Mubea sees possibilities in composites, new materials for automotive industry
By Bruce Geiselman
Automobile manufacturers and parts suppliers increasingly are adopting plastic parts to help meet evolving regulations and consumers’ and shareholders’ demands for sustainability and improved environmental performance.
The federal government, by tightening Corporate Average Fuel Economy (CAFE) standards, is encouraging automakers to reduce vehicle weight in internal combustion engine (ICE) vehicles. At the same time, as the government and automakers are striving to encourage consumers to buy electric vehicles (EVs), automakers are trying to trim part weight. Plastics are playing a key role in those initiatives.
One company that’s had success lightweighting vehicle parts is Tier I supplier Mubea, which, along with General Motors (GM), was honored last year as the Grand Award winner of the Society of Plastics Engineers’ Automotive Division’s 51st annual Automotive Innovation Awards competition.
Mubea developed the first all-composite leaf spring for light trucks — a part that GM uses in its 2022 Chevrolet Silverado and GMC Sierra light trucks. Consisting of about 60 percent glass fiber by volume, the part is created through compression molding.
The part reduces mass by up to 75 percent compared with all-steel construction and 58 percent compared with hybrid steel/composite leaf springs. It's twice as durable, improves ride comfort, lowers noise and vibration, and increases payload, according to Mubea. Also, unlike metal, it can’t corrode. Fiberglass-reinforced epoxy prepreg is used to form a single leaf with a progressive spring rate that eliminates the shackle and shackle bushing.
Mubea had developed a similar technology for composite leaf springs for use on commercial vans in Europe, before bringing the idea to U.S. light truck makers.
“GM was particularly interested and almost immediately started funding basically an R&D program to work through the implementation hurdles that we might see while adapting this to the North American truck market, since the whole situation is a little different for consumer pickup trucks in North America versus a commercial van in Europe,” said Jared Heitsch, engineering manager for Mubea’s chassis composites business unit in North America.
Mubea is a long-time supplier of parts for chassis and body components to automakers but began working with plastic composites only within the past 15 years.
“We’re a lightweight components specialist that for almost 100 years was focused entirely on steel products,” Heitsch said. “We got into composites a little over a decade ago. It was around 2008 that we started doing R&D in composites.”
The automobile industry is increasingly facing conditions that favor the use of lightweight, durable plastic composites.
“This is kind of an interesting time in the marketplace,” Heitsch said. “With EVs, there’s a lot of push for lightweighting because the batteries are extremely heavy. If you’re looking at a similar-size vehicle, you’re seeing pretty shocking numbers for how heavy the BEV [battery electric vehicle] version of a similar-size vehicle can be [compared to an ICE vehicle].”
At the same time, ICE vehicles need to meet increasingly strict fuel economy standards.
“Basically, we’re in a situation where there is significant cost savings as a whole to GM for implementing our springs because they’re able to reduce the weight of some of the vehicle variants, which drops them down into different weight classes. This dramatically reduces their greenhouse gas penalty costs, basically, that they would have to pay to the government. Essentially, they get a lighter-weight vehicle that performs better, customers are happier with because there is less noise and there is improved ride quality, and they save money by using it. It’s a win-win all around on those,” Heitsch said.
Another reason for switching from metal to plastic parts is to improve sustainability and decrease greenhouse gas emissions during manufacturing.
“I would say North America is a little behind Europe on this one,” Heitsch said. “Most of our European customers flat-out require sustainability reports.”
Those reports include statistics about all carbon emissions produced by suppliers in manufacturing parts.
“For something like a leaf spring, which is traditionally a 60-pound steel part, there are tremendous amounts of carbon emissions required during the mining, the refinement and the production process for that part. The footprint is much smaller for a composite part that can replace that. As more companies strive to reduce those emissions, it’s kind of a no-brainer if you can take something like a 70 percent reduction in carbon emissions by switching from a steel part to a composite part in the same application.”
Bruce Geiselman, senior staff reporter
Contact:
Mubea Inc., Auburn Hills, Mich., 248-393-9600, www.mubea.com
Bruce Geiselman | Senior Staff Reporter
Senior Staff Reporter Bruce Geiselman covers extrusion, blow molding, additive manufacturing, automation and end markets including automotive and packaging. He also writes features, including In Other Words and Problem Solved, for Plastics Machinery & Manufacturing, Plastics Recycling and The Journal of Blow Molding. He has extensive experience in daily and magazine journalism.
Related
A3 publishes updated ISO 10218 standards
ACS Group names area sales manager
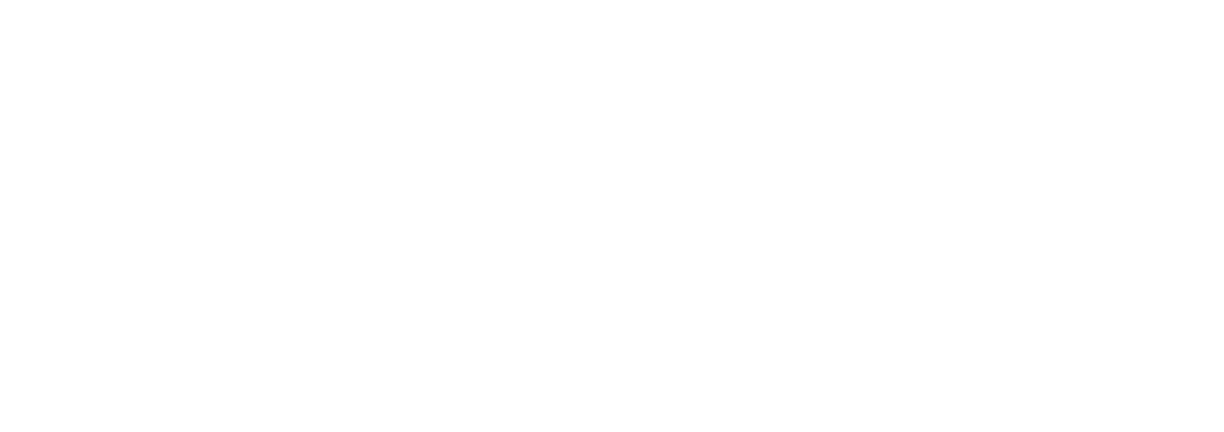