Most cars will shift to battery power; question is when, say industry experts
By Bruce Geiselman
Industry analysts and consultants agree that the automotive industry is on a path toward producing larger numbers of battery electric vehicles (BEV) and fewer traditional internal combustion engine (ICE) vehicles.
“In terms of the transition from ICE to BEV, it’s really no longer a question of if, it’s more a refinement of when or how quickly,” said Austin Biskner, a manager within Plante Moran’s automotive and strategy consulting practice, who serves as an advisor to the industry. “If you’re focused on recent OEM investment, the capital is really being allocated toward EV programs.”
OEMs are expected to invest about $1 trillion over the next 10 to 15 years across the value chain to achieve strategic targets regarding EV production, Biskner said.
General Motors, one of the world’s largest automobile manufacturers, is targeting 100 percent EV production by 2035, eliminating production of its ICE cars, trucks and SUVs. However, Biskner called that GM’s “marketing target.”
“We know that’s probably unlikely,” Biskner said. “It’s going to be kind of a two-camp approach, if you will. They’ll continue to make ICE vehicles throughout particular segments. However, the EVs are going to represent a significantly stronger population.”
By 2030, about 30 percent to 40 percent of GM’s production will be electric vehicles, according to Biskner.
“In a 5-year increment, to close that 60 percent to 70 percent gap, we don’t see that as being achievable,” he said.
However, the transition to EVs at this point is inevitable, Biskner said.
“There really is no contingency plan,” he said. “Focusing on GM, they’re really going all in on the EV space. There’s no longer any development being done in ICE engines. Ultimately, they’re riding the coattails of these legacy programs.”
Plante Moran’s internal proprietary model that it developed with the Department of Energy foresees that by 2035, about 58 percent of the production in North America will be electrified. Taking a pessimistic viewpoint, that target could be pushed back by another 3 to 5 years, Biskner said.
Launch cadence quickens
Automakers are expected to increase the pace of launching new EVs, which creates opportunities for plastic parts suppliers.
“Increased launch activity is going to drive new opportunities for the plastics industry,” Biskner said. “If you’re looking at the vehicle today, about 50 percent of the plastic consumption is really comprised on the interior of vehicles. If you’re an interior plastic supplier, these increased launch activities are an exciting thing for you.”
However, there could be a downside as about 25 percent of the plastics in vehicles today are used under the hood, including oil pans, intake manifolds and cam covers.
“Obviously, in an EV world, those go away,” Biskner said. “However, there are some replacements. We see some additional need for coolant reservoirs — now you have a battery thermal system as well as your HVAC system. If you look at the frunk [front trunk] on a Tesla, that’s all a composite piece.”
Battery enclosures represent one of the biggest opportunities for plastic parts manufacturers.
“An electric vehicle inherently is about 25 percent heavier than the comparable ICE vehicle, and that’s driven by the battery enclosure and the components of the battery,” Biskner said. “There is activity around creating a composite battery enclosure. That creates challenges, as typically the enclosures today are a structural component, so, there may be a composite cover for instance, but the actual structural component of the case would still be aluminum or steel.”
However, work is taking place on finding composites that can meet the requirements to replace metal parts in both EVs and ICE vehicles.
One example of composites replacing metal is the development of a new composite seatback design that was introduced on the 2022 Toyota Tundra pickup truck. The seatback design was developed in cooperation with chemical company BASF, L&L Products Inc. and parts supplier Flex-N-Gate.
“Historically, the components of a seat are all metal stampings with over 60 components welded together and assembled, and then ultimately you get your final product,” Biskner said. “The solution that they were able to develop involves four plastic injection molded components, and there's one pultrusion part.”
The pultruded part involves a composite material reinforced with fiberglass.
“They’re overmolding that pultrusion, and they’re able to achieve the strength properties of metal components,” Biskner said. “In addition, they’re able to reduce mass by about 20 percent.”
The transition from ICE to BEVs could present challenges to plastic parts suppliers because additional capital may be required for new production lines to manufacture the components, Biskner said.
The automobile industry is making huge strides toward producing more EVs, but the transition from ICE vehicles to EVs won’t happen overnight, said Gary Silberg, a partner and global automotive sector leader with KPMG, a professional services firm that provides consulting services to the automobile industry.
