By Bruce Geiselman
Tier 1 supplier Teijin Automotive, which develops and produces advanced composites and components, is focusing on the needs of the automotive industry with advances in two areas: covers for batteries for battery electric vehicles (BEVs) and lightweighting.
The automotive industry’s transition to BEVs is “a tremendous opportunity,” said Hugh Foran, executive director of the Advanced Development Center for the company, which makes sheet molding compound (SMC) resins, body panels and pickup beds for Toyota, Honda and other manufacturers.
“We’re basically almost everywhere on the vehicle,” Foran said. “The [automakers] went down a path where these vehicles have gotten extremely heavy. If you’ve looked at any of the information on some of these newer EVs, they’ve gained a tremendous amount of weight … Some of the EVs, like the Hummer, have an over 3,000-pound battery back, and their vehicles weigh close to 11,000 pounds. That’s an extreme example, but when you start looking at all these trucks and the larger battery packs, they’re a lot heavier vehicles.”
The advantages of composites in EVs include lightweighting parts while providing high impact strength. Other advantages include design flexibility; reduced tooling costs, especially with lower-volume EV platforms; dent and corrosion resistance, and the ability to modify formulation chemistry to meet performance targets.
One of the fastest-growing areas for Teijin Automotive is producing resins for battery boxes and battery boxes for EVs.
“We have currently four formulations that are specific to battery cases — the covers and the trays,” Foran said.
- Teijin’s base grade is vinyl ester SMC grade with 50 percent glass for battery boxes that don’t need special thermal properties.
- A high-fill polyester/vinyl ester aluminum trihydrate is available for battery boxes and applications that require fire resistance.
- An intumescent grade of thermoset composite “scabs up like your body” to protect itself from heat during a fire involving batteries, Foran said.
- A phenolic resin — similar to the original Bakelite (invented in the early 1900s) — offers higher thermal resistance than aluminum.
In addition to the four basic formulations, Teijin is working with individual automakers to make resins and battery boxes specific to their needs. For example, weights of battery packs can vary significantly, so the amount of glass or carbon fiber in a resin blend can vary.
Increasingly, automakers are incorporating battery trays and covers into vehicles interiors. In some cases, battery covers serve as the floors of the vehicles, providing additional weight reductions.
“It [the battery cover] actually has the seat mounts and the center consoles, and it’s an actual part of the vehicle itself,” Foran said. “It’s not simply a battery cover, but it actually has all the components, so, when they bring it up into the vehicle, the carpet is there, the seats are there, the seat belt mounts, the center console is there, and it is actually more a part of the vehicle than just something that they bolt on after the fact.”
Another weight-reduction strategy Teijin is promoting involves the use of its Hexacore cellular core and Foam-A-Core foam core technologies for lightweighting composite body panels.
“We can mold very thin outer panels, and then they're supported by a cardboard or a foam core to give it the structure that it needs,” Foran said. “We're actually molding parts at a millimeter and a quarter thick, which is very thin for a composite panel. Previously, all the panels that we’ve been building have been around 2.5 millimeters thick. So, that does two things for us. It reduces the cycle time for curing, and it reduces the weight. It’s getting the structure from the paper honeycomb from behind.”
Bruce Geiselman, senior staff reporter
Contact:
Teijin Automotive Technologies, Auburn Hills, Mich., 248-237-7800, www.teijinautomotive.com
Bruce Geiselman | Senior Staff Reporter
Senior Staff Reporter Bruce Geiselman covers extrusion, blow molding, additive manufacturing, automation and end markets including automotive and packaging. He also writes features, including In Other Words and Problem Solved, for Plastics Machinery & Manufacturing, Plastics Recycling and The Journal of Blow Molding. He has extensive experience in daily and magazine journalism.
So, you need a new ERP. Now what?
A3 publishes updated ISO 10218 standards
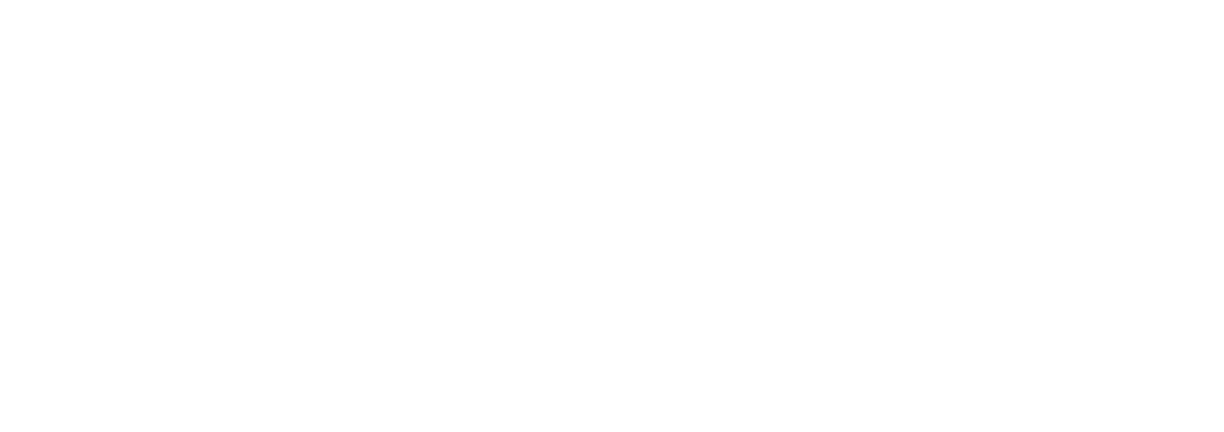