Have you found an innovative equipment solution to a plastics processing challenge? Let us know.
Problem: Reprogramming a cobot for each new job was daunting for a small-volume molder.
Solution: An add-on called FlexxReference has simplified the task of setting up cobot movements.
By Karen Hanna
For a processor that rarely runs recipes longer than a week, the challenge of automating downstream tasks was vexing.
Sure, a robot could be programmed to handle a particular job. But once that work order was complete, what would the robot do? And who could guide it through its next assignment?
That was the obstacle confronting Jon Gelston, president and owner of Aim Processing, and his team after the custom injection molder acquired its first UR5e cobot from Universal Robots. The company, which began getting serious about automation in 2018, was impressed by the cobot’s performance after initially deploying it, but found reprogramming it took hours — and employees, concerned they would break something, were reluctant to work with it.
“Trying to find an automation platform that was modular, could be redeployed, could be redeployed by a variety of individuals in the company — not just the one person who knows how to do it — was really important to us,” Gelston said.
At a company that handles annual individual part runs of 5,000 to 50,000 units, flexibility is paramount. Like other manufacturers, the Longmont, Colo., processor has struggled to find workers, even in the midst of a growth spurt that began when Gelston took over in 2006. At that time, it employed about a dozen people and had just five machines; now, the workforce numbers about 40.
One key, Gelston said, “has been recognizing where you excel, where you can be competitive and trying to stay within that capability set. .... The hard part’s trying to avoid all of the tempting work that’s just outside your capabilities.”
For Aim Processing, which makes about 1,400 different parts, the sweet spot centers on small parts. Most of its 37 presses have clamping forces of 55 to 110 tons, manufacturing parts that weigh between 10 and 20 grams, ranging in size from a fingernail to a human hand.
The company processes more than 700 materials, mostly ABS and PC. A big part of the company’s portfolio comprises electronic enclosures.
With press-mounted, three-axis servo robots on each of its injection molding machines (IMMs), the company has been working to show its customers they don’t need to go overseas for parts. In one instance, it landed a job previously performed in Vietnam.
Investing in cobots is one tack in trying to find “new ways that we can be competitive on a global sense,” Gelston said.
In an effort to fully capitalize on the plant’s UR5e, Gelston sought advice from Seth Leinbach, a sales engineer for UR cobot distributor In-Position Technologies, based in several Western states. According to a case study provided by UR, Leinbach immediately proffered a solution: “Right away, I thought it was a perfect fit for a UR+ solution by Flexxbotics called the FlexxReference,” he said.
Designed by Flexxbotics, Boston, FlexxReference is a UR-certified hardware and software add-on that simplifies the task of establishing new set points for a cobot’s movements.
“If you never change your application or don’t move your cobot around, you most likely won’t need this,” Flexxbotics CEO Tyler Bouchard said in the case study. “But we’re seeing an emerging trend of UR cobots not dedicated to one task only. The cobots lend themselves so well to many types of applications, so we came up with the FlexxReference as a productivity tool to achieve quick redeployment, enabling the operators to simply move the cobots to where they are needed that day.”
The process can take just minutes.
“Basically, it is establishing more or less a zero point where every waypoint and position that you teach are relative to that … zero point,” Gelston said. “What may change is that robots reset up, let’s say the second time you run it, it may be a millimeter to the left or a millimeter to the right, or whatever, but, as long as you reprogram where that zero point is, all the other points update in relation. Instead of reteaching 30 waypoints, you just are reteaching one, and it is just so much faster and really less prone to error or, more importantly, damage.”
Multiple Aim Processing technicians have learned how to use FlexxReference, so cobot redeployment has become fast and easy — with no worries anymore that a cobot could be positioned in a way that might cause issues.
It’s worked so well, the company has invested in a second UR5e, and it has expanded the range of applications it’s tried to automate — everything from tending IMMs to stacking trays, picking parts off conveyors and packaging parts.
At least one application involves a reshored job handling parts that required a little extra TLC, according to Gelston.
Overseas, the part was protected with special film. At Aim Processing, that process was cost-prohibitive, so the company changed it up.
“We are using a cobot to handle, secure packing trays that guard the product, but only need to be called to task every 8 minutes,” Gelston said.
The cobots’ productivity means they don’t run constantly. In February, when Gelston spoke to Plastics Machinery & Manufacturing, only one of the two cobots was at work in the 24/7 plant.
But Aim Processing — which realized a return on investment for its cobots within six to nine months — isn’t ruling out the eventual adoption of even more automation.
“As we have improved our skill with it, we can drive greater utilization, and I think that payback will only continue to come in closer,” Gelston said.
Karen Hanna, senior staff reporter
Contact:
Flexxbotics, Boston, 877-456-1576, https://flexxbotics.com
In-Position Technologies, 877-478-3241, www.iptech1.com
Universal Robots USA Inc., Ann Arbor, Mich., 844-462-6268, www.universal-robots.com
Karen Hanna | Senior Staff Reporter
Senior Staff Reporter Karen Hanna covers injection molding, molds and tooling, processors, workforce and other topics, and writes features including In Other Words and Problem Solved for Plastics Machinery & Manufacturing, Plastics Recycling and The Journal of Blow Molding. She has more than 15 years of experience in daily and magazine journalism.
Request More Information
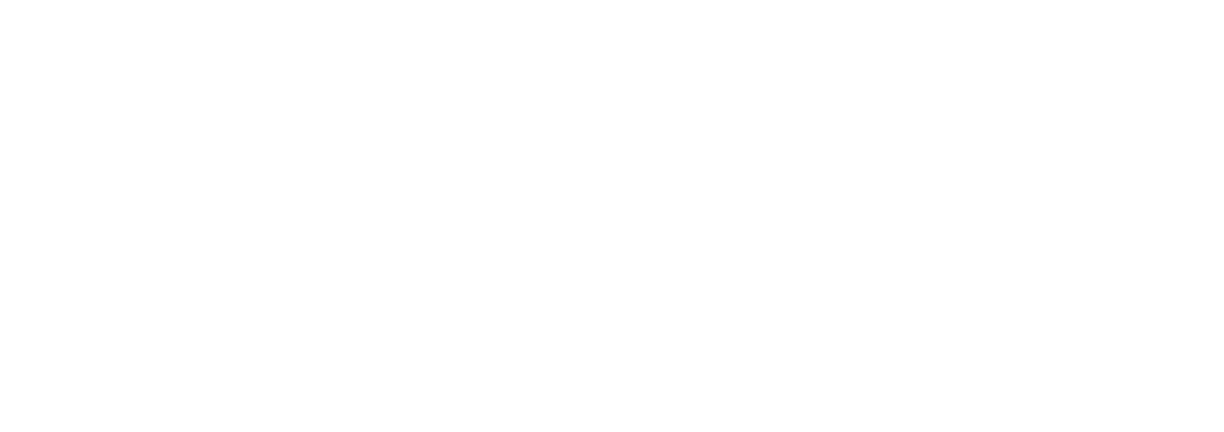