I recently wrote about serious problems with the U.S. power grid and how manufacturers should already be planning for higher prices and power shortages. The issue is worse than I thought.
My earlier story was the result of listening to a presentation at the Annual Blow Molding Conference by Clayton Penhallegon Jr., president of Integrated Services Group in Thomasville, Ga.
Penhallegon described how the traditionally centralized U.S. power system is designed to achieve a reasonable balance between reliability and cost. High-voltage transmission grids connect generating plants with large users such as cities or manufacturing plants with substations. A hub-and-spoke system moves electricity to decreasing voltage substations.
The power industry started to change after the 1970s energy crisis when retail markets were deregulated. Utilities and independent operators entered the market, Penhallegon said. Their services were mostly layered on top of the existing grid. The good news is that the cost for electricity came down.
Now, there is nationwide pressure to reduce carbon emissions by reducing coal- and gas-powered electricity generation. No problem! Solar and wind can take up the slack, right? Don’t bet your company on it.
The New York Times reported that more than 8,100 new energy projects — mostly wind turbines, solar arrays and batteries — are backlogged in an overwhelmed approval process. One large grid operator won’t take new applications again until 2026.
The American Clean Power Association said new installations declined 16 percent in 2022, primarily because of supply chain issues and lengthy delays in new project approval.
So, the cleaner energy from renewable sources that the nation needs could take longer than hoped to make a significant impact. Current wait time to get a project reviewed is about four years, according to the Times article.
There are multiple problems with having to wait longer to get a project reviewed. An investor who commits funds for a project could get tired of waiting. Construction costs go up. Options on sites can expire.
Once a project is reviewed, expensive surprises can crop up. If the transmission lines or the regional grid cannot handle the new capacity, the developer will generally have to spend millions of dollars more to connect the project.
The American Clean Power Association said in its fourth-quarter report that projects that would produce 53 gigawatts of electricity are currently delayed and projects that would have produced a total of more than 4 gigawatts were cancelled in 2022. Four gigawatts of power is enough to supply about 3 million homes.
Electric cars and electric heating and cooling systems in homes and offices are going to further stress the nation’s power grid. President Biden’s plan to fight global warming allocated $370 billion for subsidies to make clean energy technologies cheaper than fossil fuels. However, it does not address the interconnection obstacles for new power sources.
Plastics manufacturers need to think about future-proofing their power supply against rising costs, rolling blackouts, mandatory curtailments and short-interval disruptions.
I urge every plastics plant owner and key staffer to read the Times article and become involved with your electricity provider. The American Clean Power Association website at https://cleanpower.org also provides useful information.
A wind turbine or two behind the plant and solar panels on the roof might be good stop-gap measures, but I suspect the problem might be bigger than that. Manufacturers could be the first users to face energy shortages. Getting involved now could lessen the pain.
Happy birthday, Arburg!
Arburg GmbH celebrated 100 years as a company in February and threw a huge party at its Black Forest headquarters in Germany to celebrate.
Privately owned Arburg was established in 1923 at the home of Arthur Hehl, who at one point manufactured precision surgical instruments. His son, Karl, built an injection molding machine for the company’s in-house use in 1954 and by 1956 Arburg was manufacturing presses to sell.
Arburg is a technology leader in plastics processing equipment. It pioneered microprocessor controls and hydraulic proportional pressure-control valve technology, on-screen controls, the first manufacturing execution system specifically for injection molding companies and a 3D printer.
At its celebration, the company unveiled two new injection molding machines (Page 30).
The plastics industry is fortunate to have companies like Arburg and its competitors continually pushing the envelope on processing technology. It makes all processors’ work lives better.
Ron Shinn, editor
Ron Shinn | Editor
Editor Ron Shinn is a co-founder of Plastics Machinery & Manufacturing and has been covering the plastics industry for more than 35 years. He leads the editorial team, directs coverage and sets the editorial calendar. He also writes features, including the Talking Points column and On the Factory Floor, and covers recycling and sustainability for PMM and Plastics Recycling.
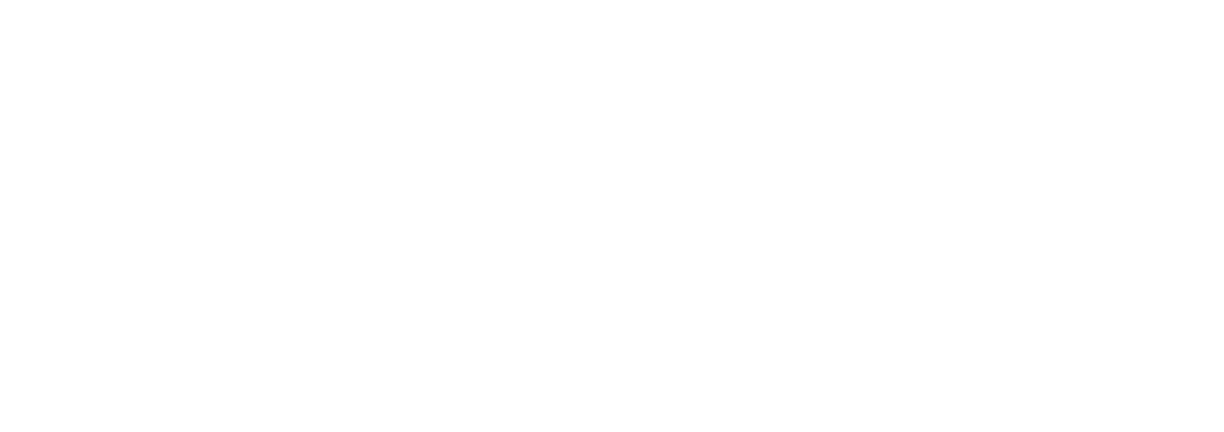