“Between now and 2026 or 2027, there will be 160 new models of EVs,” Silberg said. “They are beautiful, gorgeous. One-hundred-sixty, it’s mind blowing, and there are all these new companies from Rivian, to Lucid [Motors], to Lordstown Motors. There’s a company called Fisker. The Chinese have XPeng, Nio, BYD. Companies you’ve probably never heard of are starting to see massive growth in electric vehicles. That being said, it starts from a very small base.”
Only about 5 percent of the vehicles sold in the United States currently are EVs, he said. The percentages are slightly higher in other countries such as China and many European nations.
“It's going to be a slow but steady increase as these new models come on,” Silberg said. “You'll see continued very nice growth. So, the really big dilemma for the auto industry is going to be, how do we manage the transition? And how quickly will it take place?”
The transition to BEVs will be complicated by the fact that the nearly 300 million ICE vehicles are on the road in the United States today and they have a long lifespan.
“The average age of a car is almost 13 years as people are holding onto cars for a long time,” Silberg said. “If you do the math, if you are holding onto a car for even 10 years, it’s going to take a very long period of time to go from the 300 million to where EVs will actually be a very important portion of those.”
It could be 2040 or 2050 before ICE vehicles become largely obsolete.
“So, what you’re going to have in place is what we like to say at KPMG is a mosaic of powertrains,” Silberg said.
One of the main challenges for parts makers is to determine how to allocate their resources to meet the needs of traditional ICE vehicles while also producing parts for EVs.
“How do you do both, and do you have the talent to do both?” Silberg asked. “How quickly is one ramping up? How do we allocate our capital? These are billion-dollar bets that people are making. You could get it wrong by a few years very easily.”
Opportunities for plastics
A mixture of ICE vehicles, as a variety of EVs, will be on the roads for many years.
“You’re going to have some amazing EVs growing at incredibly fast speeds,” Silberg said. “You’re going to have plug-in hybrids, and hybrids are a huge area of growth because they’re more cost-effective and give you great range. You will have a lot of those, and you’ll have billions being bet on hydrogen. So, you’ll have hydrogen types of fuel systems, even solar, which is quite interesting, and even natural gas. All of those will play in a mosaic of powertrains, which we’ve really never seen for the industry.
“What people are grappling with, especially the plastics industry, is what type of materials should go into the vehicles, given that it’s going to be different than we’ve ever seen? That’s the 50,000-foot strategic question. Lightweighting in particular has become very important.”
Battery EVs can weigh up to 5,000 and even 6,000 pounds, he said. Parts manufacturers are working with the automakers on how to lightweight powertrains and even chassis systems, he said. EVs will have extra interior room because of the lack of an engine, and that opens the door for the use of additional plastics “for all the cool things you want to do in the vehicle interior,” Silberg said.
Plastics will also play a key role in exterior components, including the placement of LED lighting.
“You need plastic coverings, and you’re going to have all the sensors that go on the exterior,” Silberg said. “Plastics plays a big role in all of this. I think it’s going to be very exciting for them, quite frankly, with new markets, new opportunities, and great opportunities for innovation.”
Dan Hearsch, a managing director of management consulting firm AlixPartners and a leader in its automotive industrials practice, said his firm expects about one-half of cars by 2035 to be battery electric.
“On top of that, you’ll have some plug-in hybrid, but we think that once people really start to adopt electric vehicles, plug-in hybrid goes almost entirely away,” Hearsch said. “There will still be some hybrid, purely hybrid applications that don’t have the plug-in technology. That will be about a quarter of the market. That brings you down to like 20 percent of the market being purely internal combustion engines.”
While EVs are poised to become the majority of vehicles produced in the future, “there will still be cases for internal combustion engines,” Hearsch said.
There will be some applications — such as long-distance truck hauling — where battery electric vehicles won’t be practical until and unless the technology develops to where charging can be accomplished in a matter of minutes.
One big question that could influence the speed of EV adoption is how quickly infrastructure for recharging takes place.
“Consumer behaviors are going to be significantly influenced by the ability to charge publicly on the road, and in some regions, in their [consumers’] homes where the grids are not going to be up to this,” Hearsch said. “There’s a lot of stuff that has to happen in the meantime, and we think it will, but that’s part of why it takes so long.”
