’m reasonably healthy. I enjoy what I am doing. I’m only working four or five hours a day. Until I’m unable to do this, I’ll probably keep doing it just because I enjoy it. I feel sorry for people who hate their jobs. I really do.
What has been most rewarding about your career?
The most rewarding thing is the people I have met over the years. There have been some wonderful people, including employees that I enjoyed working with, some of whom went on to start their own shops eventually. We had several of our employees who started their own businesses when they left here. When they gave notice for that reason, I was really happy for them — delighted — and I wished them the best. We even from time to time gave them work when we needed outside help. I really enjoyed that they went on to improve their lives and improve their position.
I enjoy meeting and working with people.
What have been your greatest accomplishments?
No. 1 is staying in business for 54 years when a lot of other shops have closed. Also, making friends. I have longtime friends. Customers that were engineers at the companies they worked for ended up being close friends. I think that was an accomplishment — making friends with customers, employees and others.
Another accomplishment is that I was Mold Maker of the Year in 2011 from the American Mold Builders Association. I was blown away. It was amazing.
I developed our PERC System, which stands for programmable electronic rotating cores. I got the patent on that. [PERC is a compact, high-speed, high-torque and high-precision system using programmable servo motors in place of hydraulics for unscrewing applications. A servo motor rotates the core in place of conventional hydraulic unscrewing systems that need a rack and cylinder]. PERC offers unlimited turns because it is electric and does not require the large, bulky cylinders. Works great with today’s electric molding machines but also works with traditional molding machines. It’s deadly accurate.
I originally developed it for a water filtration customer that had several rotating cores in the cavities that had to be sequenced. There was just no way to do it with hydraulics at the time. It was in the middle 1980s.
I have two patents. The other one is for a mold that makes a plastic medical part. It’s for surgeons. It makes a part that guides a wire through arteries to place stents during an angioplasty. I am co-owner of that patent with a customer because I designed and built the mold to make it, which was very complex.
What trends are you seeing in mold making?
More and more molders are using hot runner systems in their molds, and I think it is a move toward more economical molding because plastic material is expensive. That is the main trend that I have seen over the last few years.
Also, I think lately the larger molding companies are coming back on shore to have their molds made. The molders were going offshore because their customers were demanding cheaper prices for them, but lately they’ve been coming back to the U.S. I can say that B A Die Mold has never gone offshore for molds. We do everything here in America. Part of the reason is that I refuse to give our engineering skills and engineering know-how to an offshore company.
What hobbies do you have or have you had?
I built drag cars and raced them. My father raced motorcycles and midget cars in Chicago at Soldier Field and the Santa Fe Speedway.
My other hobbies were deer hunting, pheasant and duck hunting. I did that for years with bows and arrows. Also, boating and fishing are my other hobbies.
In your early years in business, who was your mentor?
My brother Robert was a lead mold maker and I worked under him as an apprentice. He’s seven years older than I. He was a mentor.
Then there were the owners of the shops I worked at — in particular, at Action Mold & Engineering, one of the partners was Joe Stefan. He also was my boss when I worked at Midland Die and Engraving as an apprentice. He was the plant manager. He was a longtime mentor — a great guy, very knowledgeable.
What major challenges did you encounter as B A Die Mold grew?
Primarily finding skilled employees — attracting and hiring good mold making people. It’s still a challenge, even more so now, I think.
Schools didn’t help. Over the past 15-20 years, the secondary schools pushed people into college instead of a trade. When I went to high school, we had a machine shop. We had auto shop. We had sheet metal shop. We had a lot of shop courses that went away over the past 30 years.
When I was on the board of the Chicago AMBA [American Mold Builders Association], the local guys here and I started a school for mold making apprentices, and I was one of the teachers at that school. It has been taken over by the TMA [Technology and Manufacturing Association].
Until very recently, I served on the board of the AMBA Chicago Chapter, which was the founding chapter, and I was a three-time president. I served on the board since the AMBA started; and Francine has served on the board for many years — she is very active even now.
I also served on the board of the TMA. I think I have contributed a fair amount of my time and energy into the trade associations. It has always been important to me to give back to this industry that I love. I have been very fortunate.
How would you like to be remembered?
I’d like to be remembered as a handsome guy (laughter). That’s a lie. I want to be remembered as a well-liked person and a fair person that was good at what I did and had many, many friends.
Just the facts
Who is he: Alan Petrucci, principal and founder, B A Die Mold Inc., Aurora, Ill.
Education: Lyons Township High School, LaGrange, Ill., 1958; Lyons Township Junior College (now a part of the College of DuPage), associate degree in mechanical engineering, 1960; College of DuPage, Glen Ellyn, Ill., associate degree in business, 1970.
Years in the plastics industry: 64 (since 1958)
Age: 82
Awards: Mold Maker of the Year for 2011 from the American Mold Builders Association
Company founded: 1968
Employees: 14
Bruce Geiselman | Senior Staff Reporter
Senior Staff Reporter Bruce Geiselman covers extrusion, blow molding, additive manufacturing, automation and end markets including automotive and packaging. He also writes features, including In Other Words and Problem Solved, for Plastics Machinery & Manufacturing, Plastics Recycling and The Journal of Blow Molding. He has extensive experience in daily and magazine journalism.
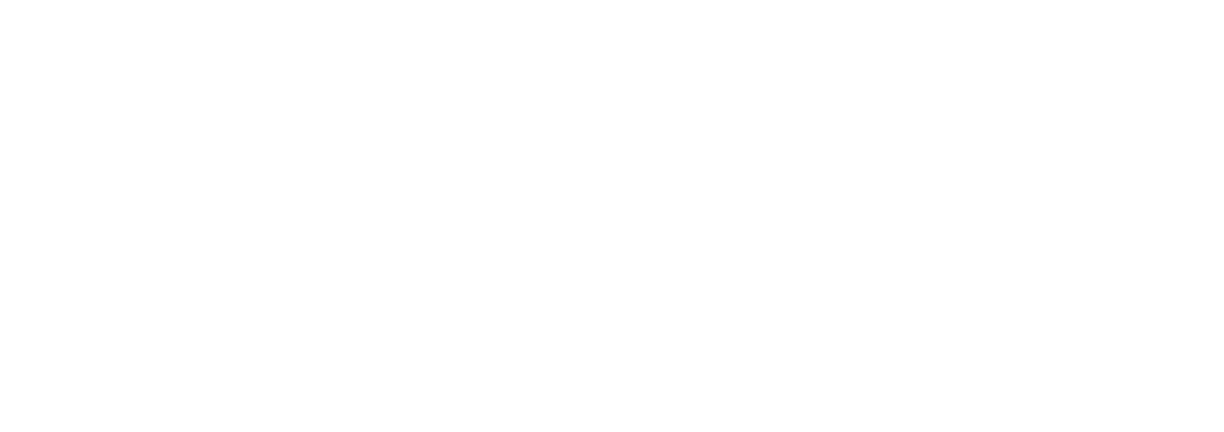