Like other experts, Hearsch said lightweighting car parts to address consumers’ “range anxiety” will play an important role in building sales of EVs. That will lead to continued development of new plastic compounds that improve strength and heat resistance, he said.
Another area of potential growth involves the development of conductive polymers that can be used in storage batteries, Hearsch said. So-called “plastic batteries,” made with electrically conductive polymers, could help make energy storage on the grid cheaper and increase the availability of renewable energy. However, such batteries would likely be too big for use in EVs, he said.
“For infrastructure, for energy storage and distribution, it could be ideal,” Hearsch said. “For more remote locations that are either more reliant on solar or wind, and where you want to store that power close to where it’s going to be used, you’ll need very large batteries of different types.”
PolyJoule, a Boston-based startup, has been developing technology using polymers that could offer a less expensive and longer-lasting alternative to lithium-ion batteries. The conductive polymers replace the lithium and lead traditionally used in batteries. The batteries also would avoid potential lithium supply issues.
MIT Technology Review in April 2022 described the PolyJoule technology.
The storage batteries could help deal with peak demands for electricity, Hearsch said.
“As cars advance, other parts of the architecture, particularly the interiors, are going to become more and more connected and digitized,” Hearsch said. “There will be more screens and all those other things, and those are also new and different applications of plastics.”
There are significant opportunities and risks for the plastics industry as companies move toward more sustainable business practices. As companies adopt ESG [environmental, social and governance] business practices, it will fuel the demand for using more recycled materials in cars and recycling more materials from scrapped cars, Hearsch said.
It’s been a challenge to recycle many of the plastic materials from junkyards, and the industry is trying to figure out ways to recycle more of those through processes including chemical recycling.
Bruce Geiselman, senior staff reporter
Contact:
AlixPartners, New York, 212-490-2500, www.alixpartners.com
KPMG International Ltd., www.kpmg.us
Plante Moran, Southfield, Mich., 248-352-2500, www.plantemoran.com
Bruce Geiselman
Senior Staff Reporter Bruce Geiselman covers extrusion, blow molding, additive manufacturing, automation and end markets including automotive and packaging. He also writes features, including In Other Words and Problem Solved, for Plastics Machinery & Manufacturing, Plastics Recycling and The Journal of Blow Molding. He has extensive experience in daily and magazine journalism.
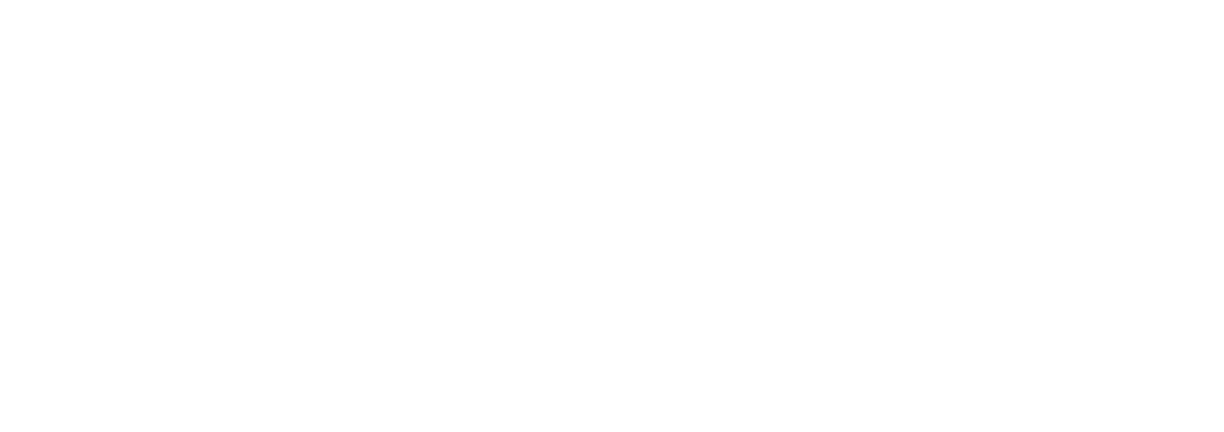